Drone technology has undeniably transformed the traditional approach to industrial inspections, making them an essential part of their maintenance procedures. Traditional inspection methods, such as scaling cell towers, wind turbines, or scaffolding to examine industrial boilers, are being phased out in favor of drone inspections. Service providers can easily capture all necessary visual data without compromising inspector safety.
Autonomous drone technology has made this process even more simpler & cost-effective. With the help of drone-in–a-box systems, companies can now perform inspections in hard-to-reach areas without the need for specialized personnel to be on site. By a simple push of a button, energy companies can gather accurate information from remote locations, such as gas facilities, solar farms, and remote oil fields.
In this blog post, we will discuss the benefits of using autonomous drone technology in industrial inspections, using case studies and insights shared at a NestGen'23 session by industry experts Kevin Toderel from RMUS Canada and Grant Hosticka from DJI, North America.
.jpg)
Phased Approach for Autonomous Drone Operations
To ensure regulatory compliance and operational safety, Kevin recommends a phased approach to drone implementation for industrial inspections. The approach involves a step-by-step progression in terms of removing human intervention and increasing automation in drone operations. The framework can be tailored to meet the unique needs of each project and it has proven to be effective, particularly in Canada. The four phases of this approach are as follows:
- Licensed Pilot with a RC and Visual Observer (VO): In the first phase, the drone operation starts with a licensed pilot operating the drone via RC while also acting as a visual observer. This requires no specific licensing and counts as a regular flight. The only difference between this and a regular flight is that the pilot will be operating through the dock, but will essentially be ready to take control with the RC in the event of an emergency.
- Dock and Software with VO having Return-to-Home Functionality: The pilot is removed from the drone operation in the second phase, and the drone is piloted remotely using cloud-based software. However, this operation remains within the visual line of sight since a visual observer (VO) is present on the site with a return-to-home functionality to take control of the drone in case of an emergency.
