As the world's primary fuel sources, oil and natural gas are major industries in the energy industry and have a significant impact on the global economy. Demand for petroleum and petroleum products has only increased in the recent past due to global economic and population growth, as well as continual urbanization and industrialization.
The United States itself has more than 190,000 miles of liquid petroleum pipelines and over 2.4 million miles of natural gas pipelines. Pipeline transportation is safer, more efficient, and emits fewer GHGs than shipping by ship, truck, or rail.
The Current Challenges with Pipeline Inspections:
Pipelines are vital infrastructure for the transmission of oil and natural gas, connecting producing areas to refineries, chemical plants, home customers, and commercial demands. However, oil and natural gas are combustible and explosive substances that are typically delivered via high-temperature, high-pressure pipeline networks. Hereby, it is critical to monitor these pipelines to ensure that they are operating effectively.
However, traditional pipeline inspection methods have some issues, such as:
Use of crewed aircraft
Currently, the majority of energy companies use helicopters to monitor encroachment in potential pipeline Right-Of-Ways (ROW). Each expedition costs an average of $150,000, making more regular inspections than every six months almost impractical.
Foot Patrols
Once the aircraft confirms an encroachment, foot patrols, typically consisting of two personnel, are dispatched to these remote locations. Such manual site inspections take approximately 8 hours and cost approximately $500 merely to have a closer look and validate the threat.
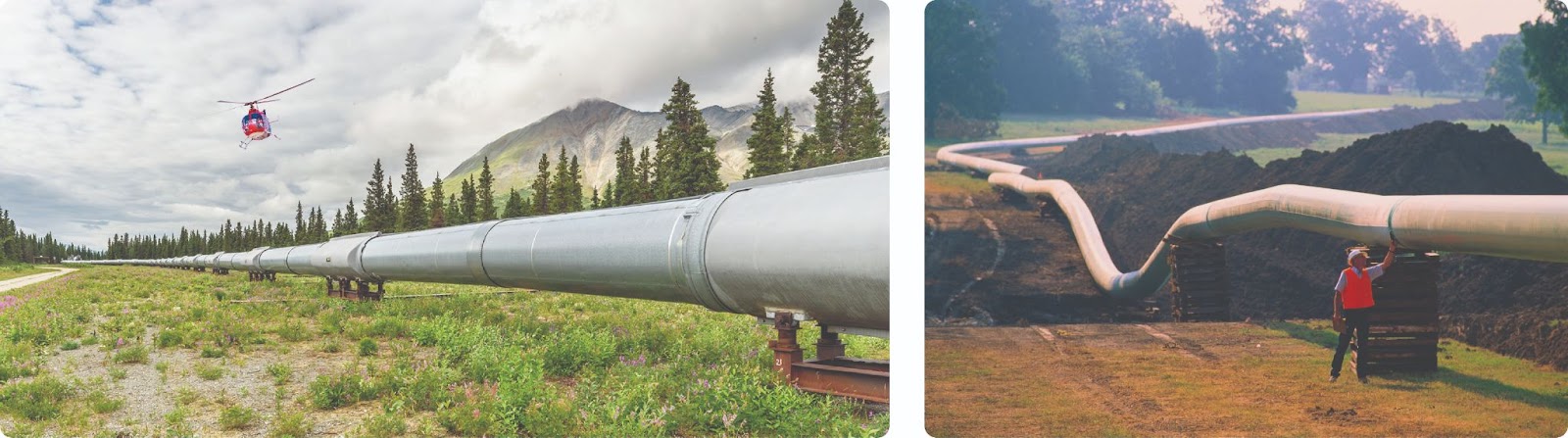
Inability to send crew at all times
Pipelines can be hundreds of kilometers long and can be spread over vast remote locations. Sending operators to such locations can put human life at risk. Hereby, it becomes quite difficult to send inspection teams to cover such areas at all times.
