Amidst the continuous evolution of uncrewed aerial systems (UAS) technology, DJI has once again raised the bar by introducing DJI Dock 2, which is on its way to release worldwide, on 26th March 2024. To know more about Dock 2, feel free to contact us.
The previous version of DJI Dock has proven its effectiveness across various industries. In Alaska, the Department of Transportation and Public Facilities (DoT&FR) deployed the docking station to enhance safety measures during avalanche and geohazard incidents. Thanks to its resilient design and rapid charging capabilities, the dock facilitated continuous drone operations, particularly crucial for Drone as First Responder (DFR) missions.
Meanwhile, in Bisamberg, Austria, it played an important role in inspecting a major substation, ensuring the integrity and security of essential energy infrastructure. By enabling regular inspections and maintenance checks, it provided the Austrian Power Grid’s (APG) team with real-time updates on the substation's condition. This approach significantly minimized downtime by detecting faults early on, thereby helping improve the reliability of the electricity supply throughout Austria.
The DJI Dock 2, along with the DJI Matrice 3D and 3DT drones, is expected to reshape the approaches of industries engaged in surveying, inspections, and public safety in their remote, uncrewed operations.
Curious about what DJI Dock 2 has to offer? Explore this buyer's guide to get all the information you need. Discover its features, compatibility, and important factors to help you make an informed decision.
Which features set DJI Dock 2 apart from its predecessor?
The DJI Dock 2 distinguishes itself from DJI Dock, through several impactful enhancements.
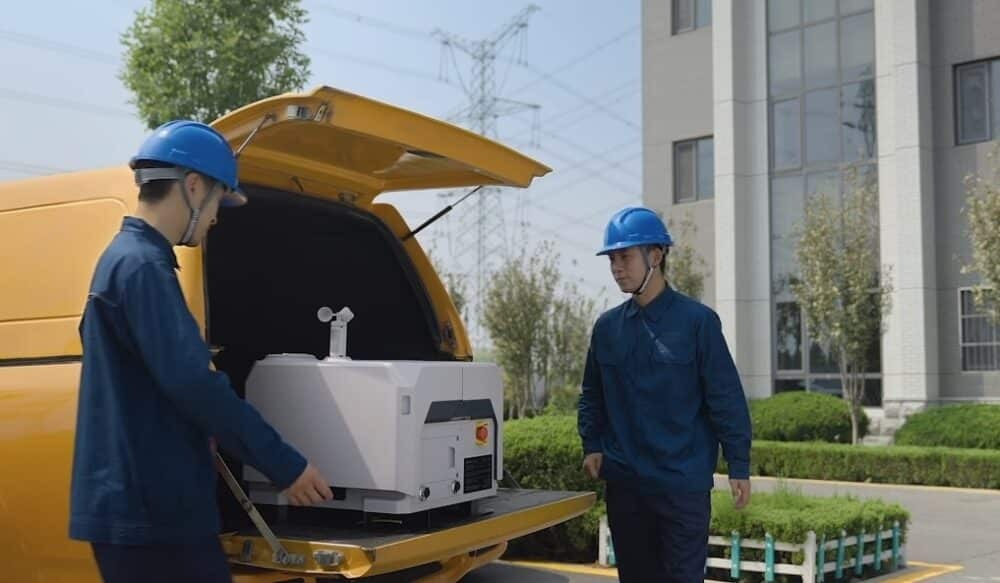
1. Weight and Design:
DJI Dock 2 boasts a 75% reduction in volume and a 68% reduction in weight compared to its predecessor. Weighing only 34kgs, this version facilitates easier, quicker, and more cost-effective deployment of autonomous drone fleets.
2. Durability and Weather Resistance:
Dock 2 retains the durability of its predecessor with an IP55 rating, being resilient against harsh weather conditions, dust, and water.
3. Coverage and Efficiency:
The DJI Matrice 3DT and Matrice 3D drones have a maximum flight time of 50 minutes and a maximum operational range of 10km when used with the DJI Dock 2, surpassing the capabilities of DJI Dock which offers a maximum flight time of 40 minutes and a maximum operational range of 7km.
