Round tubes offer the following pros:
- handle twist better than square tubes. Thus for the strength, are far lighter.
- are more readily available (pipes, tubes, arrows, kite frames, golf clubs and sticks of all materials).
- easier to cut (square tubing can twist and be damaged by cutting forces)
- easier to peg (fits into a drilled hole and easy to find extenders)
- less expensive
Round tubes are thought to have the following cons:
- difficult to mount motors
- difficult to join
None of the cons are real if you know how to work with tubes. Mounting round tubes to motors is easier and faster than with square tubing. Round tubes are also faster and easier to join together. The resulting joins are also far lighter and better.
In the H-frame forum, I was asked to share these build techniques so have decided to demonstrate the methods on the most complex multi-copter one can build, an Octa-V. I'll do this step by step. The result will be a multi-copter that reduces frame, screw, gusset, and motor mount weights by more than 40%.
The steps will be Design, Assembly, Charmin Test, and Flight Test
Installment 1: Design
First, both simple and complex multi-copters share something in common. When using round tubes for arms, there is no reason to cut a perfectly good tube in half for each arm. And then add a bunch of weight and fasteners to hold the halves together. How this is done will become evident in the third installment, the Charmin Test. For now, just know that each tube is continuous (no breaks, no joins). Opposite rotors share the same boom in a quad, hexa, or octa. All of those fasteners are gone. The cross beams on a V or H are also continuous. Assembly and disassembly is quick.
Most quads are so simple that one grabs two pieces of wood the same size and slap them together. Done. If the angle of view isn't good, just move the camera forward a bit. But, if you want to know the exact length of a quad boom based on prop diameter and platform size so you can minimize weight to get longer flights, then I've attached a worksheet that does the math.
An Octa V is a bit more complex. It is specifically used for camera work. So you need to optimize the motor boom angle and aspect ratio of the frame to achieve the desired Field-of-View for the camera (void of propellers), It also uses 8 motors so that if one dies, the copter can return to the ground with the $12K of camera/lens in tact. You also need to minimize platform vibration, so the platform needs to be large enough for the electronics, gimbal mount, and at least 1.2" (30mm) from the prop radius.
I've attached an Excel worksheet that does all of the calculations for optimizing weight. There is an instruction sheet if you want to ever build one and calculations for a Quad X, Quad +, Quad Spider, and Octa V.
