bvlos (9)
How can BVLOS drone operations be conducted in Europe, especially using a drone docking station? When it comes to flying drones in Europe, understanding the regulations and its entire architecture is important. The European Union Aviation Safety Agency (EASA) oversees the regulations across 27 European Union Countries and 4 others including Iceland, Liechtenstein, Norway, and Switzerland to ensure safe and standardized drone operations.
Recently, we conducted a webinar featuring Matteo Natale, Technical Standards Manager at DJI, focusing on breaking down EU drone regulations, right from the fundamentals to dock operations, while shedding light on the key components that drone operators need to understand.
The EU Regulatory Framework
There are two main regulations that guide drone operations in Europe: Delegated Regulation 945 and Implementing Regulation 947.
Delegated Regulation (EU) 945/2019:
Delegated Regulation 945 outlines specifications for the design and manufacturing processes of Uncrewed Aircraft Systems (UAS). It sets requirements to ensure the safety, reliability, and compliance of UAS products within the European Union.
Implementing Regulation (EU) 947/2019:
Implementing Regulation 947 establishes rules and procedures governing the operation of Uncrewed Aircraft Systems (UAS) and personnel such as remote pilots within the EU states. It defines the operational requirements to ensure safe and standardized drone activities across member states.
Classification of drone operations
The European airspace categorizes aerial operations into three main types. The regulation in Europe follows the concept of proportionality. These categories are tailored based on the level of risk associated with different drone operations. This regulatory framework applies to both, commercial and non-commercial operations.
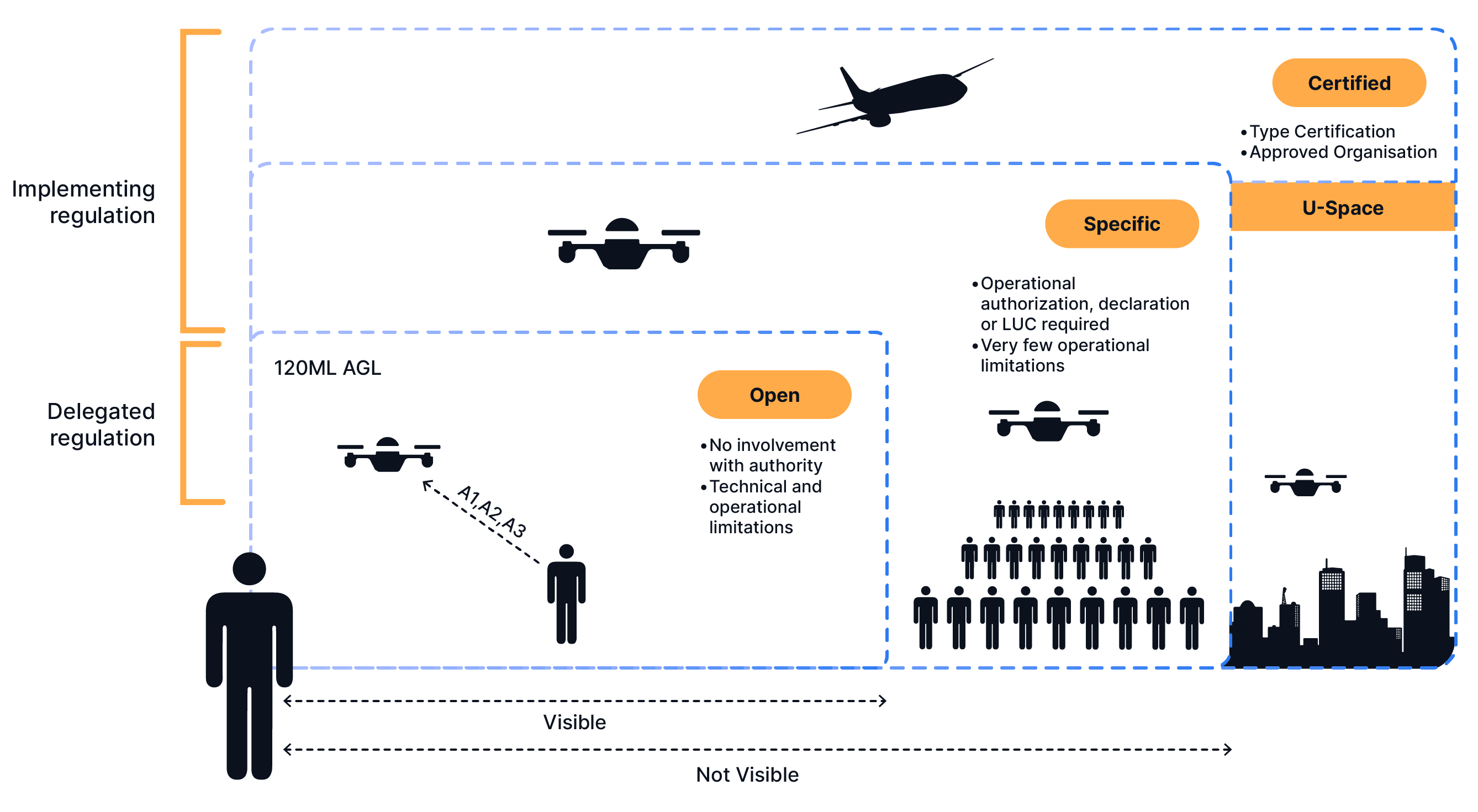
Open category
The Open category pertains to low-risk aerial operations with minimal involvement from authorities. However, there are several technical restrictions and flight limitations to consider. Operators simply need to register their drones, check state insurance requirements, and fly within the operational limits set by the subcategory. The manufacturer, who needs to provide drones with a class identification label, handles any technical restrictions. However, these operations are limited to Visual Line of Sight (VLOS) only and cannot be used for Beyond Visual Line of Sight (BVLOS) flights.
In this category, the drones are restricted to a maximum altitude of 120 meters above ground level and can weigh no more than 25 kilograms. The Open category is further divided into subcategories A1, A2, and A3.-- which may be summarized as follows:
A1: fly over people but not over assemblies of people
A2: fly close to people
A3: fly far from people
.png)
Specific category
The Specific category involves a higher level of involvement from authorities. Unlike the Open category, drones in the Specific category can fly Beyond Visual Line of Sight (BVLOS), above 120 meters in altitude, and weigh more than 25 kilograms. Generally, commercial drone operations utilizing docking stations to automate flight operations fall under this category. Operators need to seek operational authorization from the National Aviation Authority (NAA) through the following approvals:
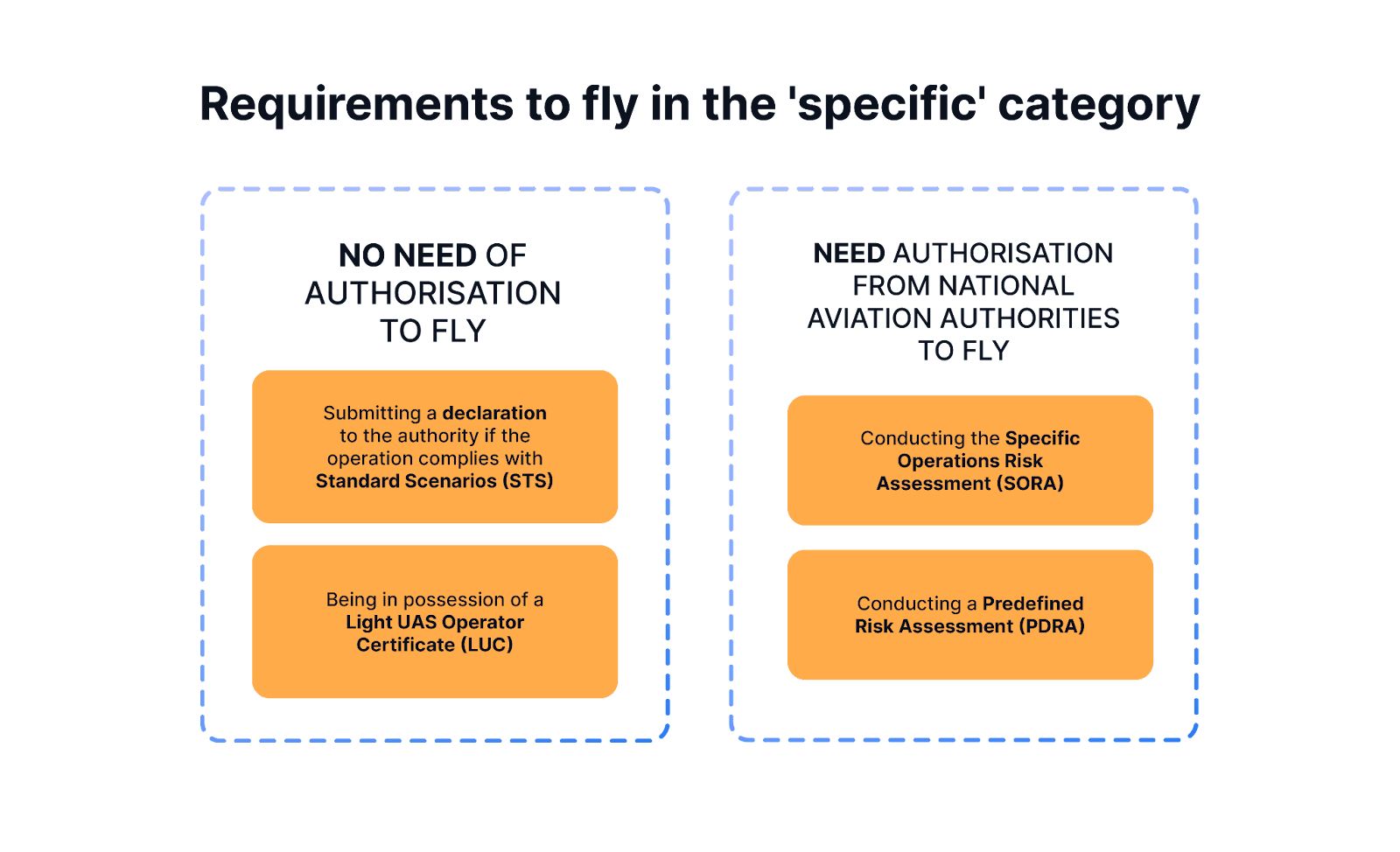
SORA: It is a risk assessment methodology for drone flights in a specific category that aids in classifying risks, identifying mitigations, and setting safety objectives. SORA helps establish operational limitations, training goals, technical requirements, and operational procedures.
PDRA: The Predefined Risk Assessment (PDRA) is an operational scenario for which EASA has already carried out the risk assessment and has been published as an acceptable means of compliance.
STS: STS is a predefined operation described in EU regulations. An operator is not required to obtain operational authorization to conduct an operation covered by a STS. Two STSs have been published so far:
- STS 01 – VLOS over a controlled ground area in a populated environment;
- STS 02 – BVLOS with Airspace Observers over a controlled.
LUC: Light Unmanned Operator Certificate (LUC) is an optional certification that grants privileges, such as starting operations in a specific category without requiring operational authorization. Operators can voluntarily request an assessment from their NAA to evaluate their capability to assess operational risks.
Certified category
The Certified category is designated as high-risk and operates under a regulatory framework akin to crewed aviation. This category applies to operations involving elevated risks such as transporting passengers, carrying dangerous goods, and flying over assemblies of people with drones positioned above three meters.
Understanding Class Identification Label
According to EU regulations, Uncrewed Aircraft Systems (UAS) are classified into seven distinct categories known as Class Identification Labels. The specifications and physical characteristics of the drone are what determine its classification. These labels range from C0 to C6, with drones in the C0 class weighing less than 250 grams and those in the C6 class weighing less than 25 kilograms. They apply to both the open and specific categories.
Following are the technical requirements and limitations for all class-labeled drones:
.png)
These labels provide clarity for drone operators and regulatory authorities alike. They ensure that drones are appropriately matched with the level of risk associated with their operation. By categorizing drones into specific classes, the regulations have been tailored to address the varying levels of risk posed by different types of drones. This approach promotes safety, accountability, and standardization across the drone industry.
The specific category includes class labels C5 and C6. They require the implementation of a geocaging system, enabling remote pilots to establish a virtual perimeter and a programmable boundary for their operations. Additionally, a flight termination system (FTS) must be available for emergencies.
Remote ID requirements
According to EASA, starting from January 1st, operations in the open category require drones with a class label. But, if you have already bought a drone without a label before January 2024, you can still fly it in subcategories A1, A2, and A3, depending upon the weight of the drone. Additionally, from January 1st, 2024, all drones in the specific category and those with class labels 1 and above must have an active remote identification system.
Remote ID allows drones to provide identification and location information while airborne, which can be received through a broadcast signal. This feature is essential for ground safety and security in drone operations. Moreover, Remote IDs help EASA, law enforcement, and regulatory bodies identify whether the drones are operating unsafely or in prohibited areas.
Obtaining operational approvals for the Specific category operations
The Specific category encompasses a wide range of activities, from commercial endeavors to specialized missions that require a higher level of involvement from regulatory authorities. To ensure compliance and safety, operators must undergo a rigorous process of obtaining approvals. By understanding and following these steps, operators can navigate the complexities of the Specific category.
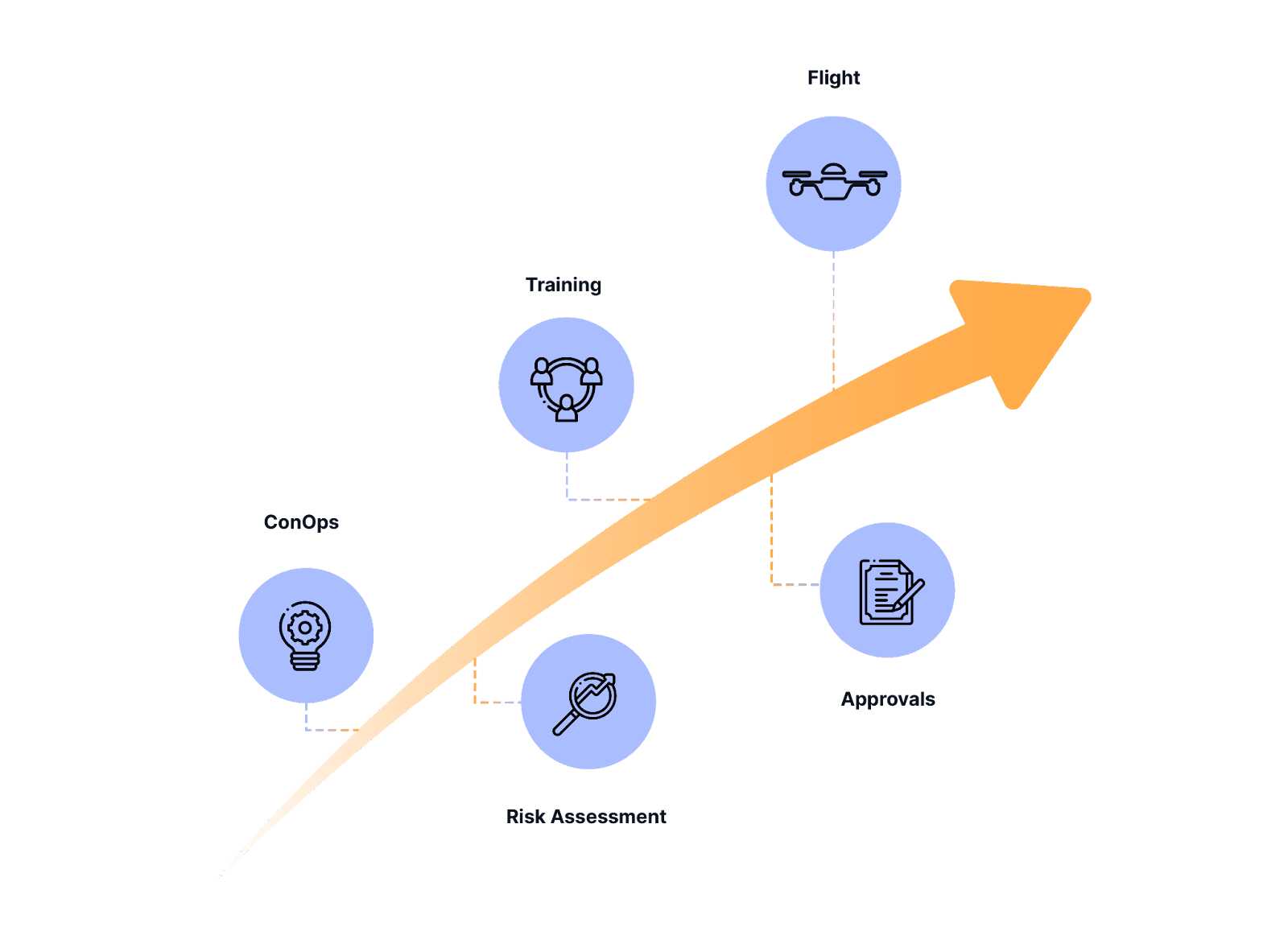
- Concept of Operations (ConOps): In the drone industry, ConOps outlines how drone systems are used in specific operational environments. It details the roles of drones, user responsibilities, various flight and mission scenarios, as well as maintenance and support protocols, guiding stakeholders through the development, implementation, and usage stages.