4. RTK Modules:
The integrated dual RTK modules on the DJI Dock 2, coupled with internal and external fisheye cameras, provide real-time environmental feedback. This enables real-time blade detection, safety checks, and takeoff in just 45 seconds, given that there is a robust network signal.
5. Charging Capabilities:
Dock 1 charges drones from 10% to 90% in around 25 minutes at 24V output, while Dock 2 achieves this from 20% to 90% in roughly 32 minutes at 12V. Both docks offer over 5 hours of independent charge for safe Return-to-Home (RTH) functionality.
6. Improved Landing & Power Supply:
DJI Dock 2 enhances landing stability and reliability through an improved image recognition system and a sloped design that guides the drone for precise positioning within the dock. For added security, it comes with a built-in backup battery that provides over 5 hours of operation in case of power loss or remote locations. Additionally, DJI Dock 2 only requires biannual maintenance, minimizing downtime and costs.
7. Third-party Payload Support:
DJI Dock 2 offers increased versatility by supporting third-party payloads through M3D/M3DT E-Port. This allows for mounting payloads like spotlights, speakers, and parachutes, expanding the drone's capabilities and ensuring safety.
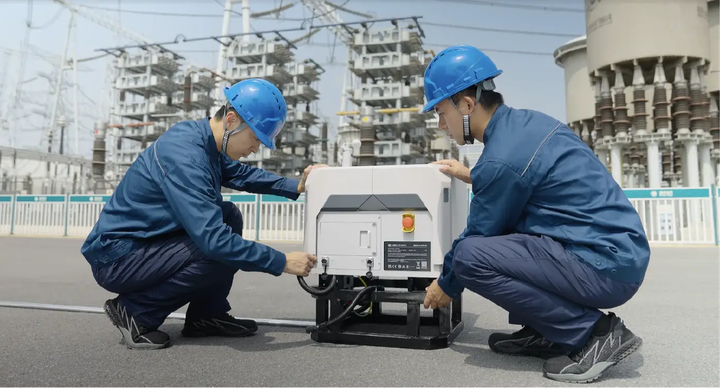
Here’s a comparative study of the specifications of the DJI Dock 1 and Dock 2
Dock 2 and its seamless operations with compatible drones
The DJI Dock 1 was designed for use with the DJI Matrice 30 and 30T drones. The key features of these drones include a 41-minute flight time, 12 m/s wind resistance, and compatibility with various third-party payloads.
However, DJI Dock 2 is designed to work seamlessly with the new DJI Matrice 3D and Matrice 3DT drones.
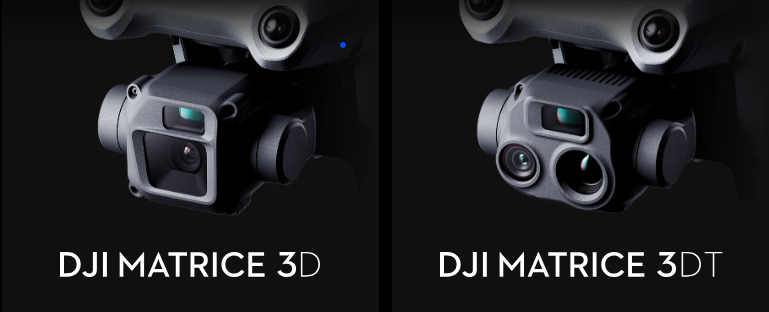
The Matrice 3D
- Best suited for applications such as surveying and mapping
- Equipped with a telephoto zoom camera and a wide camera with a special shutter
The Matrice 3DT
- Specifically designed for tasks like public safety, surveys, and inspections
- Features wide-angle, telephoto zoom, and thermal cameras, simultaneously capturing regular and heat-sensitive video.
Both drones share impressive features like an IP54 protection level, up to 50 minutes of flight time, a maximum speed of 47 mph, and a strong battery life that can handle 400 cycles, significantly reducing operational costs. Additionally, they have an RTK module, enabling them to land with remarkable accuracy when used with the DJI Dock 2.
Use cases and applications of DJI Dock 2
Multiple case studies have proven that the DJI Dock 1 can help transform applications like security and inspections where close monitoring and surveillance are required.
