
BasicAirData Air Data Boom
Triggered by some chat around the net I post here some material about mechanical wind vanes design.
Angle of attack measurement by means of wind vanes will be first introduced. The topics to be covered in this miniseries are design, practical issues and modeling.
Angle of attack (AoA) instruments measure the angle between the airspeed vector and a predefined line on a cross-section of the airplane wing. This line is usually selected either as the zero-lift line or the chord line of the airfoil. AoA is often indicated by the Greek letter alpha. This angle is often used to calculate the lift of said wing section. AoA vanes are also called alpha vanes.
AoA usually changes across the wingspan of the aircraft and this is something one should take into account. A visual example is a wing which twists progressively across its span, flying straight and level. The AoA at the wing root differs from the AoA at the wing tip by the wing geometric twist term.
AoA measurements are are useful for parameter identification, general aviation planes or even to FPV pilots of RC-aircraft, since they can be used as an early warning indication as the vehicle approaches stall. The use case affects the choice of the AoA sensor type and desired performance. There are many types of AoA measurement devices, of which the most common are:
- Wind vanes;
- Null seeking devices;
- Static-type devices, based exclusively on pressure measurement.
For a general description of these typologies, please refer to NACA-TN-4351.
In this section we will focus on a classic mass-balanced wind vane design. Even though it is less attractive than a pressure-based unit or closed-loop null seeking device. Making and calibrating a good wind vane is well-withing the reach of a DIY maker. The wind vane visible below is made by Basic Air Data members and visualizes the main components of the system. A rendering of the completed assembly of the vane can be seen in figure AoA 2.

Figure AOA.1 - Miniature DIY Wind Vane detail (JLJ and GC);
Caption - 1 Counter weight, 2 Fin, 3 Main rotation shaft, 4 Bearings,
5 Potentiometer, 6 vane body
Equally important to the instrument itself, is the definition of the quantity under measurement: an adequate design requires stating specifications beforehand. Initially, our focus will be turned towards common design aspects and then some specifications will be proposed. A lot of bibliography can be found regarding weather vanes specifically; in principle, it's a valuable resournce but not very helpful when it comes to design requirements.
There are two main macroscopic differences between weather vane and alpha vane applications: range of speeds and the vane support structure, which is needed to isolate the instrument from vibrations degrading measurment quality. Imagine a wind vane fixed on a cantilever beam. In such configuration, which resembles a nose-mounted airboom, the whole structure may start to oscillate. As a case study, we will consider a planar oscillation (ref eq.36).
Given the height of the wind vane mounting point, h, and its airspeed, u, the error angle caused by beam deflection can be calculated as:
wind vane mounting point can interact with the wind vane dynamics. To avoid performance degradation it is crucial to maintain the resonant frequencies of the two systems well apart.
Since the air-boom doesn't have a simple geometry, the calculation of the vibration modes is not feasible using a closed form formula.
A 3D model needs to be created in a computing environment and FEM modal analysis be carried out. Alternatively, lab tests are also a way to obtain such data. Figure AoA 3 depicts the first mode of the probe. Elmer is a notable open FEM package that can be freely downloaded and can handle dynamic analysis.
Generally speaking, the stiffer the airboom, the higher its first resonant frequency will be. Higher airboom resonant frequencies are desirable, since they present an uppper performance limit for the wind vane. As a rule of thumb, if the airboom assembly moves under a slight force of the hand while while fixed on the ground, some vibration-related problems are to be expected.
More accurately, if numerical analysis tools is available, make sure that the first resonant frequency of the airboom is far from the desired wind vane operational range. An offset of at least 0.3 times the first mode frequency is a good, conservative value.
Resonant frequencies of higher order can be usually neglected, as they carry significantly less deflection energy. For best performance, it is always a good idea to make sure that to other vehicle components create excitations in the low to mid frequencies of the wind vane.
Let's proceed by examining wind vane behavior; refer to figure AoA 1.
The most critical component are the bearing. A Coulomb friction model will be used to describe their static friction.
The phenomenon of static friction, or stiction, results in the torque that is necessary to start rotating a resting bearing being greater than the torque required to keep it rolling. A graph representation of this phenomenon is found in figure AoA 4. This non-linearity leads to some problems when it is incoroporated in numerical integration algorithms.
Firstly, longer integration calculation times are to be expected. Furthermore, limit cycles and solution collisions may be generated, in other words the solution may be non-steady/cyclic or converge to a terminal value that yields a non zero static tracking error.
Analysis can become much neater if the model is writen down as a Filippov system: a nice, sliding bifurcation arises.
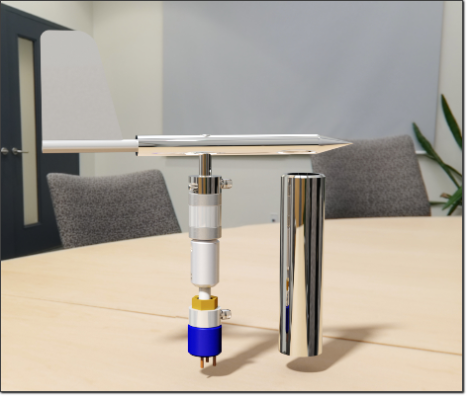
Figure AOA 2 - Miniature DIY Wind Vane 3D model (JLJ and GC)

Figure AoA 3 - Modal analysis on the probe, first mode frequency is 106Hz.
The probe is fixed at the root. The Maximum deflection at the tip 3 is 25 mm, 16 mm at the 2 windvane fixation point and 0 mm at the root 1.

Figure AoA 4 - Bearing friction model including stiction
Many articles are available on the wind vane topic, for example: J. Wieringa (1967), Evaluation and Design of Wind Vanes, Royal Netherlands Meteorological Institute, De Bilt (Download link)
Commonly, the vane dynamic behavior, at least near equilibrium, can be assimilated as one of a second order underdamped system. Standard industrial methods for determining the dynamic performance of a wind vane also exist, for example ASTM—D5366 “Standard Test Method for Determining the Dynamic Performance of a Wind Vane”.
Comments
Jose nice article. What type of ball bearings are you using in the design of your wind vane; angular contact, or deep groove? I would think that a high quality matched pair of angular contact ball bearings with a light spindle oil lubricant and pre-loaded with wave springs to prevent any axial play or movement would be ideal. Unfortunately these bearings are rather costly even at the sizes you are probably using. But standard deep groove ball bearings would definitely exhibit a measurable axial movement which i feel could contribute to further measurement inaccuracies. Just a thought. Anyway nice article.
-Brian