- Dock and Software with Complete Autonomy within VLOS: In the third phase, the drone operations are completely autonomous and the dock and the drone are remotely controlled from the command center without a licensed pilot or a VO on site. These operations however are conducted within the visual range and will test the ability of the drone to navigate on its own.
- Dock and Software for Fully BVLOS Ops: Drone operations extend beyond the range specified in phase 3 in the final phase, necessitating a waiver from the regulatory authority of the operating geography. These operations require the use of technology such as Detect and Avoid, UTMs, and others.
.png)
Applications of Drones in the Energy Industry
Let's take a closer look at some of the applications in the power generation industry where autonomous drone operations can generate value or make the most sense:
Drones in Solar Farm Inspection
The solar industry is constantly looking for ways to streamline solar panel maintenance and reduce the time required for upkeep. A potential answer to this problem is the use of drones. Autonomous operations can make the process more efficient, allowing for faster and more accurate inspection.
"Maintenance personnel still spend far too much time looking for problems rather than maintaining equipment," Kevin points out, "and this is where autonomy and AI applications will provide the most bang for the buck."
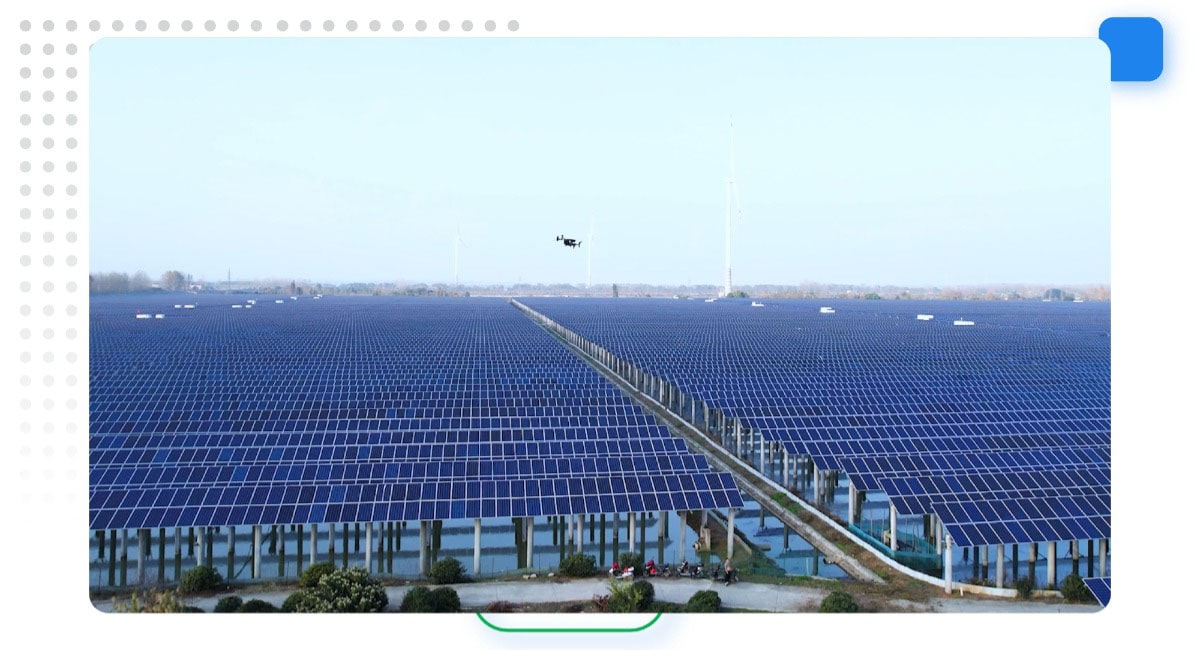
The drones can be programmed to autonomously take off from their docks at a scheduled time, follow specific flight paths, capturing images of the solar panels from different angles. The images are then analyzed using AI algorithms to identify any faults or issues, such as damaged panels or vegetation growth. This information is relayed in real time to maintenance teams, who can then prioritize their efforts accordingly.
Additionally, the same system can be used to track the progress of the solar farm's construction process and conduct security patrols. Designers can identify and correct any issues that may arise during the construction phase. Furthermore, the construction process can be made more transparent by providing regular updates to stakeholders.
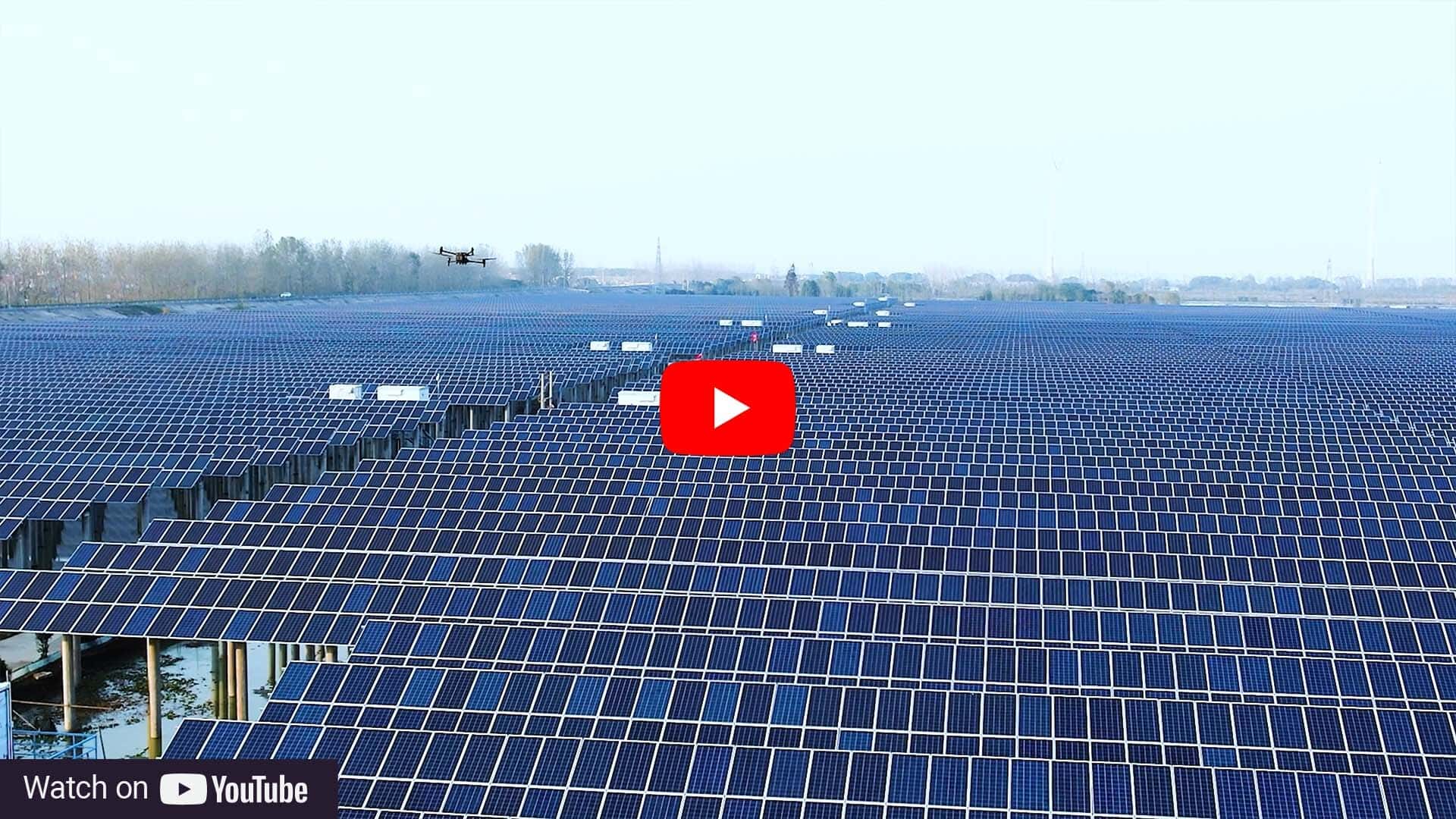
Drones in Wind Turbines
The wind energy industry has long recognized the value of UAVs for blade inspections.