Time-consuming method
Traveling from one asset to another is frequently difficult. Operators may need to drive lengthy miles along gravel or dirt roads to visit several inspection sites. The distance and hard terrain may need a significant amount of time.

How can Drones with BVLOS Capabilities Help Oil and Gas Companies Secure Pipelines
Ease of travel between assets
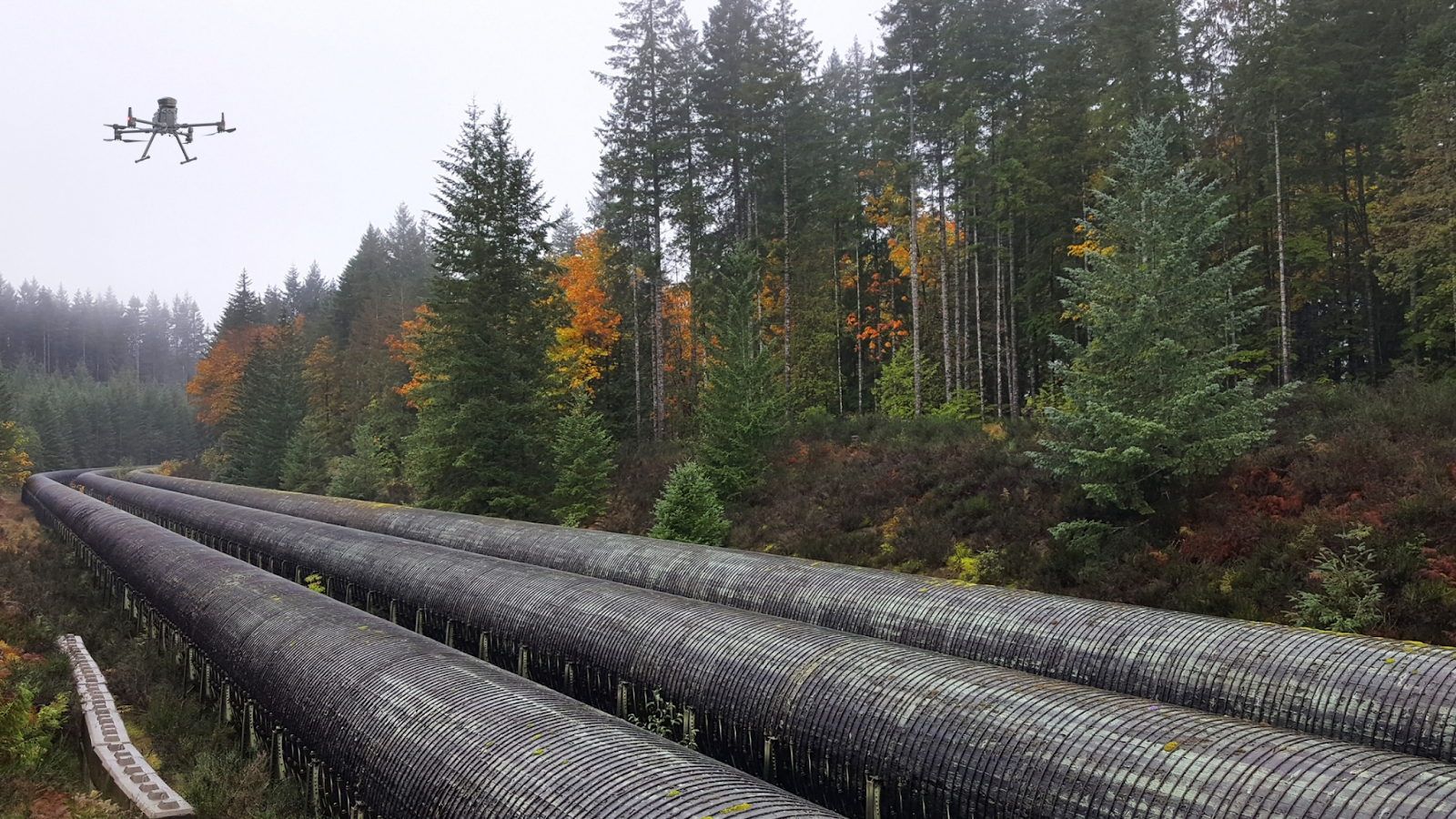
Traveling between assets during inspection operations might become challenging because these pipes can span thousands of meters. The team may be required to travel long distances and to distant regions where there is no adequate road infrastructure.