- Risk Assessment: This assessment helps evaluate potential hazards and assesses the level of risk associated with the proposed drone operation. These assessments could be in the form of Specific Operations Risk Assessment (SORA), Predefined Risk Assessment (PDRA), Standard Scenario (STS), or Light UAS Operator Certificate (LUC), as mentioned above.
- Training: Operators should undergo specific training to demonstrate proficiency in operating drones within the Specific category. These training sessions could cover topics such as flight planning, emergency response, and compliance with regulations. Training ensures that operators have the necessary skills and knowledge to conduct operations safely and effectively.
- Approvals: The national aviation authorities evaluate the proposed ConOps and if all the requirements regarding mitigating potential risks are met, they grant approval for the operation to proceed.
- Flight: Once the approvals are completed one can conduct the drone operations.
Understanding the Specific Operations Risk Assessment (SORA) in detail
According to EASA “SORA is a methodology for the classification of the risk posed by a drone flight in the specific category of operations and for the identification of mitigations and of the safety objectives.” The following 10 steps explain the process of obtaining the SORA approval.
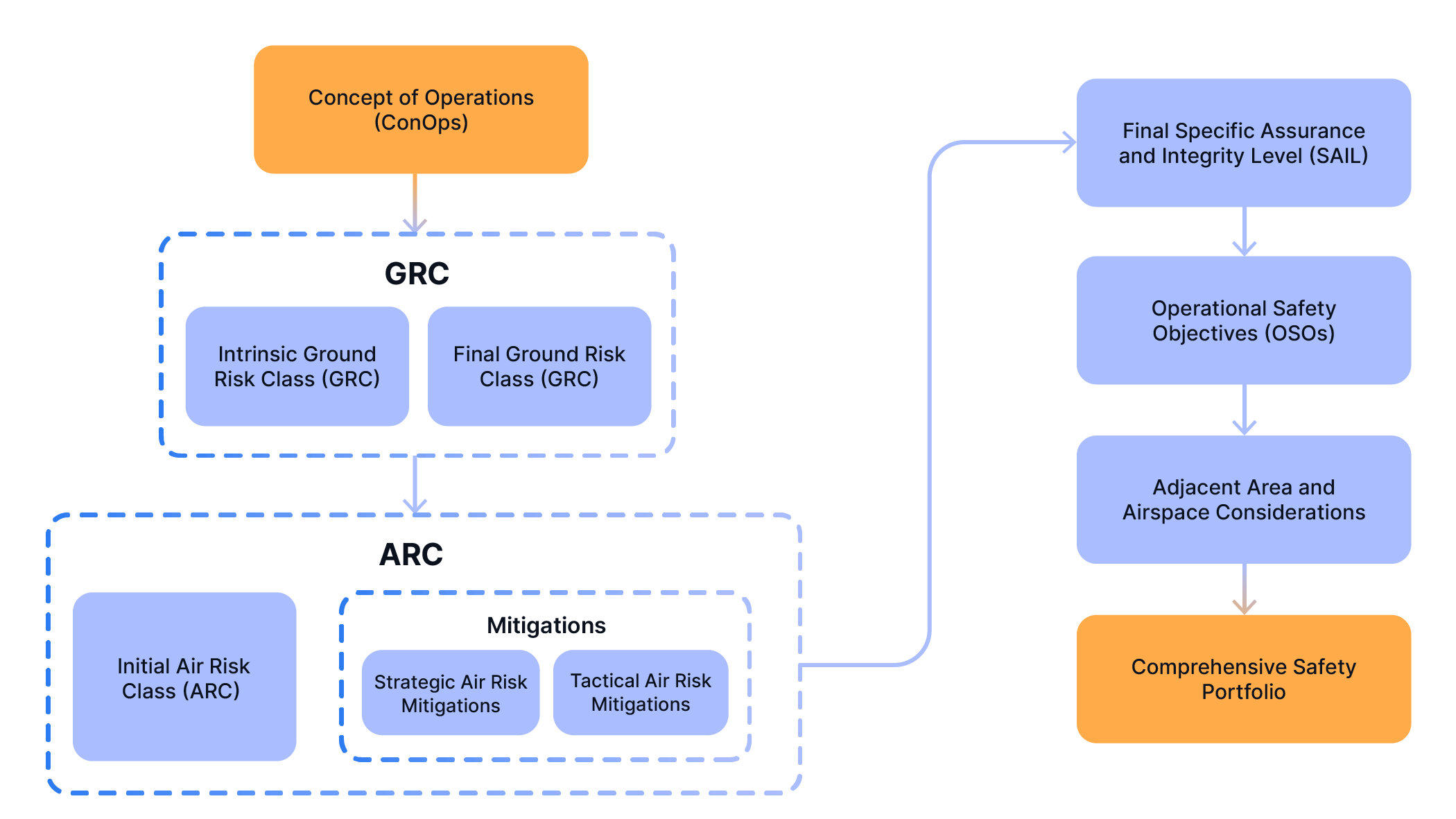
1. Concept of Operations (ConOps): Presenting an organization's system and operations to relevant authorities for approval.
2. Intrinsic Ground Risk Class (GRC): Determining inherent ground risk based on factors like the presence of people or buildings.
3. Final Ground Risk Class (GRC): Assessing ground risk after implementing mitigations to address potential hazards.
4. Initial Air Risk Class (ARC): Evaluating air risk factors before each operation, such as airspace congestion or weather conditions.
5. Strategic Air Risk Mitigations: Applying pre-flight measures to mitigate air risk, like ensuring drones are weather-resistant.
6. Tactical Air Risk Mitigations: Implementing in-flight measures, such as automatic hover or return-home programming.
7. Final Specific Assurance and Integrity Level (SAIL): Determining the overall safety level by combining ground and air risk assessments.
8. Operational Safety Objectives (OSOs): Identifying specific safety objectives based on the organization's SAIL.
9. Adjacent Area and Airspace Considerations: Developing strategies to mitigate risks of encroachment on nearby airspace or ground areas during operations.
10. Comprehensive Safety Portfolio: Compiling all assessment results into detailed safety documentation.
SORA categorizes the risk of an operation into six levels, denoted as SAIL levels, ranging from I to VI. This classification is derived from a comprehensive evaluation that combines both Ground Risk and Air Risk factors. Each SAIL level corresponds to specific requirements that operators must adhere to, meticulously tailored to mitigate the identified risks inherent to the operation. By employing SORA, operators can effectively evaluate and manage the risk landscape associated with their drone operations, ensuring safety and regulatory compliance across the board.
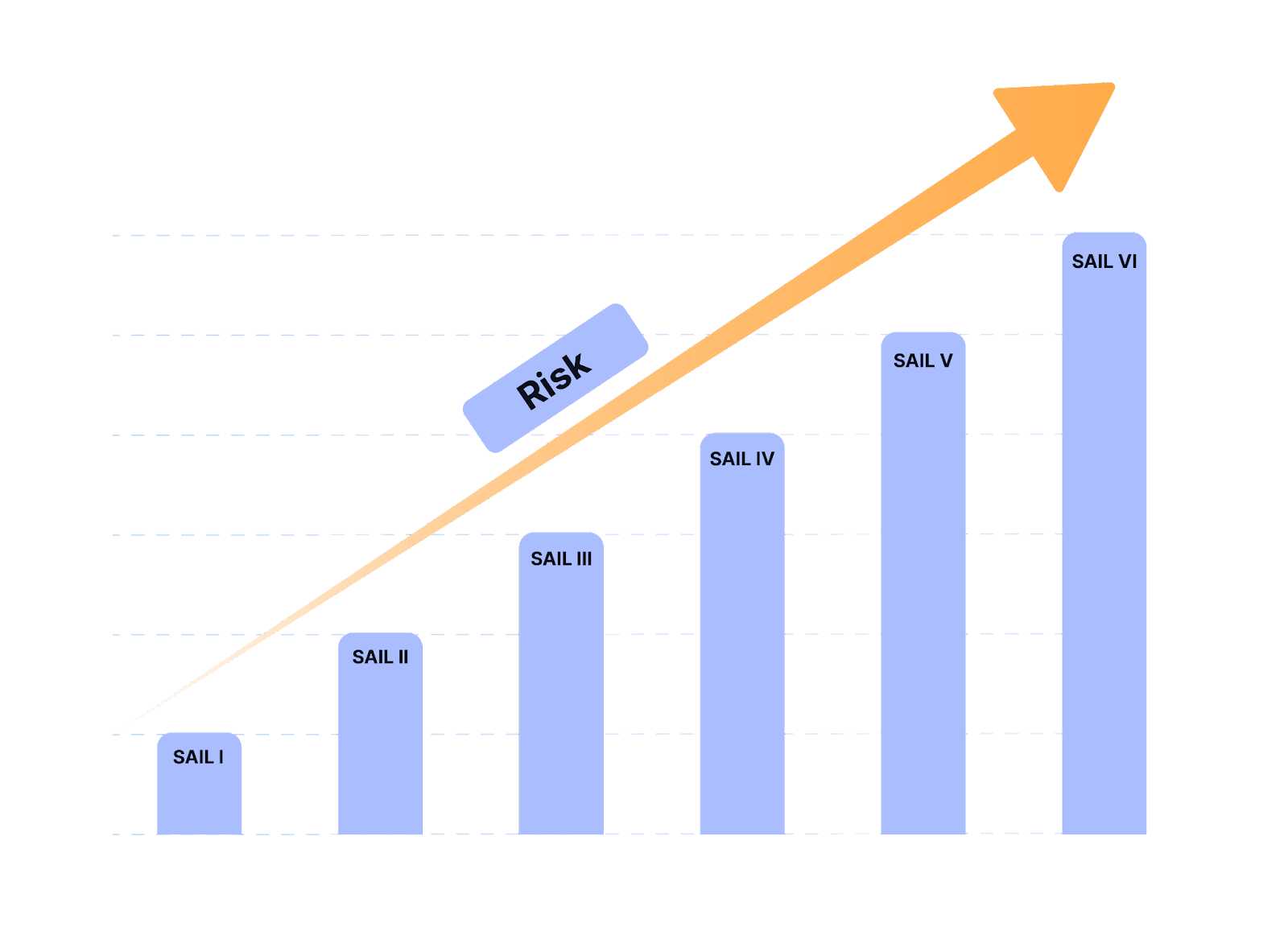
SAIL II operations with DJI Dock and FlytBase
DJI Dock operations can be conducted for SAIL II levels, for which it is essential to achieve a Ground Risk level of 3. It depends on factors like drone and dock size, as well as population density. Currently, the Matrice 30, coupled with the DJI Dock can be easily flown Beyond Visual Line of Sight over a sparsely populated area, while the smaller drone Matrice 3D coupled with the recently released, Dock 2 can potentially fly over a populated area.
However, Ground Risk mitigation, such as parachutes should be integrated to lower the Ground Risk down to a level of 3. Additionally, a Flight Termination System (FTS) is a crucial element to be considered, which might be required to operate the drones close to adjacent areas with a particularly higher level of risk.
EASA's SAIL III compliance, issued on December 18, 2023, provides comprehensive guidance regarding Flight Termination Systems (FTS) in drone operations. It says that drones must be protected from human errors, particularly in situations leading to a loss of control. These situations encompass various scenarios such as crashes with ground, infrastructure, or people.
The compliance emphasizes preventing pilots from selecting parameters that could directly result in a loss of control, including actions such as selecting non-active communication links, deactivating safety functions necessary for operation, and activating flight termination systems during normal operations.
The compliance emphasizes preventing pilots from selecting parameters that could directly result in a loss of control, including actions such as selecting non-active communication links, deactivating safety functions necessary for operation, and activating flight termination systems during normal operations.
FlytBase offers an enterprise-grade drone autonomy platform for streamlined aerial data collection enabling automated BVLOS flights using docking stations. Users can establish custom Geofences and manage No Fly Zones (NFZs) to ensure safety and compliance with regulations. The platform integrates advanced technologies like Detect and Avoid (DAA) systems and ADS-B for airspace awareness, alongside onboard connectivity options and parachute recovery systems. Also, one can access detailed flight logs with automatic PDF reports for safety demonstration and regulatory compliance.
Conclusion and way ahead
In conclusion, the EU drone regulations provide a comprehensive framework to ensure the safe and responsible use of uncrewed aircraft systems. From the Open to the Specific category, each level is tailored to the associated risk, fostering innovation while prioritizing safety.
Looking ahead, recent updates from EASA bring promising changes. SAIL 3 operations, previously requiring a design verification report, now become more accessible. Manufacturers can declare compliance through means of compliance (MoCs), providing a pathway to broader Beyond Visual Line of Sight (BVLOS) operations without the need for extensive verification processes.
In the modern drone ecosystem, BVLOS (Beyond Visual Line of Sight) operations represent the next frontier of possibilities. These operations allow drones to travel distances beyond the operator's direct vision, unlocking potential in industries like agriculture, logistics, surveillance, and more. However, automating BVLOS operations requires not just advanced drones but also sophisticated management platforms. This is where FlytBase and DJI's FlightHub 2 come into play, especially with their compatibility with the DJI dock.
The DJI dock integration is a game-changer, enabling automated drone charging, data transfer, and mission planning. With both FlytBase and FlightHub 2 offering compatibility with this dock, enterprises are presented with a pivotal decision: Which platform will best optimize their BVLOS operations?
This article aims to demystify this choice. We'll delve deep into both platforms, comparing their features, and drawing insights from genuine user feedback, all with a focus on maximizing the benefits of DJI dock integration.
FlytBase: Product Overview
FlytBase emerged as a leading enterprise drone autonomy software, tailored to automate and optimize drone operations. Its compatibility with the DJI dock underscores its commitment to facilitating seamless BVLOS operations.
FlytBase: Key Features
- BVLOS-Ready Operations: With regulatory approvals in its arsenal, FlytBase ensures enterprises can confidently undertake extended drone operations.