The next installment will be Assembly.
P.S. I'm not experienced nor am I an expert. I'm just a tinkerer like many of you. There are builders out there with far more experience and wisdom. I'm hoping that this blog will allow us all to share ideas on building strong, fast, and light not only for initial build, but also for crash repair.
Replies
Good idea. Will look into it, thx.
wow! unreal. great build methods using CAD and verification with fundamentals. simplicity at its best.
Hey!
Very nice builds you did there using tubes and glue only!
Allthough the Gimbal looks really good!
I did two similar builds some time ago. 2 Gimbal Quads at ~500g AUW.
LightFlight 1:
465g incl Gimbal und Innovv C1 HD Cam
http://der-frickler.net/modellbau/planes/lightflight
~12min of Flighttime
And LightFlight 2 - Still in development
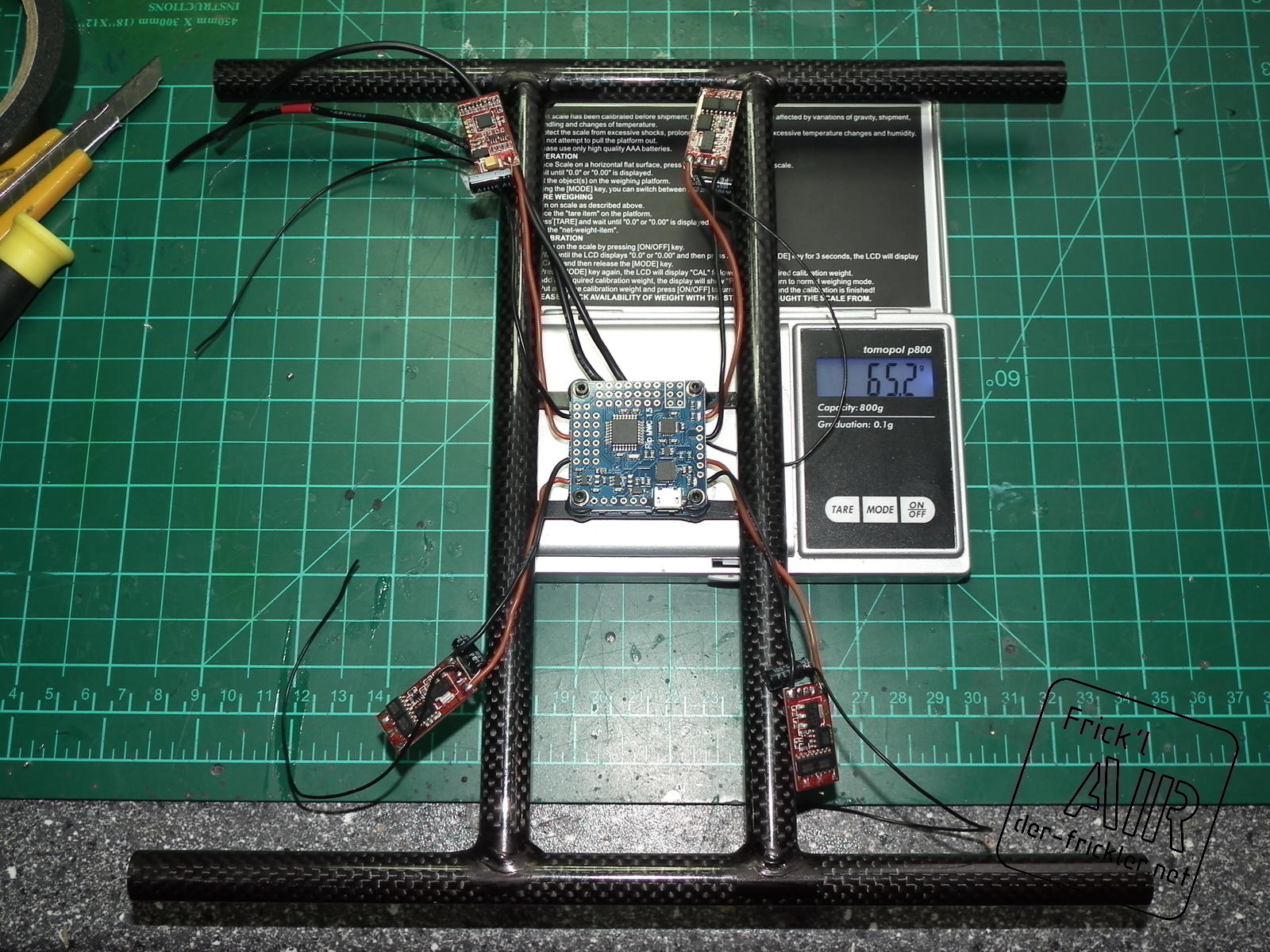
http://der-frickler.net/modellbau/planes/lightflight
~550g with 3 Axis Gimbal and SJ4000 Cam
Flighttime not yet determined.
The Gimbal to be used at the LightFLight 2 is the same i build for my Minimalist - just without the landing gear.
http://der-frickler.net/modellbau/planes/minimalist
The tubes i used are spare tail tubes from the hobbyking 450 heli. They are quite cheap and very light due to 0.5mm wall thickness
gorgeous work! keep us posted on progress.
Hi Forrest, Jon,
FIY blog published here.
(Forrest, what's the guiness book process if we wanted to officialize a world record ?)
I will post some build details in this thread once my camera is charge and I get back to my damned pictures!
I'm finishing a delivery for a customer so I do not have any time for the last week to work on my own projects. I'll be back soon...
Don't worry Huges audience waits for you ;)
Hi Forrest,
I need your advices on using a nomex sandwich panel. I would like a rectangular piece of nomex to be the pixhawk plate, elevated one or 2 inches above a cf plate. I am logically thinking of using nylon pillars (spacers) to elevate this nomex sub-plate above the cf plate. However I wonder what the best method would be to fix the four nylon pillars on each corner of the nomex sandwich plate? Would I drill four holes in the nomex sandwich and pour 3M2216 epoxy around the pillars placed vertically in each hole?
PS : I'm starting to get my bench back in order after the renovations work (sometimes wife is disrupting the hobby...) and I will finally move ahead on the gimbal and 60+ minutes CF frame projects....
Another possibility is to drill a 3mm hole in the Nomex. Cut the head off a 3mm nylon bolt, say 16mm in length. Slide the nylon thread through the hole in the Nomex, screw the nylon thread into the spacer below with nylon washer in between. Attach a nylon washer and nut to the nylon thread which should be sticking through the top of the Nomex.