Operators must travel to the sites, assess the asset, review their data, and then drive to another asset. Furthermore, they must repeat the entire process until all assets have been inspected. This can take a significant amount of time which can be costly for an industry like oil and gas.
However, drones can travel vast distances and reach difficult-to-access locations. Additionally, using drone-in-a-box systems, eliminate the need for continual re-launching, packing, and landing of drones which is majorly faced in manual-led VLOS operations.
Increase worker safety
Oftentimes, assets are located on high terrains or difficult-to-reach locations. Operators may need to set up substantial scaffolding or dangle from ropes to inspect this equipment. Any mistake here can result in severe consequences. Despite the industry's strict regulations and safety standards, health and safety concerns persist. A BVLOS operation eliminates the operator's danger by allowing them to undertake the flight mission from any remote location.
Simplify early detection of pipeline leaks
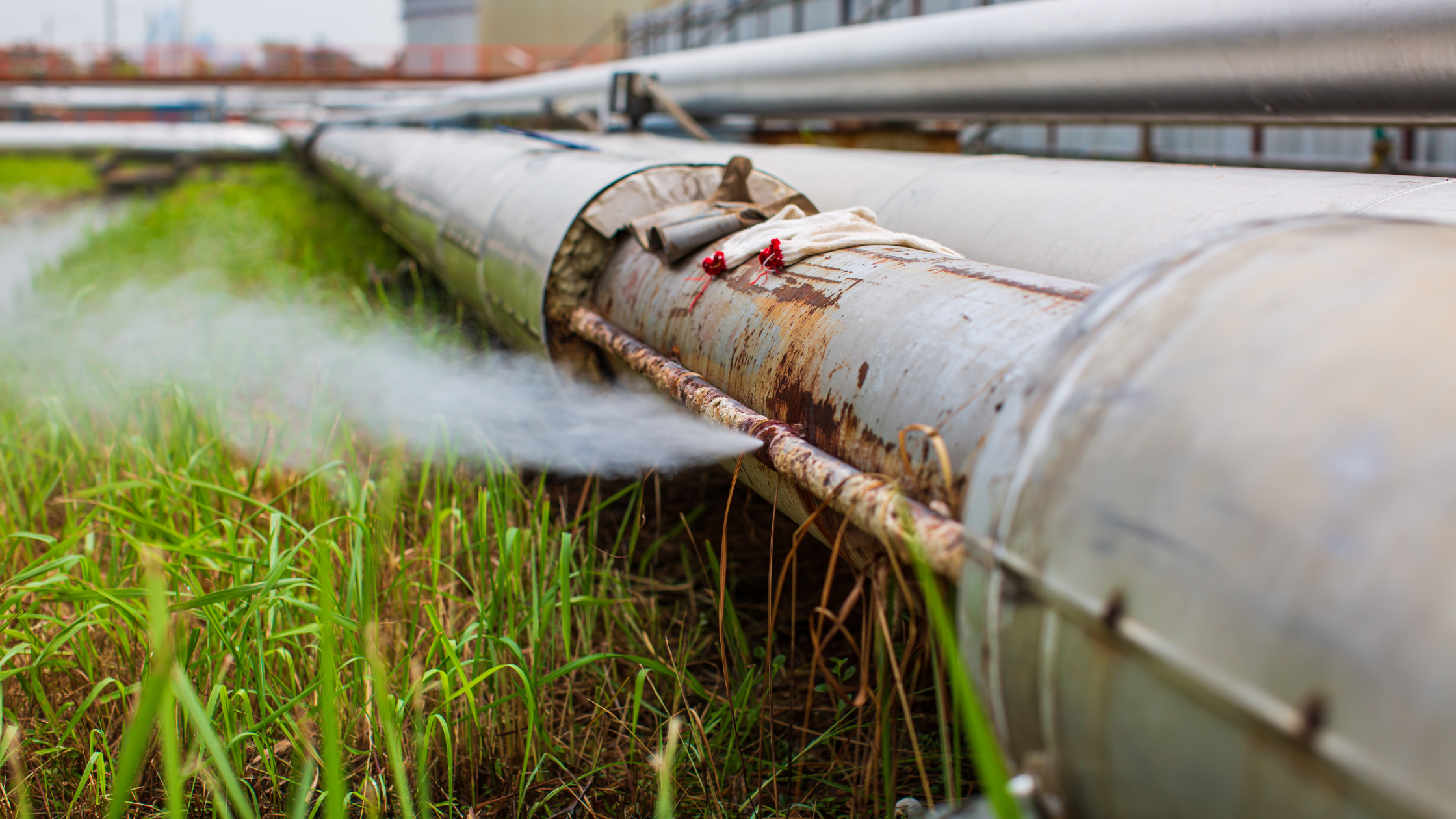
Drones are increasingly being used in the oil and gas industry for early detection of pipeline leaks. By using advanced drone technology including thermal cameras and visual or infrared cameras, these drones help the operators to identify gas leaks in storage tanks and pipelines with greater accuracy and efficiency than traditional methods.
These drones can easily access hard-to-reach areas and capture high-quality photos and videos of the pipelines and storage tanks. These data can be helpful to conduct image analytics for accurate and early detection of potential leaks or damage.
This allows operators to respond quickly and effectively to potential pipeline failure, minimizing the impact on the environment and reducing the risk of accidents. The use of drones also reduces the potential for human error, as operators can monitor the pipelines remotely, without the need for physical inspections.
Reduce heavy costs
Hiring a pilot and a helicopter, for example, can cost thousands of dollars. Regular inspections may become prohibitively expensive and time-consuming. Autonomous drone missions can minimize such costs while also minimizing human dependency.
Utilize readymade data and analytics via automated procedures
A human-led operation requires the operator to drive to the location and visually inspect the asset. Via autonomous operations, drone operators can run pre-planned drone flights and augment the inspection process. The drone will follow its routine, capture and store data which can be further assessed for detailed inspection as per need.
This enables the operator to quantify their assessment with turnkey data and analytics delivered via automated workflows. This simplifies the entire process and backs it up with data, which greatly aids decision-making.
Ability to scale operations
While examining pipelines spanning thousands of kilometers, it becomes nearly impossible to conduct manual operations consistently. However, autonomous drones can be scaled up and deployed readily to fit the business's needs as they can be programmed to conduct the desired tasks.