- Open Integration: A flexible platform, FlytBase supports robust API and third-party app integrations, catering to diverse enterprise needs.
- Data Security: GDPR compliance and ISO 27001 certification ensure that data integrity and security are paramount.
- Operational Excellence: From live HD/thermal feeds to ERP and VMS integrations, FlytBase offers a comprehensive suite for varied enterprise needs.
- DJI Dock Compatibility: Seamless integration with DJI dock facilitates automated charging, data transfer, and mission planning, enhancing operational efficiency.
FlytBase: User Review
FlytBase: Pricing Plans
For detailed pricing information reach out here: https://www.flytbase.com/contact
FlightHub 2: Product Overview
DJI's FlightHub 2 is not just another drone management solution. It's a comprehensive cloud-based platform designed to provide real-time insights for drone missions. Its compatibility with the DJI dock makes it a formidable choice for enterprises aiming for streamlined BVLOS operations.
FlightHub 2: Key Features
- Real-time Situational Awareness: Features like 2.5D Base Map and One-Tap Panorama Sync ensure enterprises always have a bird's-eye view of their operations.
- Cloud Power: With Cloud Mapping and Unified Management, FlightHub 2 leverages the cloud's prowess for enhanced operational insights.
- Data Security: Hosted on AWS and compliant with ISO/IEC 27001, FlightHub 2 ensures data remains protected and secure.
- Operational Suite: From Mission Live Streaming to Ground-to-Cloud Synergy, FlightHub 2 offers a range of features to optimize drone operations.
- DJI Dock Integration: FlightHub 2's seamless integration with DJI dock ensures automated drone operations, from charging to mission execution, are a breeze.
Flighthub 2: Pricing Plans
FlytBase vs FlightHub 2: Key Differentiators
Let's delve into the primary areas where FlytBase and FlightHub 2 diverge.
BVLOS Operations and Integration:
- FlytBase: Puts a strong emphasis on its BVLOS-ready capabilities, highlighting its regulatory approvals. Its open platform approach with APIs and third-party app integration capabilities makes it stand out for enterprises looking for flexibility.
- FlightHub 2: While it also supports BVLOS operations, its strength lies in providing comprehensive real-time situational awareness. The platform doesn't emphasize third-party integrations as much but offers a rich set of built-in features.
User Experience and Interface:
- FlytBase: Offers a streamlined interface tailored for ease of use, making it intuitive for users to navigate and manage drone operations.
- FlightHub 2: Provides a more detailed dashboard, focusing on in-depth insights and comprehensive drone mission management. This might come across as more complex for some users, especially those new to drone operations.
Data Security and Compliance:
- FlytBase: Prioritizes data security with multiple layers of protection, including GDPR compliance and ISO 27001 certification, ensuring data integrity and security.
- FlightHub 2: While it also emphasizes data security, its hosting on Amazon Web Services with ISO/IEC 27001 security certifications is its unique selling point.
Operational Features and DJI Dock Compatibility:
- FlytBase: Apart from its core features like live HD/thermal drone feeds, its compatibility with DJI dock ensures seamless integration for automated BVLOS operations.
- FlightHub 2: While it also integrates seamlessly with DJI dock, it offers additional features like 2.5D Base Map and Cloud Mapping, enhancing the operational experience.
By understanding these key differentiators, enterprises can make an informed decision based on their specific needs and operational priorities.
Conclusion - FlytBase vs FlightHub 2
Every decision in the realm of drone operations should be rooted in your enterprise's specific requirements and objectives. It's crucial to align your choice with your operational needs and future goals.
FlytBase distinctly shines with its BVLOS-ready capabilities and its open integration approach. Its emphasis on regulatory approvals and flexibility in third-party integrations makes it a top choice for enterprises that value adaptability and a hands-on approach to drone operations. Moreover, its robust data security measures ensure that enterprises can operate with peace of mind.
FlightHub 2, on the other hand, excels in providing real-time situational awareness and a comprehensive suite of built-in features. It's tailored for those who prioritize in-depth insights and a holistic view of their drone missions.
While both platforms offer commendable features and DJI dock compatibility, FlytBase might have a slight edge for those who prioritize flexibility and BVLOS operations. However, if you're looking to explore further, there might be other platforms in the market that cater to niche drone operational needs.
In the rapidly evolving landscape of drone operations, one of the most significant challenges is navigating beyond the line of sight (BVLOS). Operating BVLOS opens up endless possibilities for industries, but it also brings a host of crucial considerations to the forefront. Flight safety and risk mitigation take utmost importance among these considerations, as the safety of people, property, and the uncrewed aircraft itself is paramount.
Currently, most BVLOS operations require the presence of a vigilant visual observer (VO) who diligently scans the skies for potential obstacles and hazards. If they come across one, they must immediately notify the remote pilot in command to abort the drone's current mission. Therefore, it goes without saying how dangerous any form of communication lapse can be.
The Role of Visual Observers in BVLOS Flights
Before delving into the specifics of the various types and Detect and Avoid (DAA) technologies available, we must first understand the role of visual observers and why they are required. For example, the Federal Aviation Administration (FAA) in the United States specifies the operational requirements that must be met before flying unmanned aircraft systems. There is a requirement for a visual observer to perform the following roles for all drone operations that do not have a Part 107.33 waiver.
However, this human-centric approach can be both resource-intensive and limited in terms of continuous monitoring. There could be objects in the area of the drone operation, such as a small non-cooperative paraglider with no engine noise. It may be difficult for a human to accurately identify that and notify the remote pilot-in-command (PIC).
The Solution: AI-powered Detect & Avoid Technology
Detect and avoid (DAA) system enables operators to sense and avoid other aircraft and obstacles autonomously. These systems use sensors, such as radar, acoustic, and visual, to detect and avoid obstacles in the airspace. With DAA technology, drones can operate safely beyond visual line of sight, expanding their range of capabilities and applications.
Types of DAA Systems
There are several types of DAA systems, including radar, acoustic, and optical systems. Each of these systems has its own set of pros and cons, and the choice of system depends on the specific requirements of the drone operation.
Casia G: Iris Automation’s Ground-Based Detect and Alert System
Based on optical vision, Casia G is a ground-based surveillance system from Iris Automation to continuously monitor airspace and ensure UAS operations are safe from intruder aircraft. The sensors employ Iris' patented AI and computer vision technology to provide a full optical, 360° field of view for detecting and alerting to any cooperative or non-cooperative aircraft within a 2 km radius of the sensor's location.
Integration with FlytBase for Safe Remote Drone Operations
By integrating with the Casia G system, the FlytBasedashboard provides real-time data on intrusive aircraft, including type, live telemetry, and location on the map. Remote drone operators can monitor the status and radius of the Casia G sensor and receive immediate alerts if unauthorized aircraft are detected within their operating area.
BVLOS Approvals with Detect and Avoid Systems
The FAA has introduced a smart approach by incorporating "shielding" into their waivers, acknowledging that flying within 50 feet of the ground or a structure is likely safer for other aircraft. To achieve true BVLOS flights, the FAA requires some form of detect and avoid system, whether cooperative or non-cooperative, integrated into the operations.
The Way Ahead
While human visual observers remain important, technological solutions offer scalability and significant advantages. These solutions should be seen as tactical mitigation measures complementing other safety protocols. Cameras, sensors, and advanced safety technologies provide higher accuracy, continuous monitoring, and real-time responses, enhancing the safety of drone operations and opening doors to more advanced applications in the future.
Continued innovation and advancement in DAA technology are going to be essential for handling complex situations effectively and mitigating risks and safely integrating drones into the world’s third dimension.
Conclusion
The future of drone navigation is here, and it's called Detect and Avoid (DAA) systems. These systems, powered by AI and advanced sensor technology, are revolutionizing the way drones operate, especially in BVLOS operations. As we continue to innovate and advance in this field, we can expect to see safer, more efficient, and more scalable drone operations in the near future.
Read the Full Article Here: https://www.flytbase.com/blog/detect-and-avoid-technology
Drone technology has undeniably transformed the traditional approach to industrial inspections, making them an essential part of their maintenance procedures. Traditional inspection methods, such as scaling cell towers, wind turbines, or scaffolding to examine industrial boilers, are being phased out in favor of drone inspections. Service providers can easily capture all necessary visual data without compromising inspector safety.
Autonomous drone technology has made this process even more simpler & cost-effective. With the help of drone-in–a-box systems, companies can now perform inspections in hard-to-reach areas without the need for specialized personnel to be on site. By a simple push of a button, energy companies can gather accurate information from remote locations, such as gas facilities, solar farms, and remote oil fields.
In this blog post, we will discuss the benefits of using autonomous drone technology in industrial inspections, using case studies and insights shared at a NestGen'23 session by industry experts Kevin Toderel from RMUS Canada and Grant Hosticka from DJI, North America.
.jpg)
Phased Approach for Autonomous Drone Operations
To ensure regulatory compliance and operational safety, Kevin recommends a phased approach to drone implementation for industrial inspections. The approach involves a step-by-step progression in terms of removing human intervention and increasing automation in drone operations. The framework can be tailored to meet the unique needs of each project and it has proven to be effective, particularly in Canada. The four phases of this approach are as follows:
- Licensed Pilot with a RC and Visual Observer (VO): In the first phase, the drone operation starts with a licensed pilot operating the drone via RC while also acting as a visual observer. This requires no specific licensing and counts as a regular flight. The only difference between this and a regular flight is that the pilot will be operating through the dock, but will essentially be ready to take control with the RC in the event of an emergency.
- Dock and Software with VO having Return-to-Home Functionality: The pilot is removed from the drone operation in the second phase, and the drone is piloted remotely using cloud-based software. However, this operation remains within the visual line of sight since a visual observer (VO) is present on the site with a return-to-home functionality to take control of the drone in case of an emergency.
- Dock and Software with Complete Autonomy within VLOS: In the third phase, the drone operations are completely autonomous and the dock and the drone are remotely controlled from the command center without a licensed pilot or a VO on site. These operations however are conducted within the visual range and will test the ability of the drone to navigate on its own.
- Dock and Software for Fully BVLOS Ops: Drone operations extend beyond the range specified in phase 3 in the final phase, necessitating a waiver from the regulatory authority of the operating geography. These operations require the use of technology such as Detect and Avoid, UTMs, and others.
.png)
Applications of Drones in the Energy Industry
Let's take a closer look at some of the applications in the power generation industry where autonomous drone operations can generate value or make the most sense:
Drones in Solar Farm Inspection
The solar industry is constantly looking for ways to streamline solar panel maintenance and reduce the time required for upkeep. A potential answer to this problem is the use of drones. Autonomous operations can make the process more efficient, allowing for faster and more accurate inspection.
"Maintenance personnel still spend far too much time looking for problems rather than maintaining equipment," Kevin points out, "and this is where autonomy and AI applications will provide the most bang for the buck."
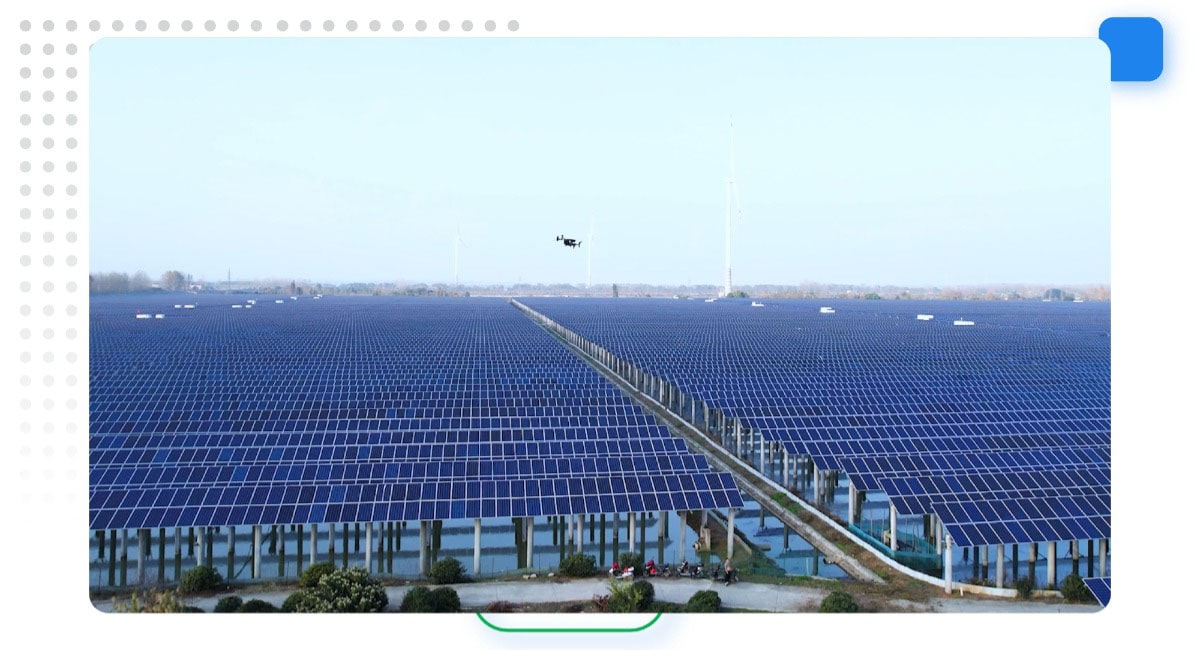
The drones can be programmed to autonomously take off from their docks at a scheduled time, follow specific flight paths, capturing images of the solar panels from different angles. The images are then analyzed using AI algorithms to identify any faults or issues, such as damaged panels or vegetation growth. This information is relayed in real time to maintenance teams, who can then prioritize their efforts accordingly.
Additionally, the same system can be used to track the progress of the solar farm's construction process and conduct security patrols. Designers can identify and correct any issues that may arise during the construction phase. Furthermore, the construction process can be made more transparent by providing regular updates to stakeholders.