Even if you do not consider fully autonomous blade inspections, there are countless applications for drone technology in wind farms, especially if the drone is ready to be deployed at all times.
One of the most significant advantages of using autonomous drone systems for wind turbine inspections is the ability to perform predictive maintenance and servicing. By regularly inspecting wind turbines, energy companies can detect damages and defects before they become severe, reducing the risk of downtime and increasing the lifespan of the turbine.
Kevin highlights, “Operators often have to suspend maintenance if they suspect there’s ice on the blades. One of the biggest use-case for drone-in-a-box automated operations would be to send drones to check if there is ice on the blades and whether it is safe for the team to go up for inspections.”
Drones for Inspecting Dam Spillways
The use of autonomous drone systems in detecting and responding to dam spillways has been gaining traction in recent years. Energy companies can reduce the risk of personnel injury by monitoring and inspecting the dam spillway from a safe distance.
.png)
Kevin shares an account about how they received a BVLOS waiver to conduct drone operations after a fatality occurred during a flood caused by dam water release. Before releasing the water, autonomous drones can perform a quick inspection of the spillway.
He emphasizes that each use-case has its own set of technical requirements. Considerations like whether the drone is below grade or whether an LTE or RF connection is necessary had to be made in the case of the dam spillways.
Drones for Inspecting Site Security
One of the most common use-case of autonomous drone systems is for site security and the power generation industry is no exception. Kevin mentions a case wherein the asset owner had to unfortunately experience an act of vandalism that caused extensive damage to the infrastructure. The damage caused by the vandalism totaled around four million dollars. If there were to be a drone docking station to monitor this frequently and mitigate this, the ROI from installing it would be immediately achieved.
Kevin was able to easily schedule repetitive perimeter patrol missions with high frequency using DJI Dock, even at temperatures ranging from 0 to 6 degrees. Furthermore, with software solutions such as FlytNow, motion detection sensors or existing security systems to trigger drone deployment based on alarms can be easily integrated. Drone-in-a-box system for site security helps in reducing liability, avoiding repairs, downtime and property loss, making it a critical use case for a wide range of assets.
What Lies Ahead
Implementing autonomous drone operations in industries like power generation could present several challenges such as navigating the complex regulatory frameworks, technical development, and partnerships with third-party providers. Kevin emphasizes that, in order to address regulatory challenges, industry players collaborate with regulatory bodies and use phased approaches to build trust over time.
Technical challenges are addressed through R&D investments and collaborations with third-party providers to integrate complementary technologies. Partnership challenges are addressed by developing integrated solutions through open APIs and software development kits. Through these solutions, the benefits of autonomous drone operations can be realized while ensuring safety and regulatory compliance.
He concludes the session by stating the importance to remember that there is “no one-size-fits-all” solution in the drone industry. Different use cases will require different sensors and aircraft, and there will be a variety of hardware and software options available to meet these needs.
When considering partners for proof of concept projects, it's important to find a partner who can take a holistic approach to the project, considering all aspects of the drone solution from regulatory engagement to data hosting and security. With the right partners and solutions in place, drone-in-a-box systems have the potential to greatly improve efficiency, safety, and security across a wide range of industries.