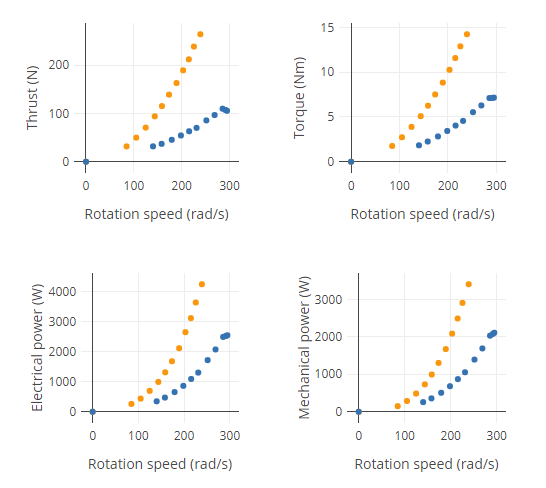
I will discuss the challenges of designing this database. Searching for the right propulsion components for a UAV is tough. There is not much data available, and what is available from suppliers is not standardized or reliable. Even with the right tools, you still have to buy and test many components before finding the right motor and propeller. My team and I have extensive experience with dynamometers, so we have a good understanding of the issues, but we still had some serious challenges when designing a database.
Racerstar BR2306S 2400kv and DALPROP 6040
Dynamometer tests produce a lot of data. This data is very sensitive to the test conditions. The first obvious challenge in a user-contributed database is figuring out how to create a standardized test environment. There is, unfortunately, no international standard on propulsion test for small UAVs. I can say from personal experience with hundreds of businesses and universities that everyone does it differently. It is also not possible to record the entire test environment, so we cannot only use software checks. In the end, we came up with multiple solutions to minimize the variance between the test. First, we developed a strict test procedure and environment with a checklist. Second, all the tests are done with a script and uploaded automatically to minimize the risk of operator error. Third, the test script has multiple checks to test for data consistency. Finally, all the test data is available in the database and we encourage people to upload pictures and comments, so other users can verify the data accuracy and comment on it. We intend to implement a voting system so more people can help catch incorrect data.