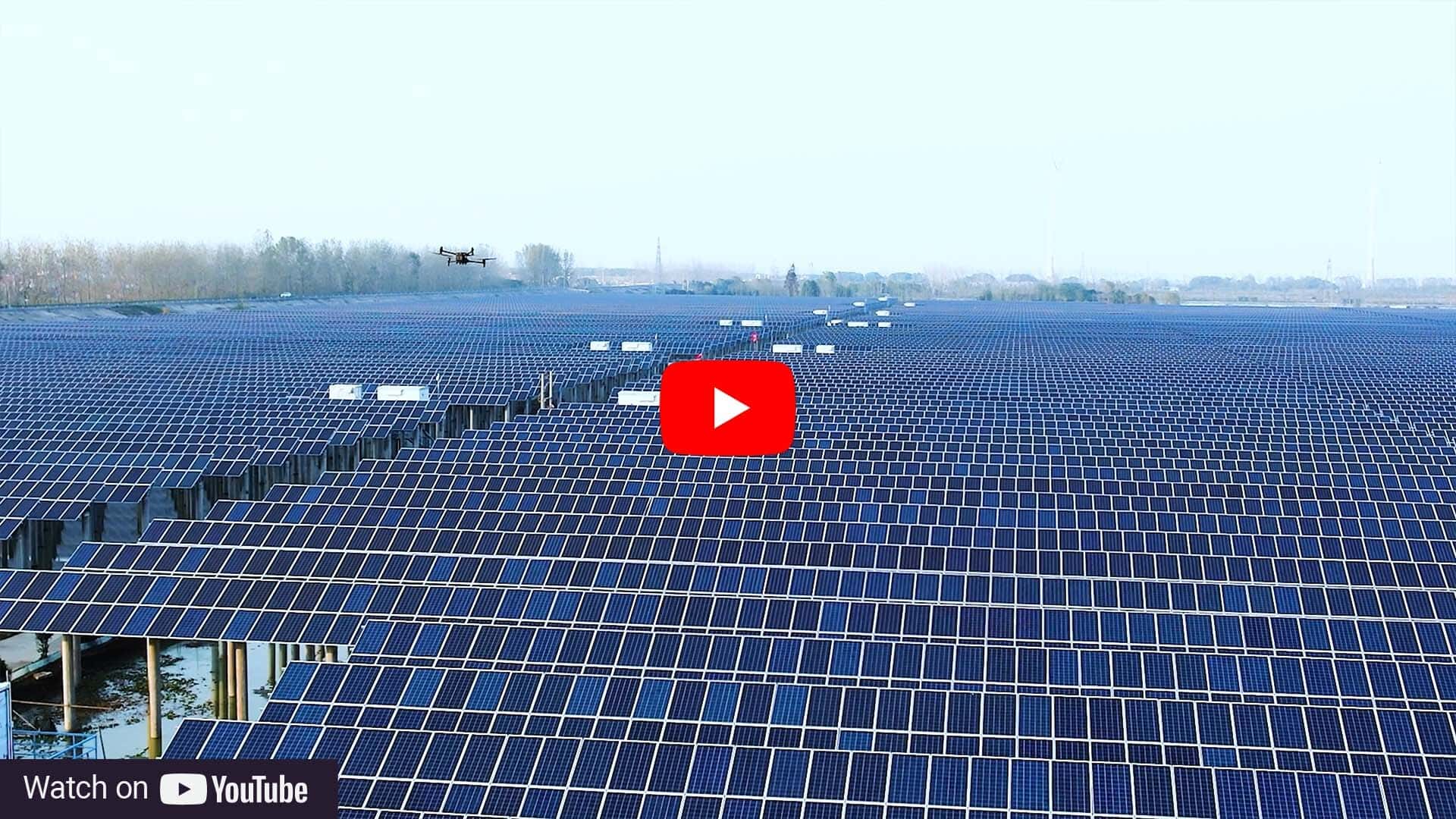
Drones in Wind Turbines
The wind energy industry has long recognized the value of UAVs for blade inspections.
Even if you do not consider fully autonomous blade inspections, there are countless applications for drone technology in wind farms, especially if the drone is ready to be deployed at all times.
One of the most significant advantages of using autonomous drone systems for wind turbine inspections is the ability to perform predictive maintenance and servicing. By regularly inspecting wind turbines, energy companies can detect damages and defects before they become severe, reducing the risk of downtime and increasing the lifespan of the turbine.
Kevin highlights, “Operators often have to suspend maintenance if they suspect there’s ice on the blades. One of the biggest use-case for drone-in-a-box automated operations would be to send drones to check if there is ice on the blades and whether it is safe for the team to go up for inspections.”
Drones for Inspecting Dam Spillways
The use of autonomous drone systems in detecting and responding to dam spillways has been gaining traction in recent years. Energy companies can reduce the risk of personnel injury by monitoring and inspecting the dam spillway from a safe distance.
.png)
Kevin shares an account about how they received a BVLOS waiver to conduct drone operations after a fatality occurred during a flood caused by dam water release. Before releasing the water, autonomous drones can perform a quick inspection of the spillway.
He emphasizes that each use-case has its own set of technical requirements. Considerations like whether the drone is below grade or whether an LTE or RF connection is necessary had to be made in the case of the dam spillways.
Drones for Inspecting Site Security
One of the most common use-case of autonomous drone systems is for site security and the power generation industry is no exception. Kevin mentions a case wherein the asset owner had to unfortunately experience an act of vandalism that caused extensive damage to the infrastructure. The damage caused by the vandalism totaled around four million dollars. If there were to be a drone docking station to monitor this frequently and mitigate this, the ROI from installing it would be immediately achieved.
Kevin was able to easily schedule repetitive perimeter patrol missions with high frequency using DJI Dock, even at temperatures ranging from 0 to 6 degrees. Furthermore, with software solutions such as FlytNow, motion detection sensors or existing security systems to trigger drone deployment based on alarms can be easily integrated. Drone-in-a-box system for site security helps in reducing liability, avoiding repairs, downtime and property loss, making it a critical use case for a wide range of assets.
What Lies Ahead
Implementing autonomous drone operations in industries like power generation could present several challenges such as navigating the complex regulatory frameworks, technical development, and partnerships with third-party providers. Kevin emphasizes that, in order to address regulatory challenges, industry players collaborate with regulatory bodies and use phased approaches to build trust over time.
Technical challenges are addressed through R&D investments and collaborations with third-party providers to integrate complementary technologies. Partnership challenges are addressed by developing integrated solutions through open APIs and software development kits. Through these solutions, the benefits of autonomous drone operations can be realized while ensuring safety and regulatory compliance.
He concludes the session by stating the importance to remember that there is “no one-size-fits-all” solution in the drone industry. Different use cases will require different sensors and aircraft, and there will be a variety of hardware and software options available to meet these needs.
When considering partners for proof of concept projects, it's important to find a partner who can take a holistic approach to the project, considering all aspects of the drone solution from regulatory engagement to data hosting and security. With the right partners and solutions in place, drone-in-a-box systems have the potential to greatly improve efficiency, safety, and security across a wide range of industries.
Pampa Energía, Argentina's largest independent energy company, specializes in the electricity, oil, and gas value chains. Headquartered in Buenos Aires, it engages in intense oil and gas exploration and production activities. It has a presence in 13 production areas and 5 exploration areas in the most significant basins of the nation.
Through its power plants, the company has attained the capacity to generate about 5,000 barrels of oil and 9 million cubic meters of gas per day. In addition, it produces 4,970 MW of electricity through wind, hydroelectric, and thermal power plants. Listed on the Buenos Aires Stock Exchange (BCBA) and the New York Stock Exchange (NYSE), it thrives on the vision of becoming an emblematic company known for its commitment, growth, and operational excellence.
How Pampa Energía Conducted Thermal Power Station Inspection with Drones
In 2017, Pampa Energía integrated drones into their asset inspection operations and have since expanded to a fleet of nine different drones to assist in their large-scale operations. During inspections, they primarily use the Mavic 2 Enterprise Advanced and Matrice 200 series drones for photo imaging and analysis.
These drones enable them to quickly cover large areas and capture tens of thousands of photographs, which are then stitched together into an orthomozaic to create an accurate representation of the plant. Pampa Energía conducts three types of inspections:
1. Periodic
Pampa requires periodic inspections of their pipelines, docks, tanks, chimneys, high-voltage towers, boilers, and electric grids, for example, every week. These inspections are crucial to ensure that assets are functioning correctly, as issues like corrosion or lateral structures near the pipeline often go unnoticed during a manual inspection.
2. Planned
Conducted once a year, these inspections primarily consist of land surveys of electric grids, roads, and terrain and are necessary for new construction and infrastructure development.
3. Triggered
Triggered inspections are only carried out when there is a specific problem that needs to be assessed, such as the surveillance of oilfields and pipelines.

Challenges Faced by Pampa Energía with Manual Drone Inspections
As the demand for energy in Argentina grew, continuous monitoring and preventive maintenance of the Genelba Thermal Power Plant (CTGEBA) became critical to ensure uninterrupted operations. With a total capacity of 1,253 MW, representing 2.9% of the nation's installed capacity, the plant required frequent inspections to maintain safety and efficiency. However, as the plant expanded, manual inspections became increasingly challenging and time-consuming, leading to two major difficulties:
1. Increase in drone inspection rounds
As the Genelba Thermal Power Plant grew in size, it required a large number of manual visual inspection rounds to be carried out to cover the new equipment. This gradually increased the time required to cover the entire power plant for thermal inspection. The available inspectors were no longer able to cover the entire power plant in a single shift, resulting in a significant gap in the inspection timeline.
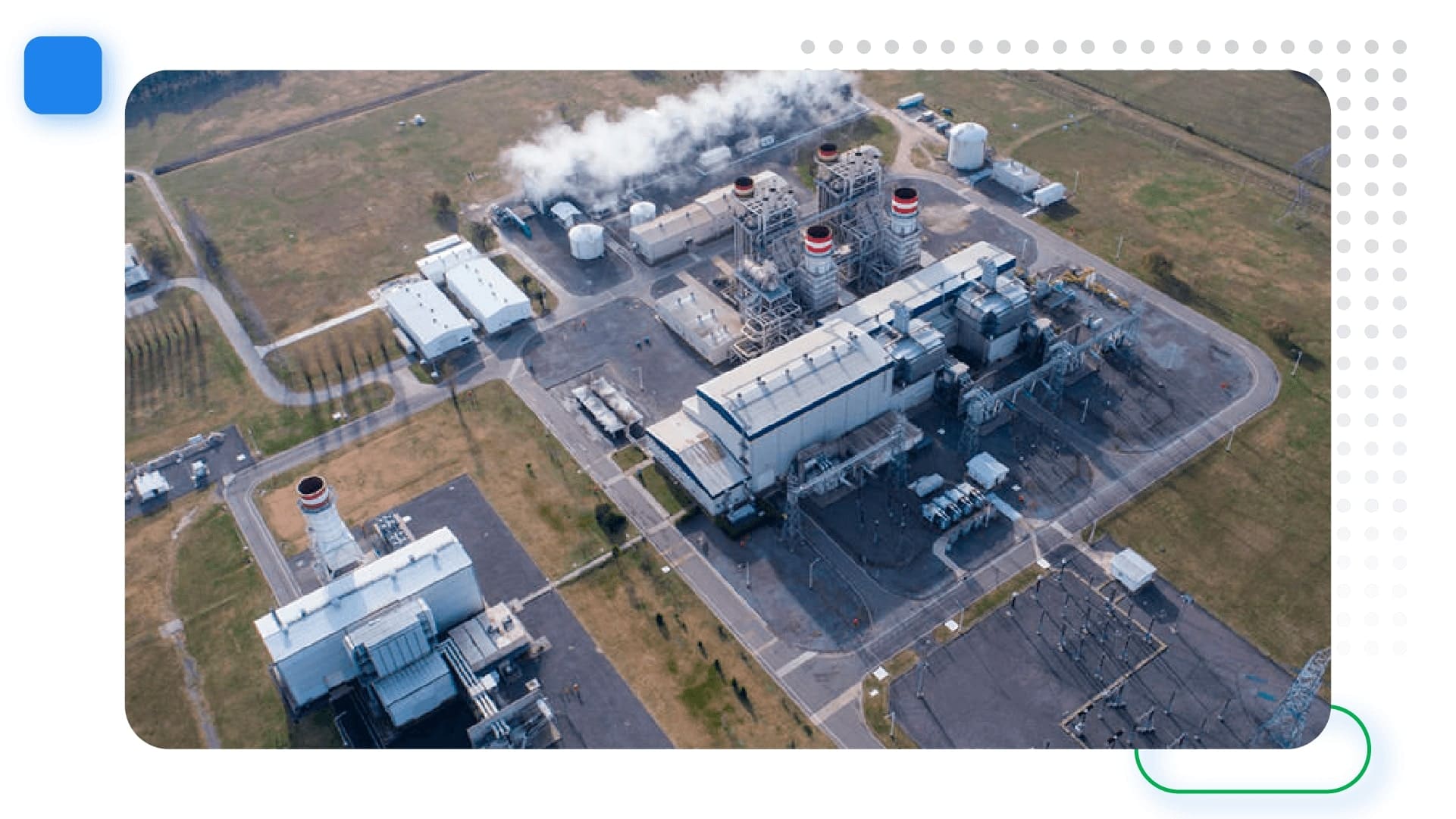
2. Difficulty in conducting perimeter security tours
The site, which is located in the province of Buenos Aires, is more than 970,000 square feet in size, making it one of the country's largest thermal power plants.
Because the team had to constantly set up their base station, replace drone batteries, and transfer data manually after a certain distance, conducting security tours throughout the plant became much more difficult and time-consuming.
Optimizing Inspection of Thermal Power Plants with Drone-in-a-Box Solution
As part of its Digital Transformation strategy, Pampa Energía sought to optimize the inspection routes at the Genelba power plant. Rather than hiring additional employees and drone pilots, they decided to explore the use of autonomous drones to simultaneously carry out maintenance planning, inspections and security operations.
Phased Implementation Process
The deployment has been carried out in several stages, as follows:
- First, a proof of concept test was conducted to evaluate various docking stations, battery recharge technologies, and control software.
- The selected technologies were then purchased, and a highly thorough series of tests were run to ensure that the equipment's functionality and how it interacted with one another were both verified.
- A determined and tested set of paths were determined for the drone.
Additionally, the present and upcoming team members also received training on how to use this technology to carry out drone missions.
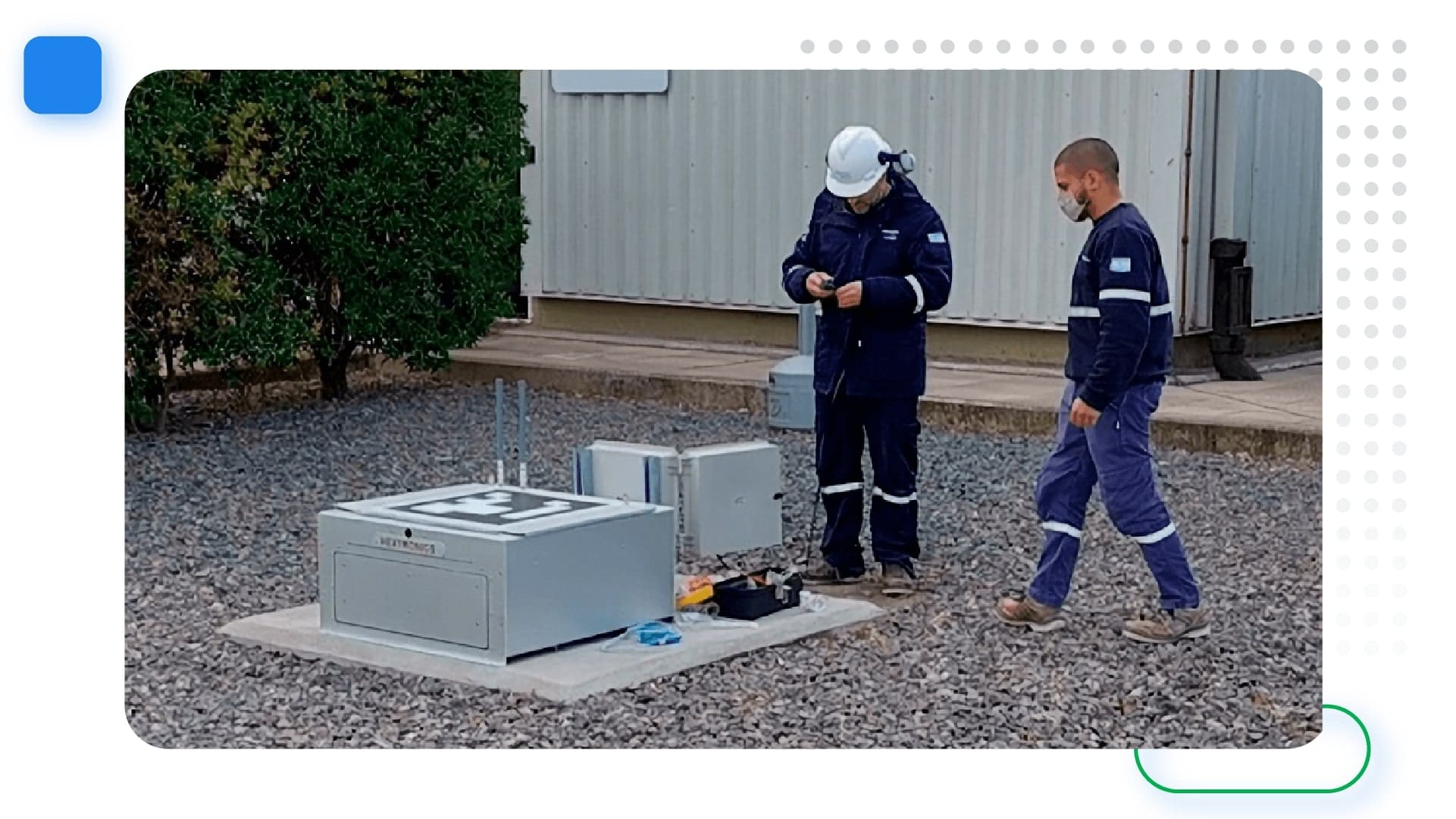
The biggest benefit that drone-in-a-box systems provided was the dual functionality. The team at Pampa intended to deploy these systems across their power plants for inspection as well as security. The inspection team could use the docking station to do monitoring and maintenance of the plants during the daytime and in the nighttime they use the same devices for security.