How FlytNow is Enabling BVLOS Operations
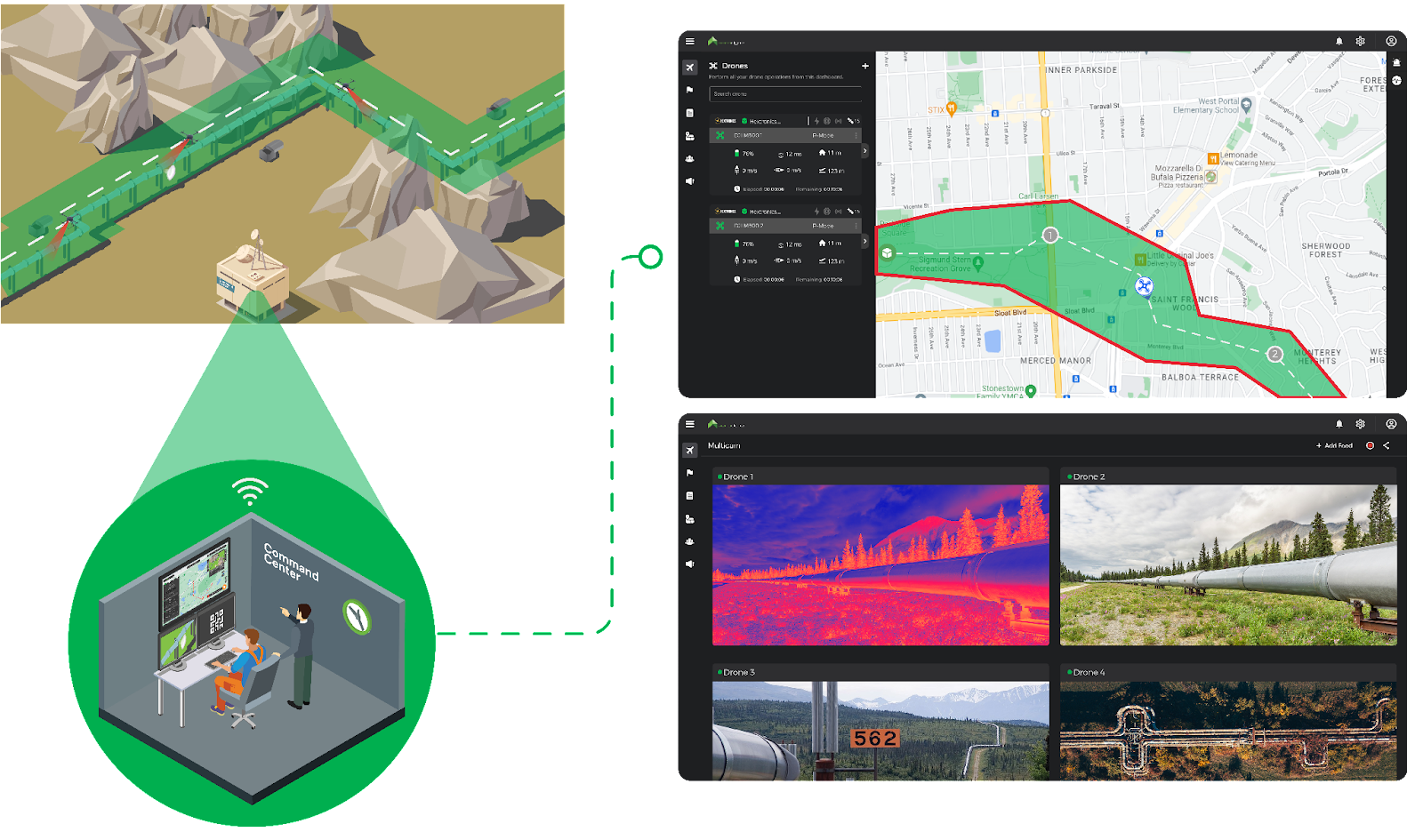
FlytNow is a cloud-based solution that enables the deployment and management of drones in just a few clicks, allowing you to manage your drone operations via a single web-based dashboard for a seamless experience. It helps you lower travel costs, reduce operation rounds, and increase productivity by saving travel time. It is integrated with ready-to-use intelligent modules, like collision avoidance, and precision landing, and integration with drone-in-a-box systems, which further helps you shorten your time to market.
The FlytNow software solution enables project managers to schedule pre-planned or on-demand flights from a command center located miles away from the base station. The drone takes off from the drone nest autonomously, flies its mission, captures real-time videos and images, and uploads them to the cloud.
