Recognizing the growing importance of data safety and customization, Danish drone company Upteko has entered the market with its flagship product, the LARK drone.
Originally conceived for windmill inspection, the LARK drone has been developed to set a new standard for data security and versatility, and has quickly garnered attention for its data safety features and adaptability.
The LARK drone features robust data encryption mechanisms and a highly customizable design; engineered to meet the unique specifications of each customer, ensuring optimal performance and data safety in any scenario. Whether it’s precision agriculture, infrastructure monitoring, or environmental surveys, Upteko empowers its clients to tailor the LARK drone to their specific needs, without compromising on data security.
Setting new standards for data security & versatility
In the ever-evolving landscape of drone technology, the demand for data safety and customization has become paramount. As regulatory bodies tighten their grip on privacy and security measures, companies are facing unprecedented challenges in ensuring the integrity and safety of the data collected by their drones.
In this shifting paradigm, Upteko offers cutting-edge solutions that prioritize data security and customization.
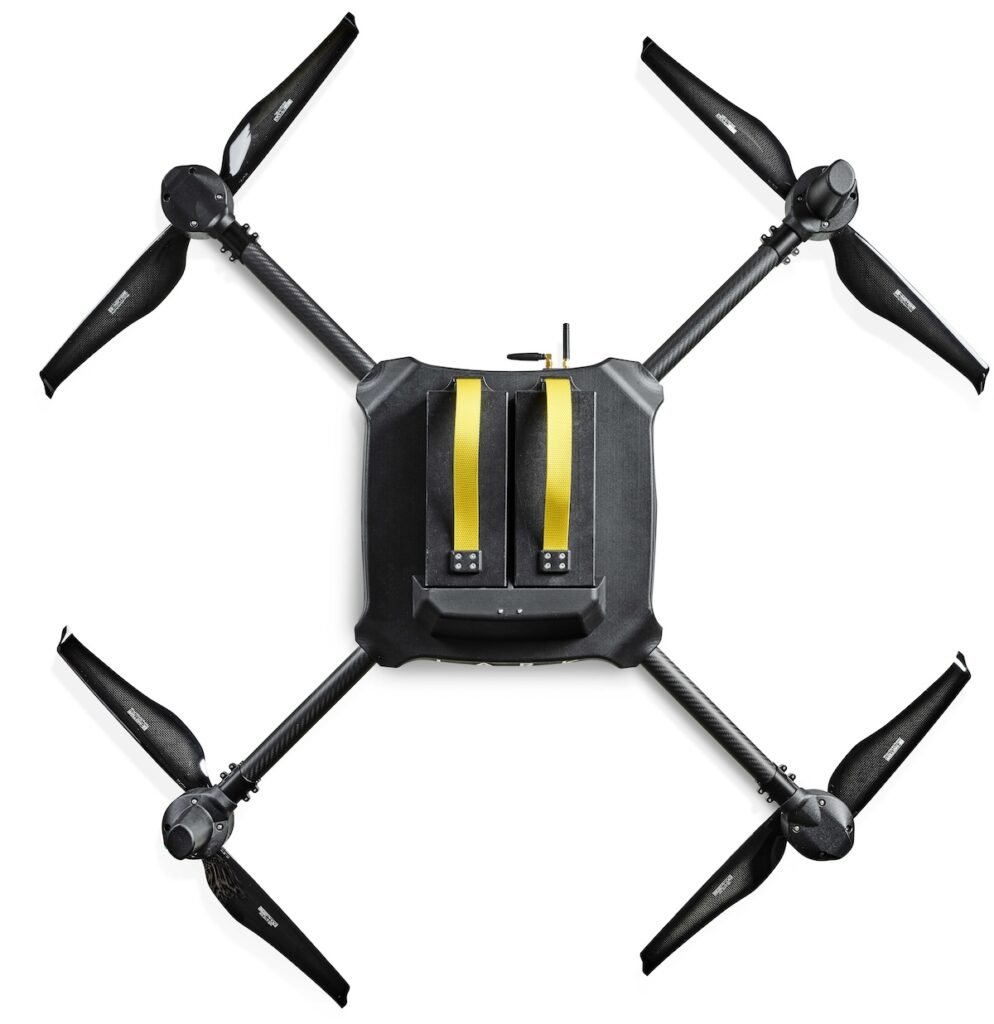
The drone industry is undergoing a profound transformation, driven by advancements in technology and an increasing need for data-driven insights across various sectors. From agriculture to infrastructure inspection, drones have become indispensable tools, providing real-time data and actionable insights like never before. However, with this proliferation of drone usage comes pressing concerns over data privacy and security.
Regulators worldwide are stepping up efforts to enforce stringent guidelines to protect sensitive information collected by drones. From stringent data encryption protocols to strict limitations on data storage and transmission, compliance with these regulations has become a top priority for companies operating in the drone industry. Failure to adhere to these standards not only poses legal risks, but can also undermine public trust in drone technology.
The versatility of the LARK drone has been a game-changer for businesses seeking reliable and secure drone solutions. With its advanced payload options and modular design, the LARK drone can seamlessly adapt to evolving industry requirements, providing unparalleled flexibility and scalability.
Whether it’s integrating specialized sensors for precise data collection or implementing custom software solutions for enhanced analytics, Upteko offers a comprehensive suite of services to meet the most demanding operational needs.
Read more here: Upteko