Why Pampa Energía Chose FlytNow as their DiaB Operations Software
As Marcelo Lopez, Pampa Energía's Project Manager, pointed out “We wanted to optimize inspection routes at the Genelba power plant since the area was too large for inspectors to cover in a single shift. We decided to employ the FlytNow-powered autonomous drone-in-a-box solution due to its superior unattended flight technology and affordable price. The FlytNow customer success team has been dedicated to resolving customer issues. They are aware of industry developments, are attentive to their customer's needs, and capable of handling challenges.”
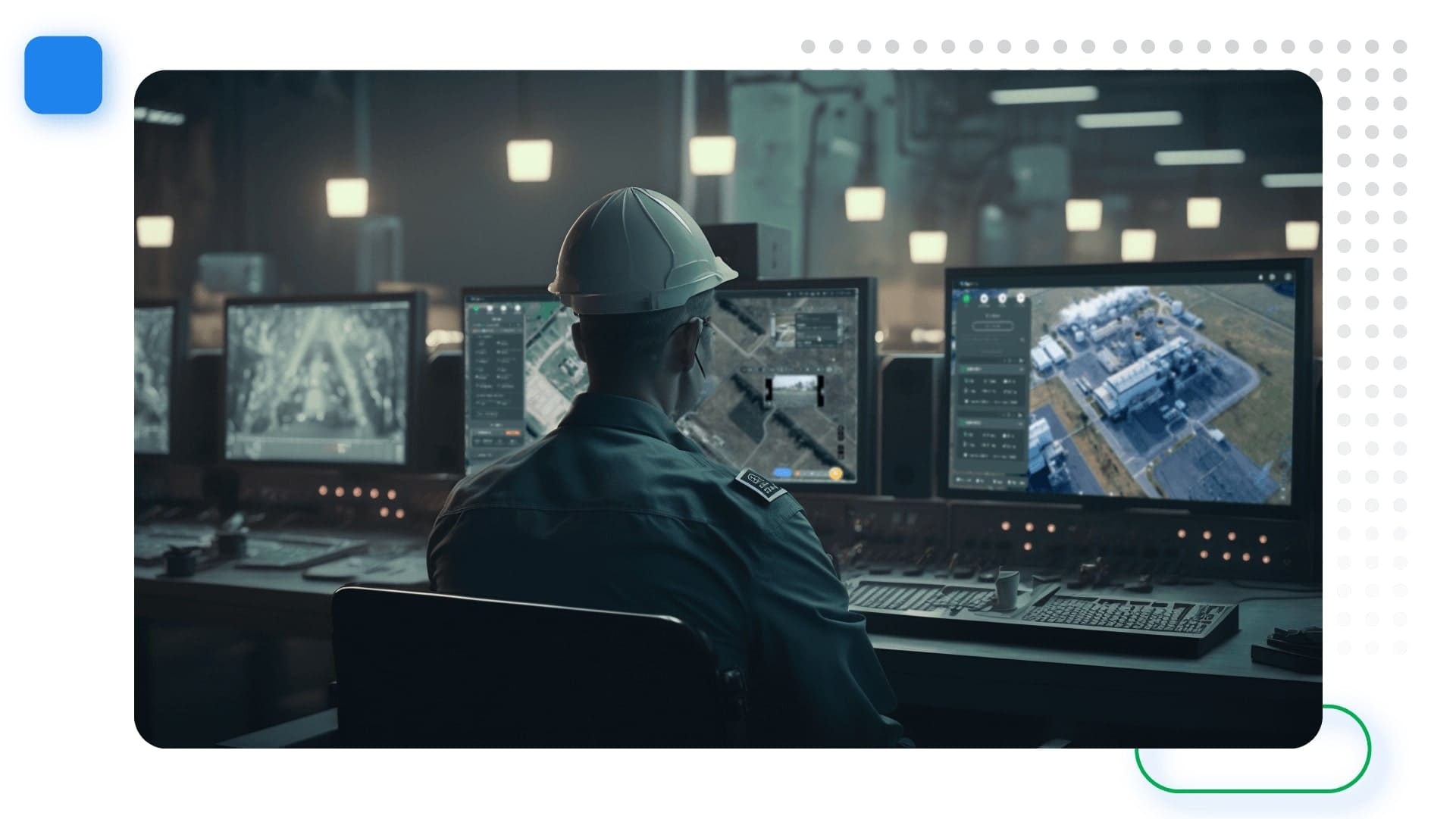
Here’s how they benefited from autonomous drone-in-a-box systems powered by FlytNow:
1. Improvement in inspection rounds:
FlytNow enabled Pampa Energía's operations team and inspectors to schedule and execute repeatable drone missions along pre-established routes, stopping at specific points of interest to view assets remotely.
The remote control of the drone's camera payload allowed for efficient zooming to detect faults or abnormalities in the power plants. Compared to manual inspections, FlytNow resulted in faster and more efficient rounds, significantly reducing the time and effort required to inspect large areas like the Genelba plant.
Here’s how an inspection routine looked like:
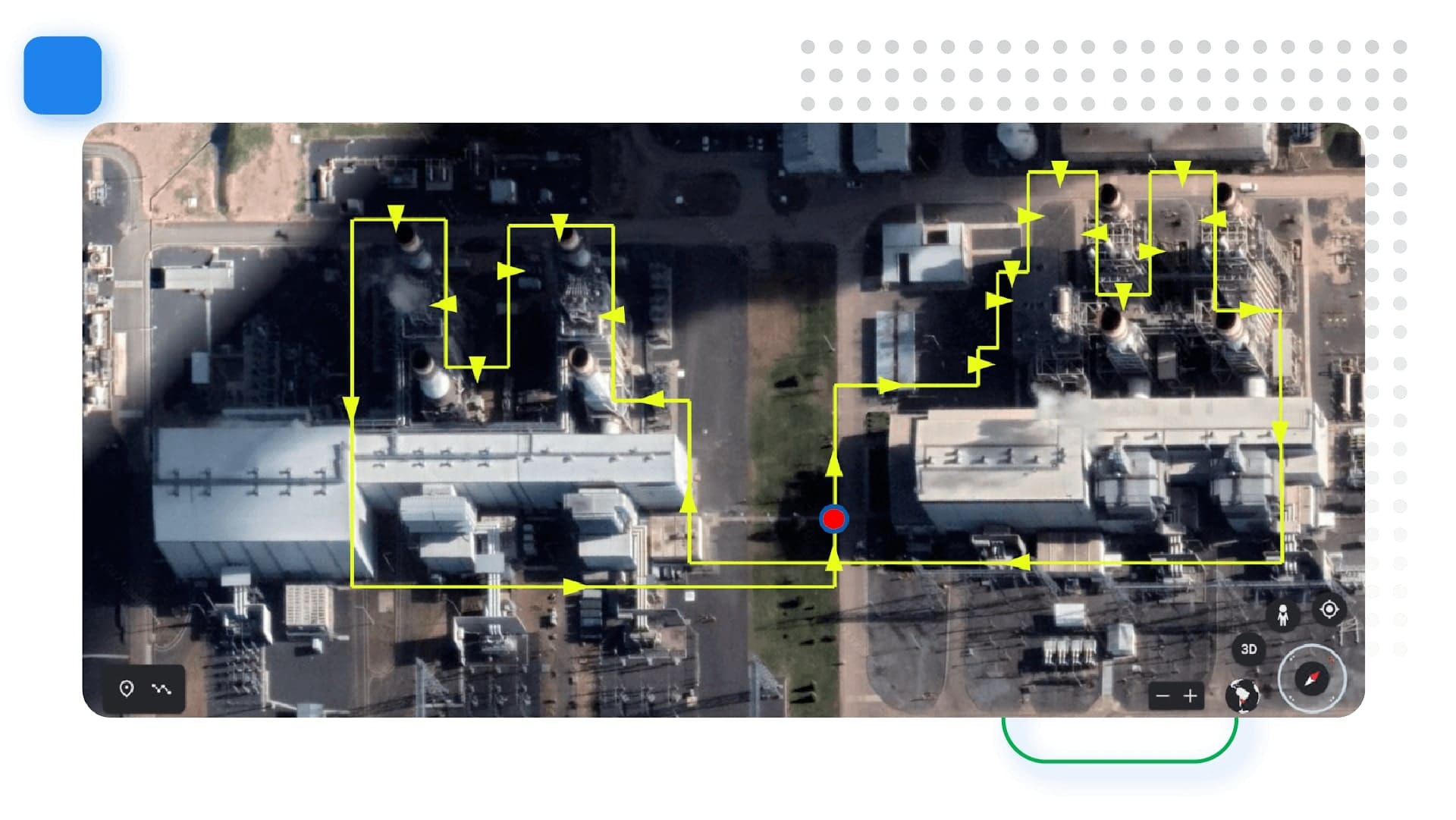
Furthermore, the team utilized drone docking stations to perform security patrols at regular intervals, effectively monitoring the premises for any potential intrusions. By deploying drones to the site prior to security personnel, the team was able to proactively prepare for incidents, while simultaneously saving time and resources in terms of fuel and personnel typically required for routine patrols. The image below depicts a typical security patrol mission:
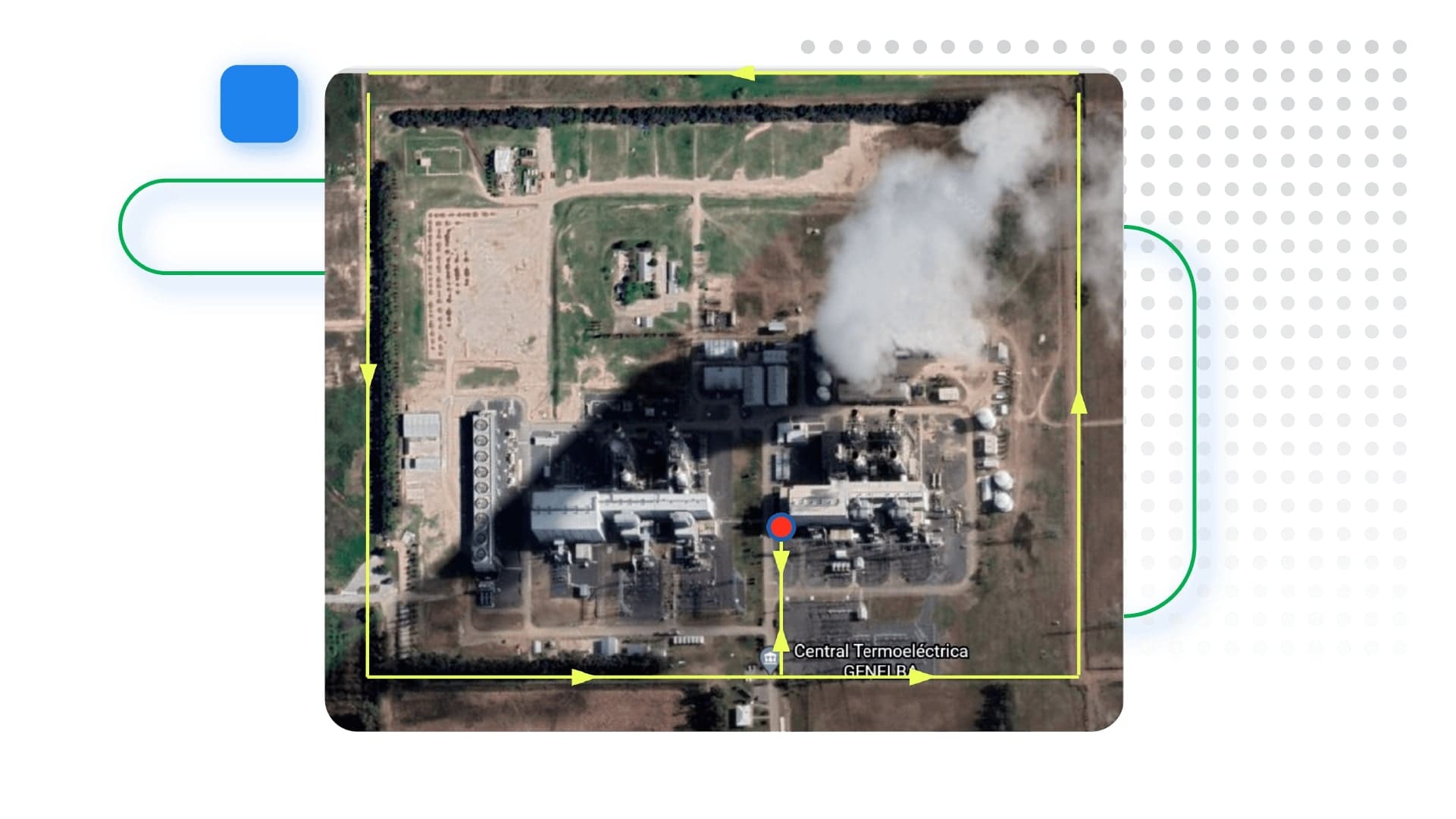
2. Reduction in accidents:
Given that, in a thermal power station the potential for devastating mishaps due to high pressures and temperatures is very high, it is crucial to ensure the safety of workers while maintaining the smooth operation of the plant. With the ability to send drones autonomously at a click of a button, the team can now access hard-to-reach or dangerous areas with ease, without having to send the local team in harm’s way.
By remotely monitoring the plant's critical infrastructure and systems, the team can quickly identify and address any issues before they escalate into major accidents, thereby reducing the risks associated with human error.