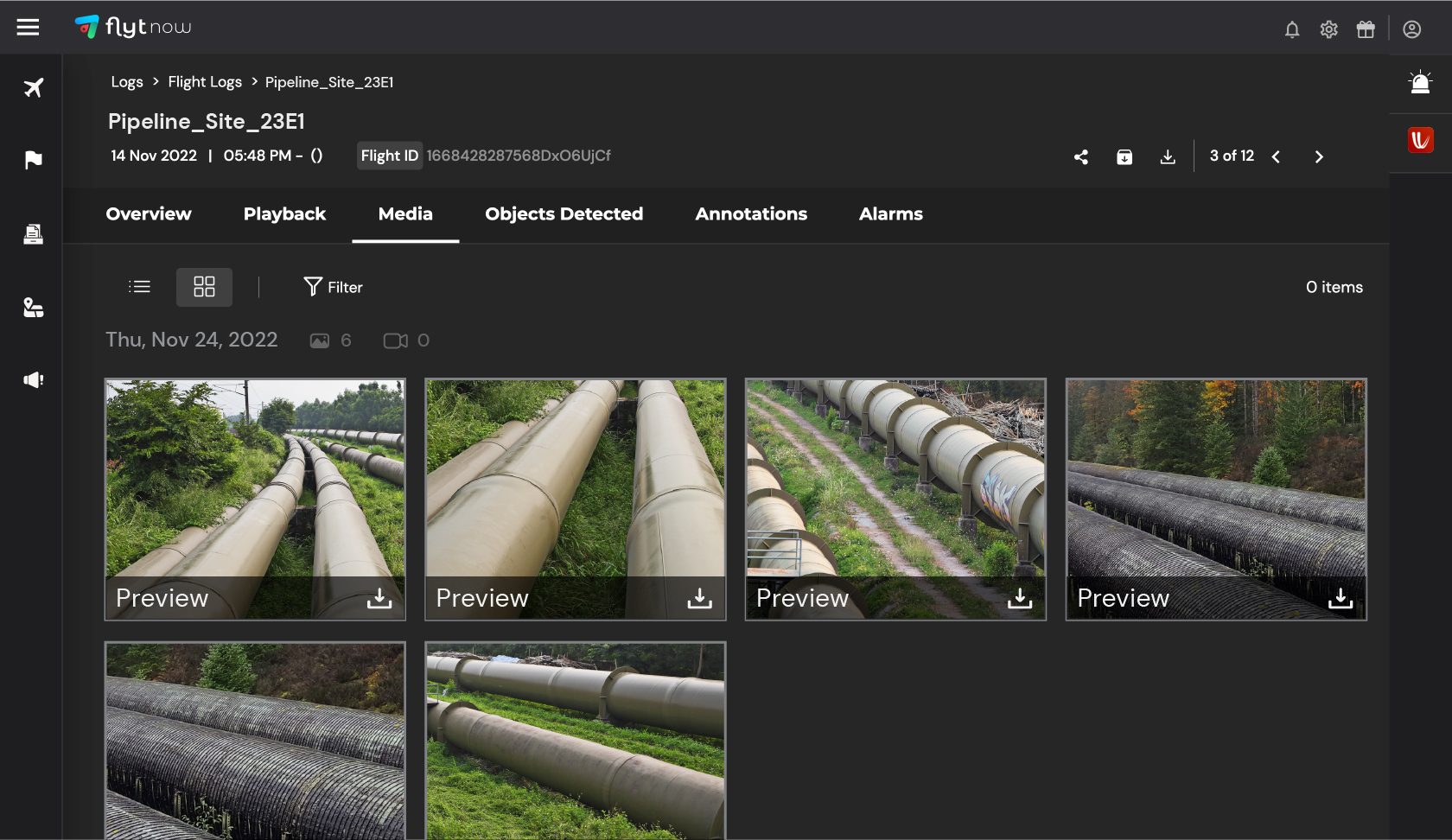
Following the flight, the drone returns to the docking station for battery swapping and storage. These stations can charge up to four batteries simultaneously and swap out the existing battery in less than 90 seconds, ensuring minimal downtime. Furthermore, because it is lightweight, it can easily fit on the back of a pickup truck and be moved from one location to another if necessary.