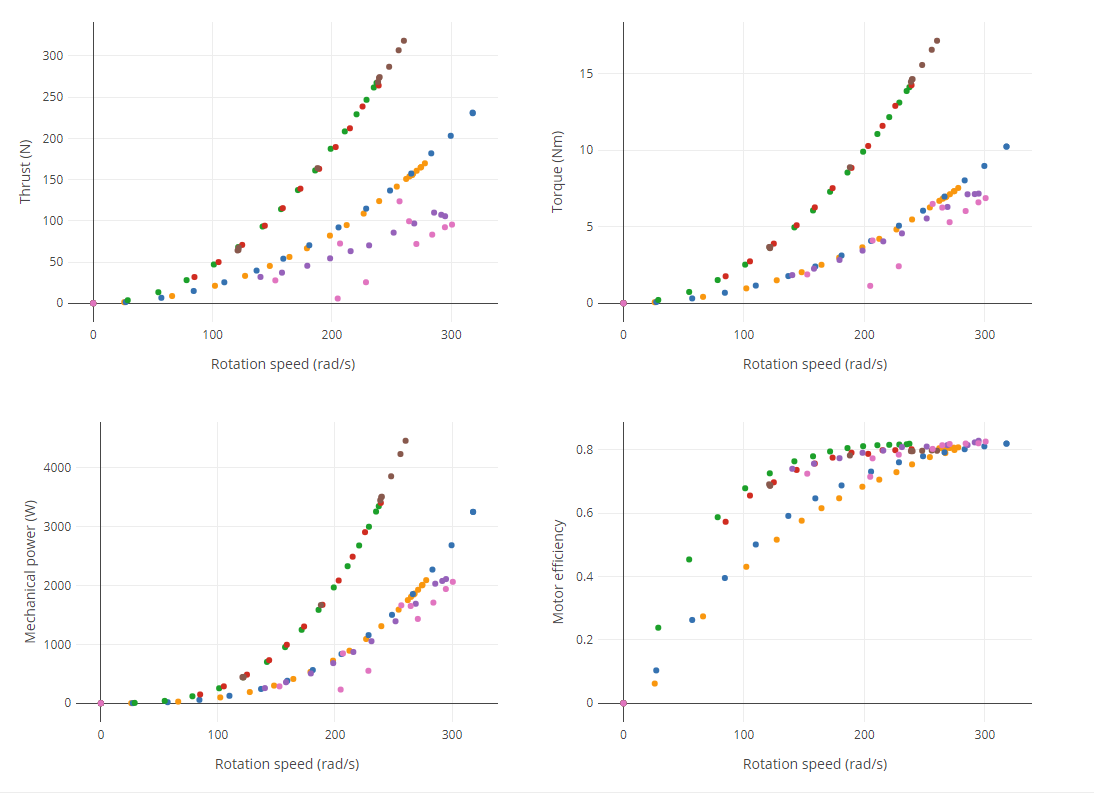
Sample Data for the Xoar TA130-25 KV80
Another challenge is regarding sorting and categorizing the data. We developed a component-test model where each component can be associated with multiple tests, and multiple tests can be associated with multiple components. For example, this coaxial test has two motors and two propellers. If you click any of the components, you can see all the tests that were done with this component. This test-component model is important for data analysis. You can already see the data plotted on each component and test page, but it is possible to do more. We are working on an analysis module that will allow you to extract the fundamental motor and propeller parameters (Kv, i_0, C_t, C_p, etc…) from multiple tests. Those parameters will also be searchable.
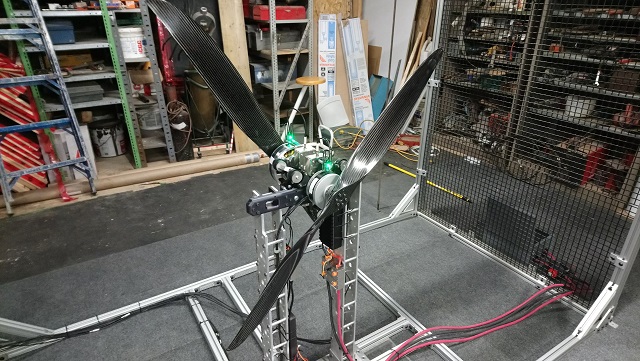
The data in the database will always be freely accessible if contributors choose to make their data public. We are planning a model similar to GitHub where users pay only for private components hosting and analysis. We currently only support RCbenchmark test tools, but we are definitely open to supporting other tools if other people develop motor and propeller dynamometers.
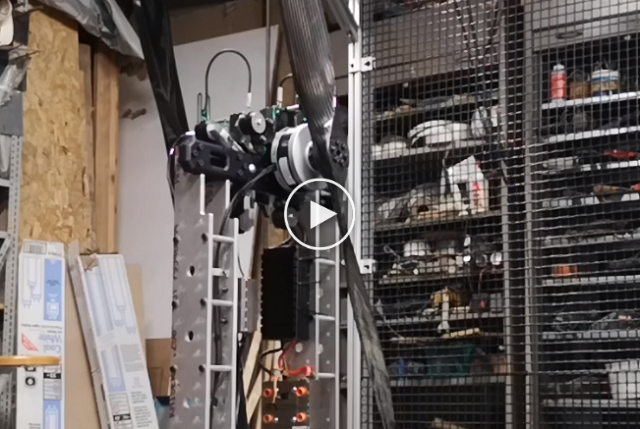
Test of the Xoar Coaxial 47 and 40 inch prop
Next on our list of feature is display unit selection, advanced analysis and search, and an option to share embedded graphs on forums and websites. I invite you to browse the database and submit feedback! The database is still in alpha, so some features are missing, but it is already useable for searching, categorizing and data analysis.