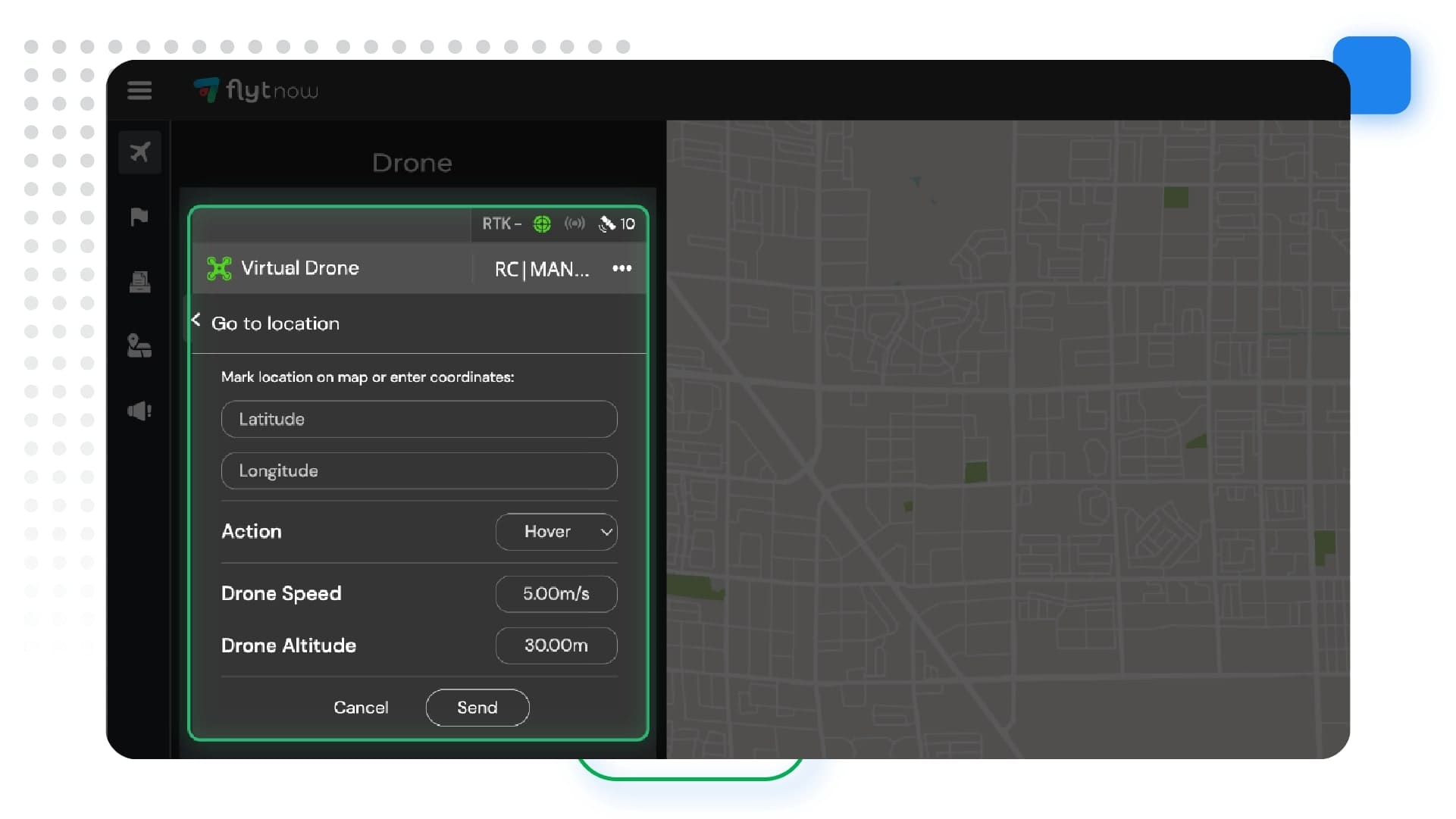
Additionally, FlytNow with a host of security features enabled the safety of the drone & the dock as well. With features such as:
- Failsafes: FlytNow is equipped with various failsafe mechanisms that provide assistance in case of emergencies. For instance, in the event of a lost RC link or internet connectivity, the drone can either pause until the connection is restored or perform a controlled emergency landing at a predetermined safe location in case of low battery alerts. These failsafe mechanisms and timeout settings can be easily customized and configured by the team to ensure optimal safety during drone operations.
- Geofence: The operators also have the ability to create virtual fences around the area of their operation and prevent the drone from entering restricted zones by taking specific actions if the fence is breached.
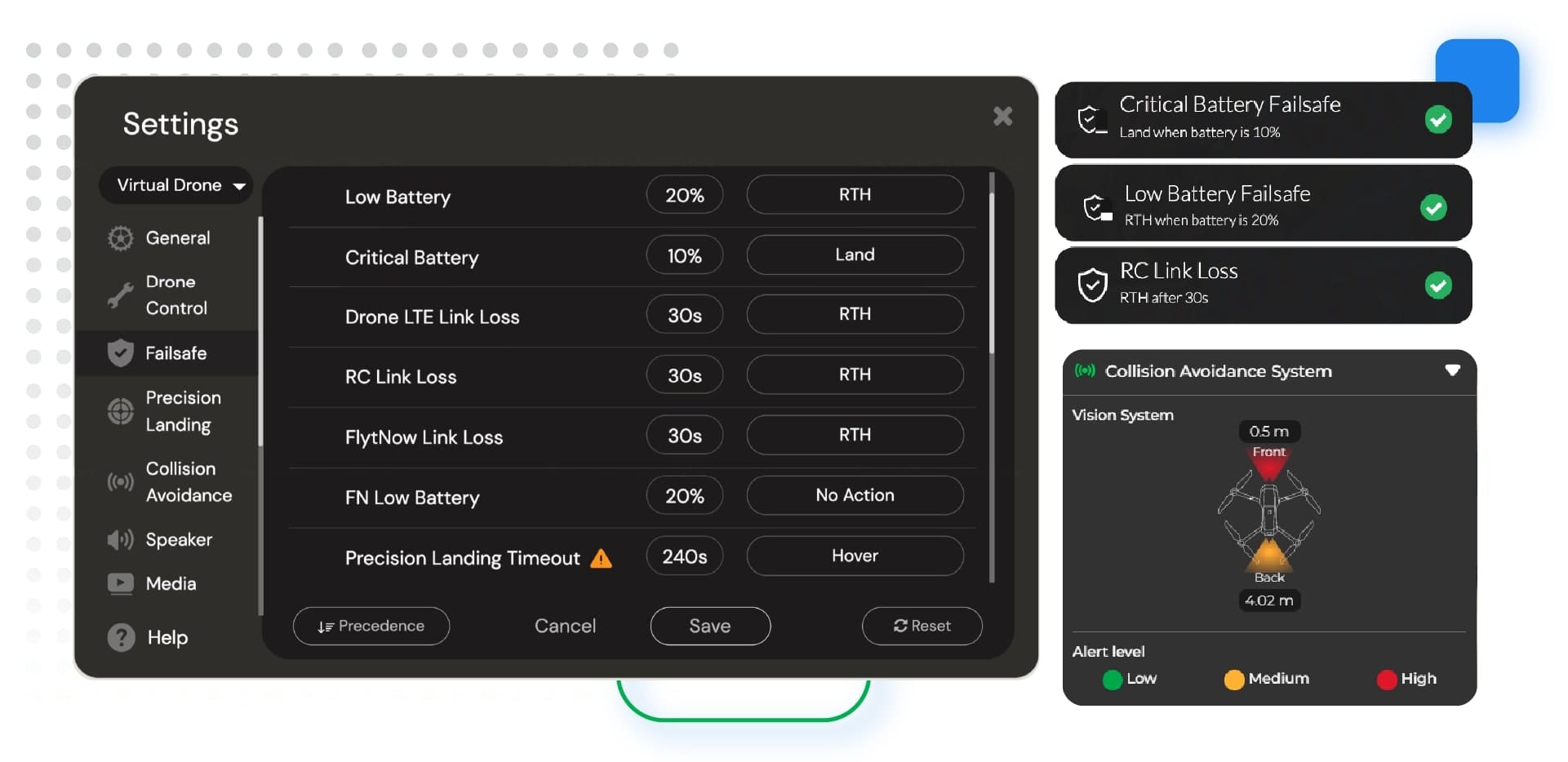
- Collision avoidance: FlytNow enables collision avoidance by constantly scanning the drone's surroundings for potential obstacles. A real-time radar map with red, yellow, and green indicators is displayed on the operator's screen, allowing them to safely maneuver the drone around obstacles. This feature provides an additional layer of safety and helps prevent accidents, making it easier to navigate through challenging or unknown environments.
3. Better precise documentation:
The advanced video and image capture capabilities of FlytNow provide operators with a clear and accurate view of the plant in real-time. Moreover, the cloud media sync feature enabled operators to conveniently upload media from their drone's SD card directly to a pre-configured private cloud storage (AWS S3), without any disruption in their workflow. The archived data can be stored, organized, and shared across various stakeholders directly from the FlytNow dashboard to increase operational efficiency and situational awareness.
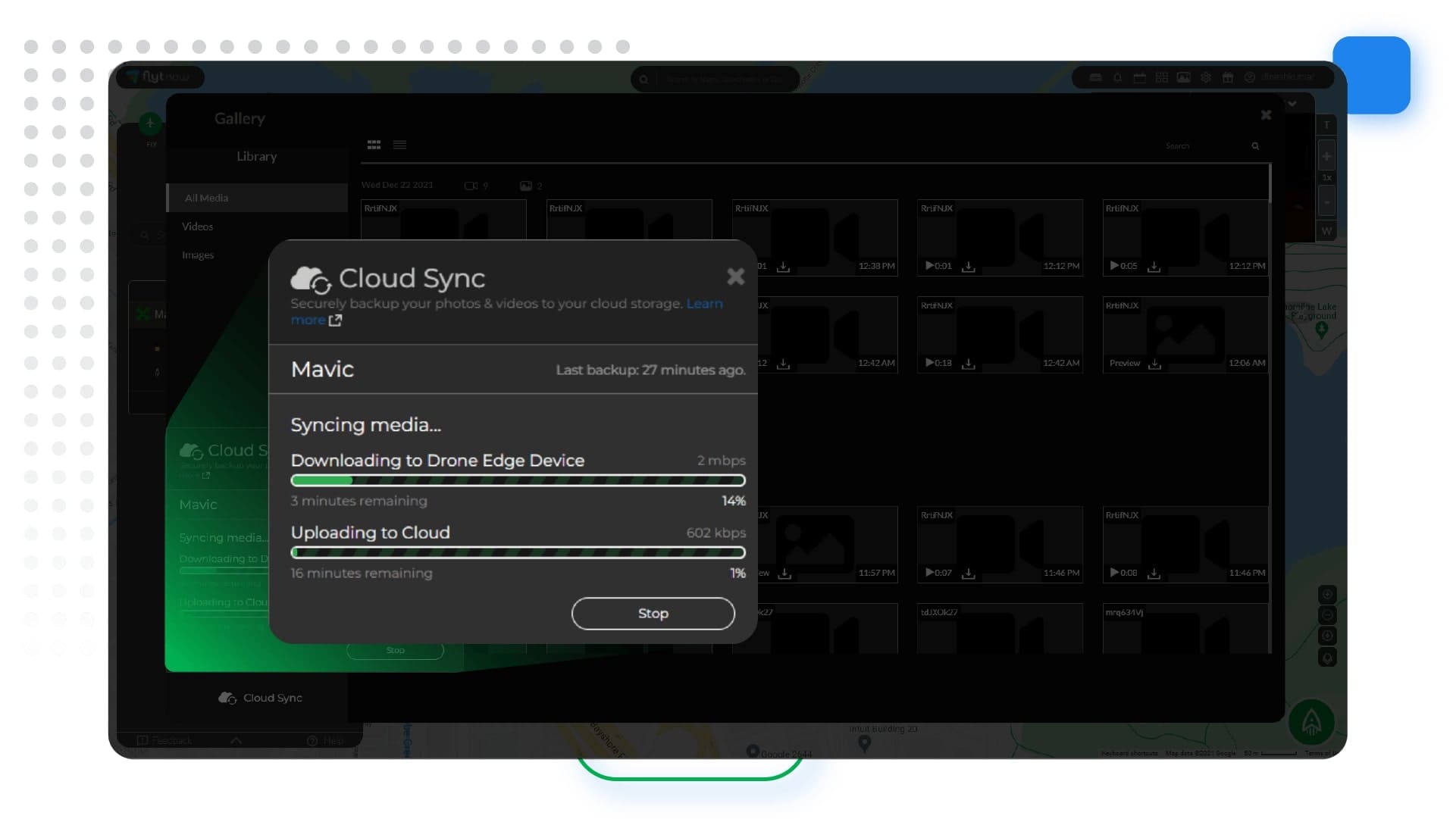
4. Real-time guest share:
By using FlytNow, remote inspections can be conducted from a centralized command center and shared in real-time with stakeholders both inside and outside the plant. With role-based access, security officers can access the video feed on their preferred device and take action as needed. The "Video Streaming Optimization" feature allows for optimization of the video stream for better FPS or picture quality even in areas with limited or poor bandwidth connections. The video below demonstrates a typical operation conducted at the Genelba Power Plant.
The Way Ahead for Pampa Energía with Autonomous DiaB Solution
As the second-highest per capita energy consumer in South America, Argentina faces increasing demand for electricity, driven by the need for space heating. With thermal power plants being the most reliable source of energy generation, their continuous operation is crucial to meet the country's energy needs.
Once the Pampa Energía's deployment of autonomous drones at the Genelba power plant proves to be successful in enhancing operational efficiency and reducing the risk of accidents, the company plans to expand its drone-in-a-box program to several other power plants, ensuring a safer and more efficient operation while maximizing the return on investment.
Achal Negi, Director of Business Development at FlytBase, highlights the potential drone-in-a-box systems hold for the future of thermal plant inspection and monitoring. He concludes by stating that: “Currently, manual inspection of thermal power plants is a time-consuming and potentially hazardous task for workers. By using autonomous drones for these inspections, energy companies can increase efficiency and safety for workers and reduce any potential down-time of the plant. Furthermore, the use of automated drones for thermal power station inspection with drones and docks offer more frequent and thorough inspections and also improve night-time security operations for power stations. We will see more autonomous drone-in-a-box deployments in power plants in the coming years.”
At NestGen ‘22, Marcelo Lopez, discussed their operations in detail. Watch the entire video to learn more:
The industry’s only virtual summit entirely dedicated to drone autonomy is back and bigger than ever!
To help the industry accelerate its transition to BVLOS ops, NestGen 2023 will bring together experts in BVLOS technology, autonomous drone operations, regulatory consultants and adopters of drone-in-a-box systems.
What to expect at NestGen 2023
The single-day, 11-hour virtual only event will include keynotes, sessions from some of the most prominent proponents and leaders of the commercial drone industry, deep dives into cutting-edge, modular drone docking stations, product updates and announcements, application-specific breakouts, and a plethora of virtual networking and engagement opportunities.
NestGen 2023 dates and times
9:30am – 8:30pm February 23rd 2023
Registrations to the event are free till 31st January 2023.
Go ahead and register now! https://flyt.link/nestgen-feb-2023
As the world's primary fuel sources, oil and natural gas are major industries in the energy industry and have a significant impact on the global economy. Demand for petroleum and petroleum products has only increased in the recent past due to global economic and population growth, as well as continual urbanization and industrialization.
The United States itself has more than 190,000 miles of liquid petroleum pipelines and over 2.4 million miles of natural gas pipelines. Pipeline transportation is safer, more efficient, and emits fewer GHGs than shipping by ship, truck, or rail.
The Current Challenges with Pipeline Inspections:
Pipelines are vital infrastructure for the transmission of oil and natural gas, connecting producing areas to refineries, chemical plants, home customers, and commercial demands. However, oil and natural gas are combustible and explosive substances that are typically delivered via high-temperature, high-pressure pipeline networks. Hereby, it is critical to monitor these pipelines to ensure that they are operating effectively.