3rd party integrations in FlytNow, such as Casia G system by Iris Automation for detection and avoidance of cooperative and non-cooperative aircraft, Altitude Angel for airspace awareness, and others, assist to increase capabilities for greater insights and seamless BVLOS operations.
Leveraging Nested Drone Systems (NDS)
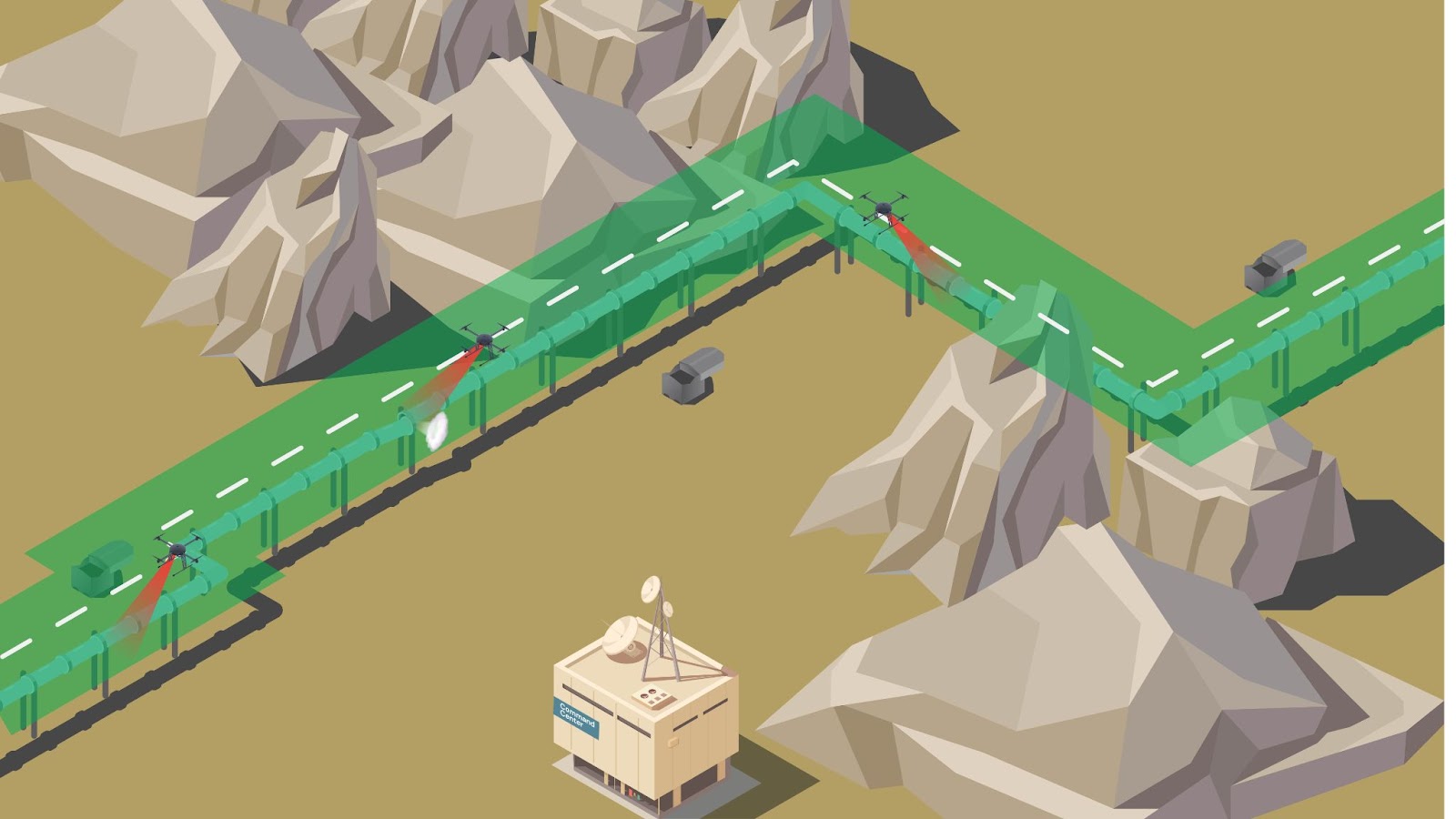
The Nested Drone Systems (NDS) can significantly improve the data collection process and transform how pipelines are inspected. It lets the drone operator conduct long-duration flights without the need to return the drone to the command center to recharge or swap the battery. With the nested drone system, energy companies would be able to quickly scale up, undergo a digital transformation, run safely, and boost productivity.