However, traditional pipeline inspection methods have some issues, such as:
Use of crewed aircraft
Currently, the majority of energy companies use helicopters to monitor encroachment in potential pipeline Right-Of-Ways (ROW). Each expedition costs an average of $150,000, making more regular inspections than every six months almost impractical.
Foot Patrols
Once the aircraft confirms an encroachment, foot patrols, typically consisting of two personnel, are dispatched to these remote locations. Such manual site inspections take approximately 8 hours and cost approximately $500 merely to have a closer look and validate the threat.
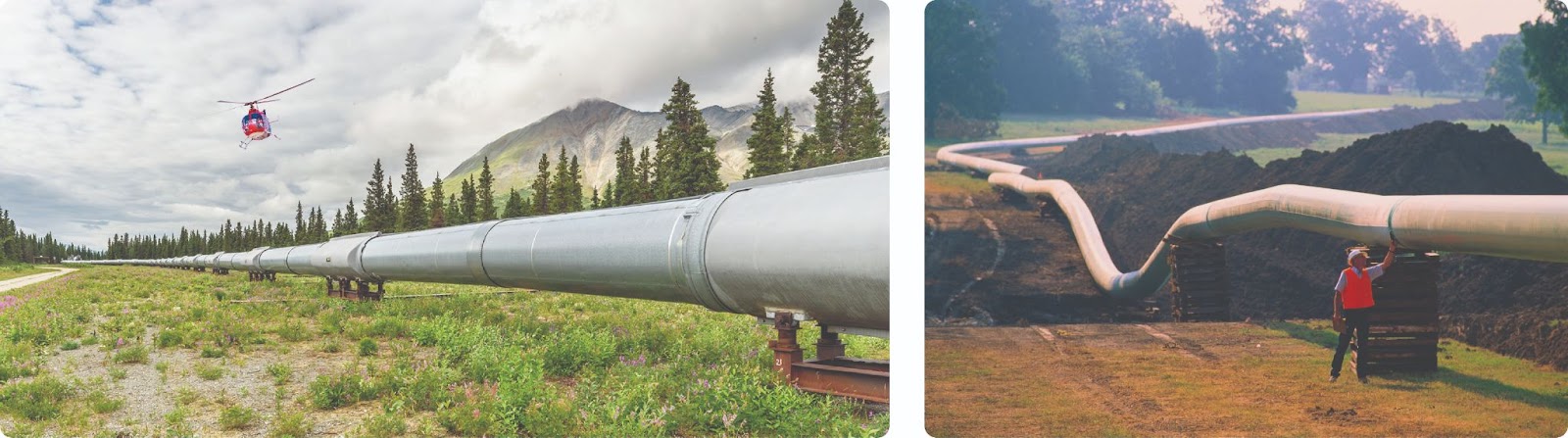
Inability to send crew at all times
Pipelines can be hundreds of kilometers long and can be spread over vast remote locations. Sending operators to such locations can put human life at risk. Hereby, it becomes quite difficult to send inspection teams to cover such areas at all times.
Time-consuming method
Traveling from one asset to another is frequently difficult. Operators may need to drive lengthy miles along gravel or dirt roads to visit several inspection sites. The distance and hard terrain may need a significant amount of time.

How can Drones with BVLOS Capabilities Help Oil and Gas Companies Secure Pipelines
Ease of travel between assets
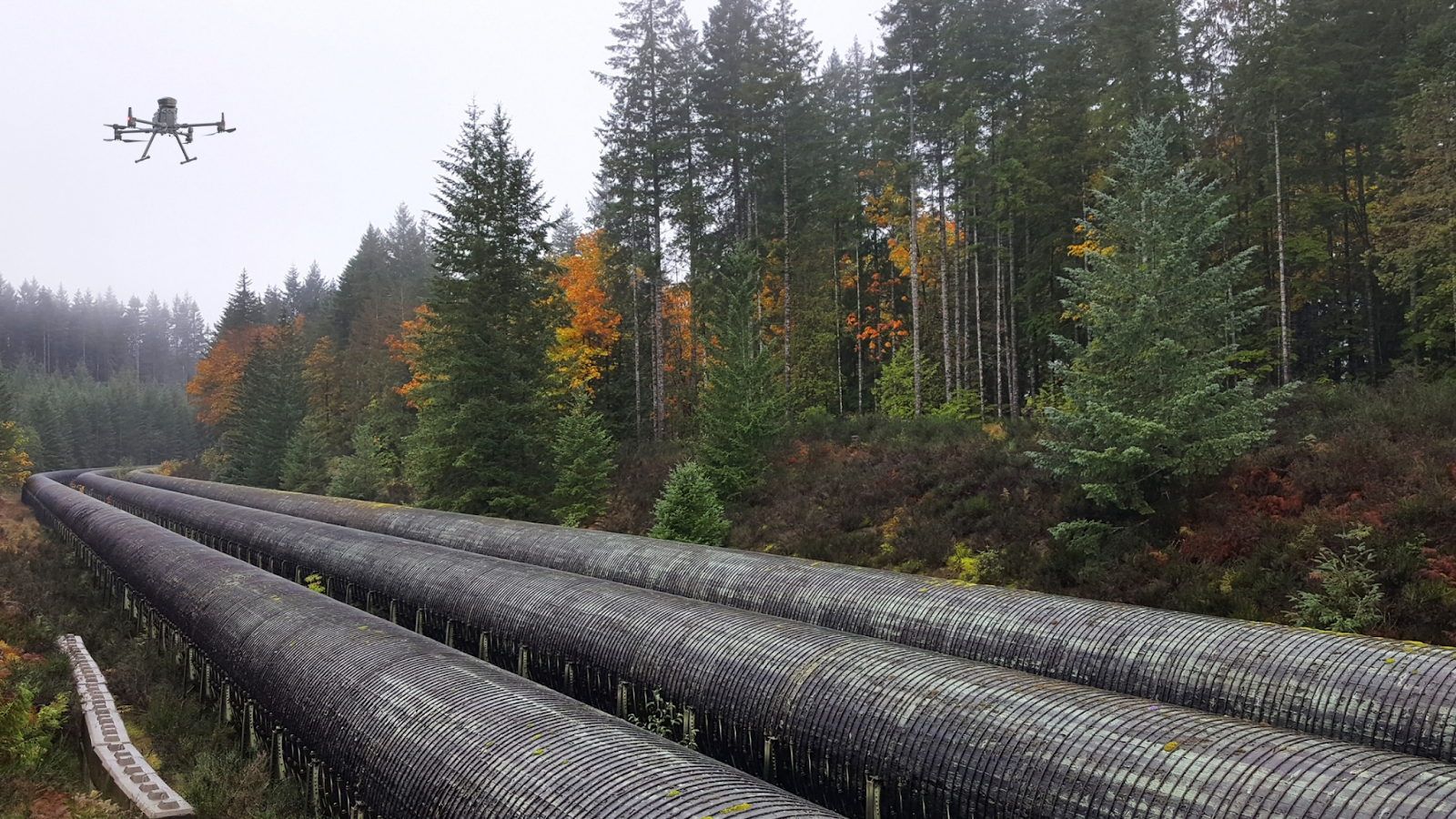
Traveling between assets during inspection operations might become challenging because these pipes can span thousands of meters. The team may be required to travel long distances and to distant regions where there is no adequate road infrastructure.
Operators must travel to the sites, assess the asset, review their data, and then drive to another asset. Furthermore, they must repeat the entire process until all assets have been inspected. This can take a significant amount of time which can be costly for an industry like oil and gas.
However, drones can travel vast distances and reach difficult-to-access locations. Additionally, using drone-in-a-box systems, eliminate the need for continual re-launching, packing, and landing of drones which is majorly faced in manual-led VLOS operations.
Increase worker safety
Oftentimes, assets are located on high terrains or difficult-to-reach locations. Operators may need to set up substantial scaffolding or dangle from ropes to inspect this equipment. Any mistake here can result in severe consequences. Despite the industry's strict regulations and safety standards, health and safety concerns persist. A BVLOS operation eliminates the operator's danger by allowing them to undertake the flight mission from any remote location.
Simplify early detection of pipeline leaks
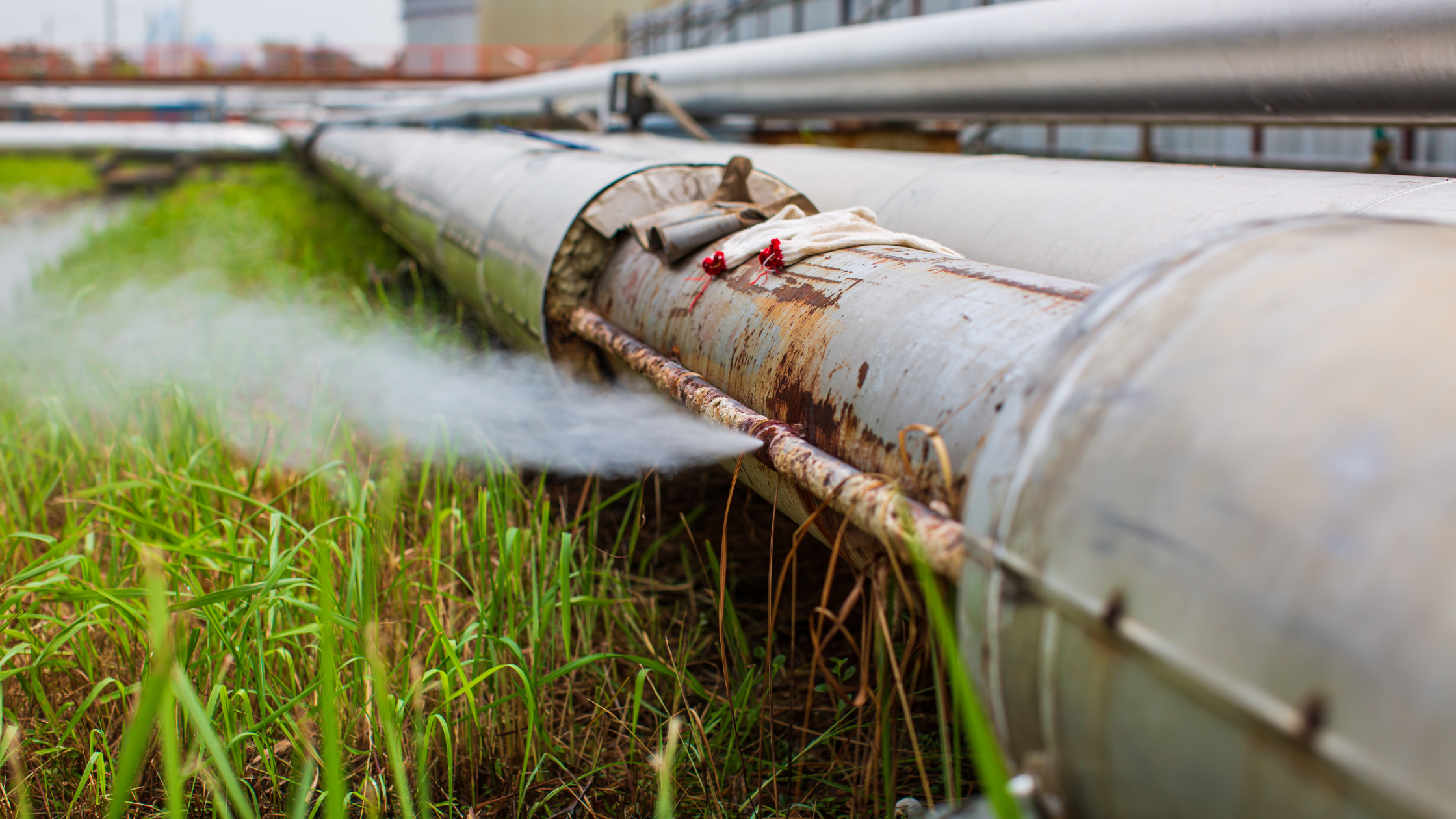
Drones are increasingly being used in the oil and gas industry for early detection of pipeline leaks. By using advanced drone technology including thermal cameras and visual or infrared cameras, these drones help the operators to identify gas leaks in storage tanks and pipelines with greater accuracy and efficiency than traditional methods.
These drones can easily access hard-to-reach areas and capture high-quality photos and videos of the pipelines and storage tanks. These data can be helpful to conduct image analytics for accurate and early detection of potential leaks or damage.
This allows operators to respond quickly and effectively to potential pipeline failure, minimizing the impact on the environment and reducing the risk of accidents. The use of drones also reduces the potential for human error, as operators can monitor the pipelines remotely, without the need for physical inspections.
Reduce heavy costs
Hiring a pilot and a helicopter, for example, can cost thousands of dollars. Regular inspections may become prohibitively expensive and time-consuming. Autonomous drone missions can minimize such costs while also minimizing human dependency.
Utilize readymade data and analytics via automated procedures
A human-led operation requires the operator to drive to the location and visually inspect the asset. Via autonomous operations, drone operators can run pre-planned drone flights and augment the inspection process. The drone will follow its routine, capture and store data which can be further assessed for detailed inspection as per need.
This enables the operator to quantify their assessment with turnkey data and analytics delivered via automated workflows. This simplifies the entire process and backs it up with data, which greatly aids decision-making.
Ability to scale operations
While examining pipelines spanning thousands of kilometers, it becomes nearly impossible to conduct manual operations consistently. However, autonomous drones can be scaled up and deployed readily to fit the business's needs as they can be programmed to conduct the desired tasks.