Nitin Gupta, Founder & CEO of FlytBase, Inc. concludes by stating that “Nested Drone Solutions are rapidly revolutionizing the way repeatable, high-frequency missions are conducted across use-cases. Maintenance of pipelines, spread over thousands of miles, is a great application of this technology with a significant ROI for the end-user.
FAQs
1) How can drones improve the safety of inspections on oil and gas pipelines?
Drones can play a vital role in improving the safety of inspections in the oil and gas industry. With their ability to fly closer to the ground, drones can provide high-resolution aerial data through the use of visual or infrared cameras. This allows for more precise and thorough inspections of pipelines, particularly in hard-to-reach areas.
By using drones, workers can avoid the potential dangers of inspecting pipelines on foot, such as exposure to crude oil leaks. Additionally, the use of drones allows for earlier detection of leaks, which can prevent potential disasters and safeguard the environment.
2) What are the benefits of using drones for pipeline inspections?
Drones provide several benefits for pipeline inspections, including accuracy and improved technologies. Using drones to detect leaks and identify potential issues can save costs and equipment compared to traditional inspection methods. Drones can also access dangerous terrain and provide quick emergency response.
In addition, using drones for regular inspection can improve worker safety by avoiding the need for workers to enter hazardous areas. Visual or infrared cameras on drones can monitor pipelines and identify potential issues, whether it be for gas or oil pipelines. With better data and improved maintenance, major accidents can be avoided through the use of drones for pipeline inspections.
3) How can FlytNow help in pipeline inspection using drone-in-a-box systems?
Using FlytNow-powered drones for pipeline inspection, operators can now easily detect any leaks in the pipeline with greater accuracy and efficiency than traditional methods. It allows the team to access difficult-to-reach areas and avoid putting any human in potential danger.
Furthermore, operators can get a real-time video stream of the assets, and also capture high-quality photos and videos of the pipelines and storage tanks. This significantly helps in conducting accurate inspections and detecting potential leaks or damage.
4) What can we expect in upcoming technologies in oil and gas pipeline inspection?
New technologies will include autonomous drones that are packed with a cost-effective platform that will help in inspecting pipelines, provide insight for maintenance activities, and identify human errors. Moreover, they will be equipped with a visual or infrared camera that can detect leaks or damage on its own and inform the team immediately.
5) What are some of the best drones for pipeline inspections in the oil and gas industry?
There are several drones that are well-suited for use in pipeline inspections in the oil and gas industry. Some options include:
- DJI Phantom 4 RTK: This drone has a high-resolution camera and RTK GPS for precise mapping and surveying capabilities.
- DJI Mavic 2 Enterprise Dual: This drone has a compact design and can fly in challenging weather conditions. It also has a dual thermal and visible light camera for identifying issues in pipelines.
- senseFly eBee X: This drone has a long flight time and can fly in autonomous missions to cover large areas quickly. It also has a high-resolution camera for detailed inspection.
- Parrot Anafi USA: This drone has a 4K HDR camera and is capable of flying in challenging environments. It is also lightweight and easy to transport.