How FlytNow is Enabling BVLOS Operations
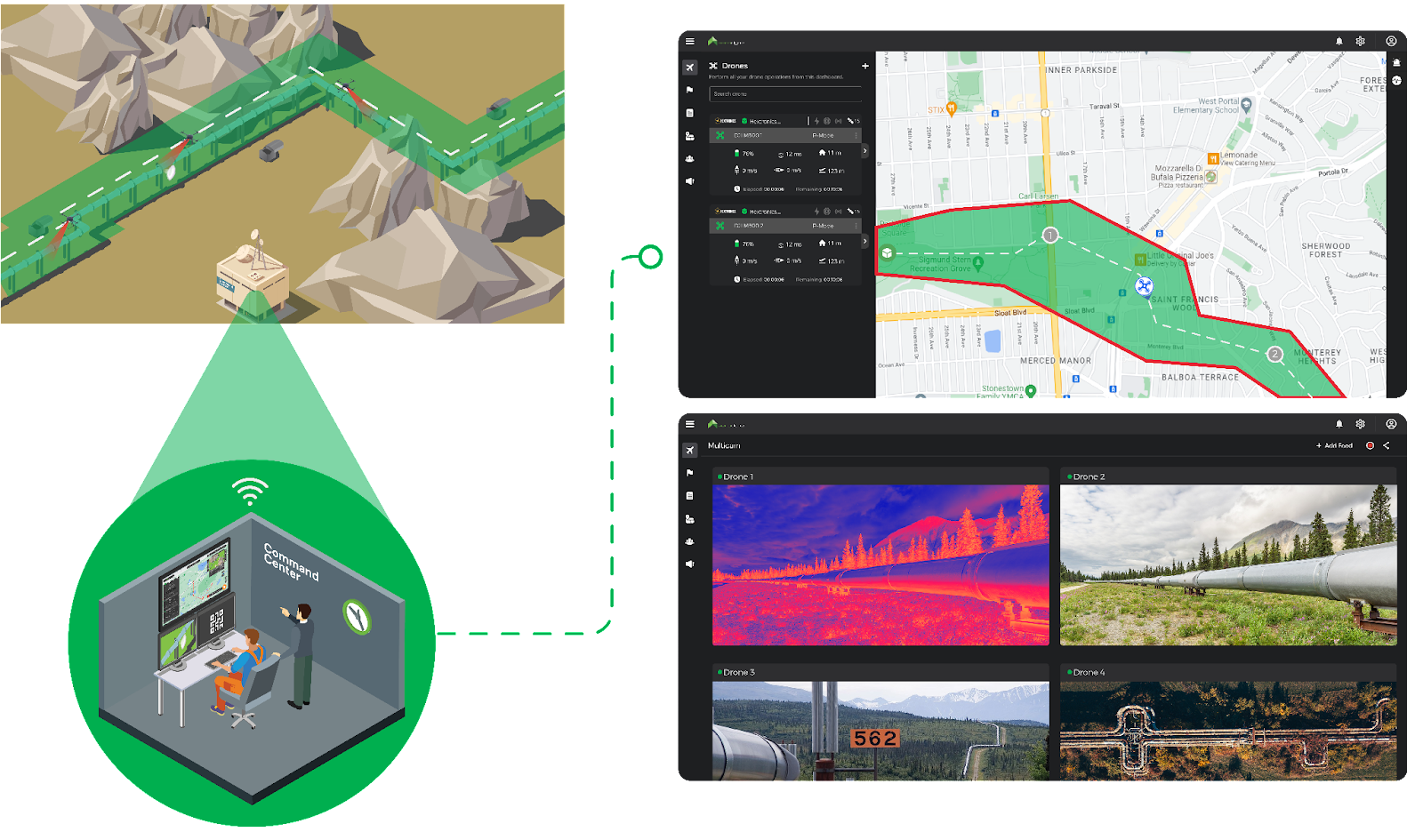
FlytNow is a cloud-based solution that enables the deployment and management of drones in just a few clicks, allowing you to manage your drone operations via a single web-based dashboard for a seamless experience. It helps you lower travel costs, reduce operation rounds, and increase productivity by saving travel time. It is integrated with ready-to-use intelligent modules, like collision avoidance, and precision landing, and integration with drone-in-a-box systems, which further helps you shorten your time to market.
The FlytNow software solution enables project managers to schedule pre-planned or on-demand flights from a command center located miles away from the base station. The drone takes off from the drone nest autonomously, flies its mission, captures real-time videos and images, and uploads them to the cloud.
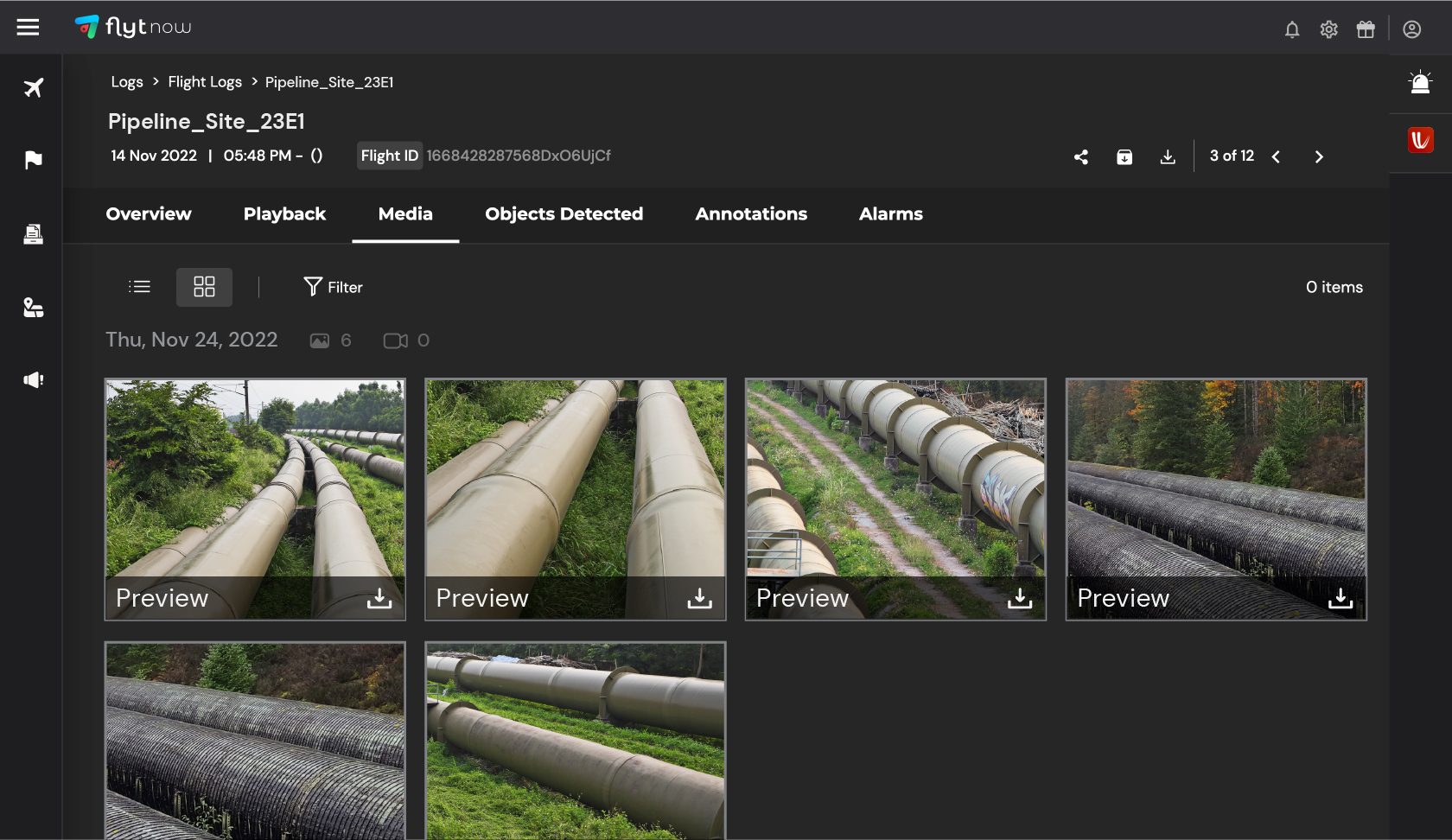
Following the flight, the drone returns to the docking station for battery swapping and storage. These stations can charge up to four batteries simultaneously and swap out the existing battery in less than 90 seconds, ensuring minimal downtime. Furthermore, because it is lightweight, it can easily fit on the back of a pickup truck and be moved from one location to another if necessary.
3rd party integrations in FlytNow, such as Casia G system by Iris Automation for detection and avoidance of cooperative and non-cooperative aircraft, Altitude Angel for airspace awareness, and others, assist to increase capabilities for greater insights and seamless BVLOS operations.
Leveraging Nested Drone Systems (NDS)
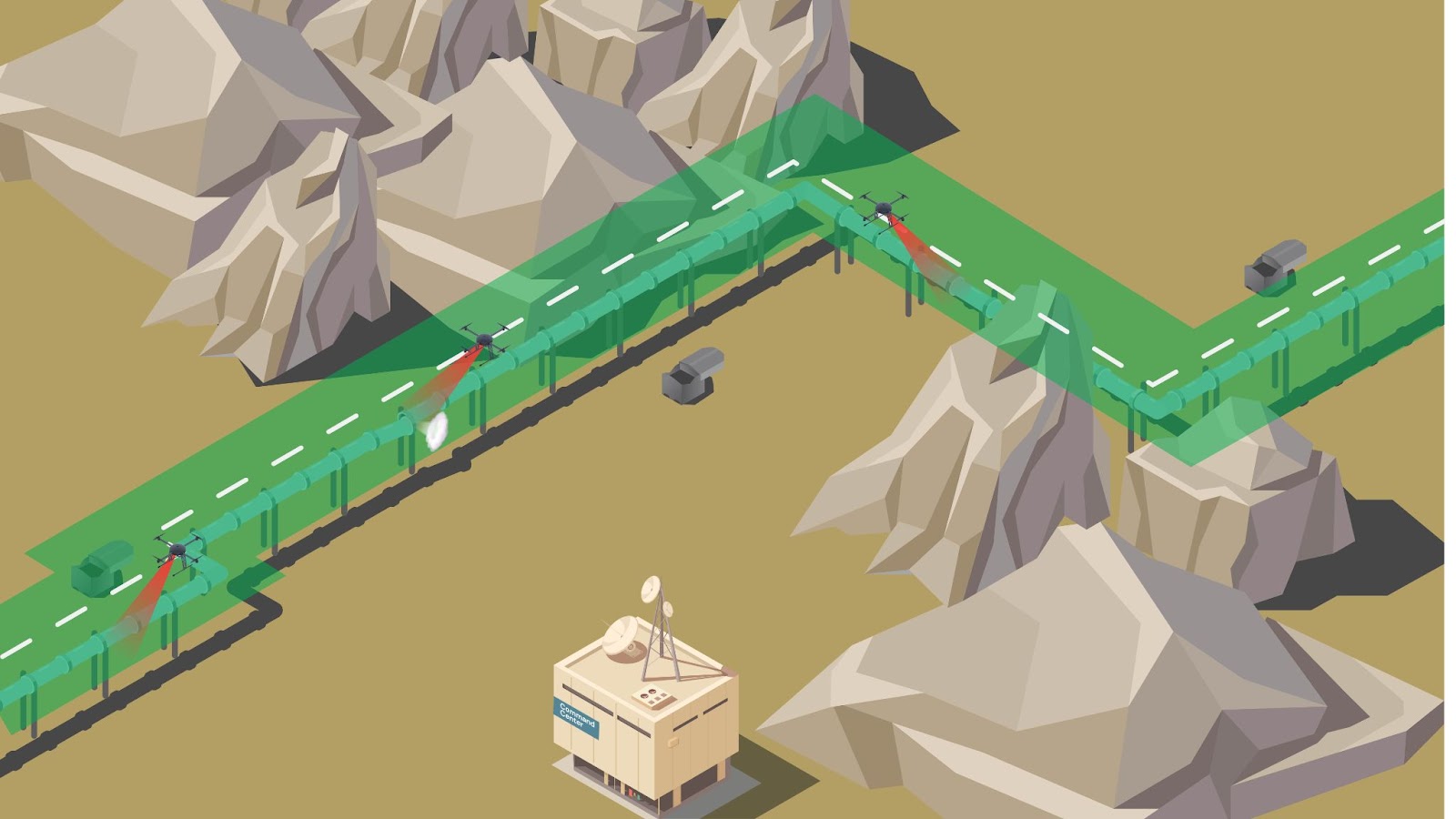
The Nested Drone Systems (NDS) can significantly improve the data collection process and transform how pipelines are inspected. It lets the drone operator conduct long-duration flights without the need to return the drone to the command center to recharge or swap the battery. With the nested drone system, energy companies would be able to quickly scale up, undergo a digital transformation, run safely, and boost productivity.
Nitin Gupta, Founder & CEO of FlytBase, Inc. concludes by stating that “Nested Drone Solutions are rapidly revolutionizing the way repeatable, high-frequency missions are conducted across use-cases. Maintenance of pipelines, spread over thousands of miles, is a great application of this technology with a significant ROI for the end-user.
FAQs
1) How can drones improve the safety of inspections on oil and gas pipelines?
Drones can play a vital role in improving the safety of inspections in the oil and gas industry. With their ability to fly closer to the ground, drones can provide high-resolution aerial data through the use of visual or infrared cameras. This allows for more precise and thorough inspections of pipelines, particularly in hard-to-reach areas.
By using drones, workers can avoid the potential dangers of inspecting pipelines on foot, such as exposure to crude oil leaks. Additionally, the use of drones allows for earlier detection of leaks, which can prevent potential disasters and safeguard the environment.
2) What are the benefits of using drones for pipeline inspections?
Drones provide several benefits for pipeline inspections, including accuracy and improved technologies. Using drones to detect leaks and identify potential issues can save costs and equipment compared to traditional inspection methods. Drones can also access dangerous terrain and provide quick emergency response.
In addition, using drones for regular inspection can improve worker safety by avoiding the need for workers to enter hazardous areas. Visual or infrared cameras on drones can monitor pipelines and identify potential issues, whether it be for gas or oil pipelines. With better data and improved maintenance, major accidents can be avoided through the use of drones for pipeline inspections.
3) How can FlytNow help in pipeline inspection using drone-in-a-box systems?
Using FlytNow-powered drones for pipeline inspection, operators can now easily detect any leaks in the pipeline with greater accuracy and efficiency than traditional methods. It allows the team to access difficult-to-reach areas and avoid putting any human in potential danger.
Furthermore, operators can get a real-time video stream of the assets, and also capture high-quality photos and videos of the pipelines and storage tanks. This significantly helps in conducting accurate inspections and detecting potential leaks or damage.
4) What can we expect in upcoming technologies in oil and gas pipeline inspection?
New technologies will include autonomous drones that are packed with a cost-effective platform that will help in inspecting pipelines, provide insight for maintenance activities, and identify human errors. Moreover, they will be equipped with a visual or infrared camera that can detect leaks or damage on its own and inform the team immediately.
5) What are some of the best drones for pipeline inspections in the oil and gas industry?
There are several drones that are well-suited for use in pipeline inspections in the oil and gas industry. Some options include:
- DJI Phantom 4 RTK: This drone has a high-resolution camera and RTK GPS for precise mapping and surveying capabilities.
- DJI Mavic 2 Enterprise Dual: This drone has a compact design and can fly in challenging weather conditions. It also has a dual thermal and visible light camera for identifying issues in pipelines.
- senseFly eBee X: This drone has a long flight time and can fly in autonomous missions to cover large areas quickly. It also has a high-resolution camera for detailed inspection.
- Parrot Anafi USA: This drone has a 4K HDR camera and is capable of flying in challenging environments. It is also lightweight and easy to transport.
Many commercial drone operations rely on several people in the field: usually a pilot, a payload/camera operator and sometimes additional domain experts depending on the mission type. In times of a pandemic - as we have it with Covid-19 at the moment - you want to avoid people being outside or travel as much as possible. But some drone operations can't be postponed - for example inspection of critical infrastructure, Search & Rescue or curfew enforcement. In this situations staff in the field should be reduced as much as possible to protect them and the entire population.
Sky Drone technology allows you to fully remote-operate a drone and its payload over a 4G / 5G cellular network. Even if your payload operator is in home quarantine - productive work for a mission critical project is still possible. He will be able to control the camera and gimbal from hundreds of kilometers away using low latency streaming technology, capture images and inspect them immediately from home.
Using Sky Drone technology we can help you to implement all of the following scenarios, minimizing or eliminating the need to send people to a target operating area.
Scenario 1: Pilot in the field, Payload Operator and Domain Experts operate remotely
The easiest way to get started is to reduce the staff in the field to the drone pilot only.
Both payload/camera operator and other Stakeholders can watch a low latency life stream from anywhere in the world, operate the camera and take still images for instant review.
Scenario 2: Safety pilot in close distance - Drone and payload operated remotely
The next step is to only have a safety pilot that can take over control of the drone in an emergency situation and to comply with relevant Line-of-Sight regulations. Both drone and payload are operated remotely via 4G/5G connection.
Scenario 3: Full remote operation - nobody needs to leave the house
Full Beyond Visual Line of Sight (BVLOS) operation via the 4G/5G network. This depends on local regulations and possible BVLOS licenses in your jurisdiction but allows you to execute your drone mission fully remotely without leaving your house.