Interestingly, along with the previously mentioned use cases of Dock 1, due to the wide-angle, telephoto zoom, and thermal cameras of Matrice 3D/3DT, the DJI Dock 2 can now also be used for advanced mapping and surveying.
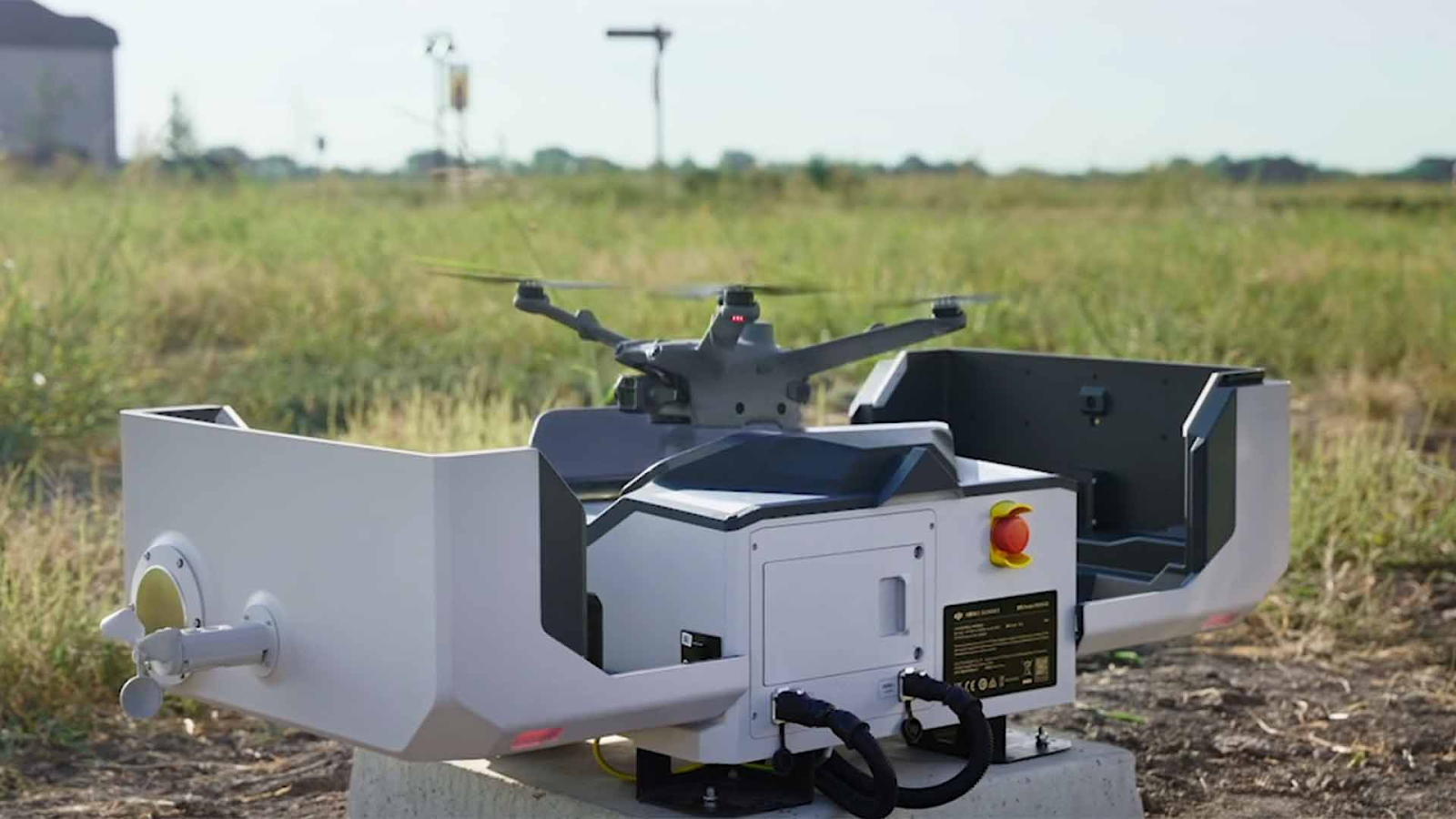
Let's explore the applications of Dock 2 in detail:
- Surveying and Mapping: Matrice 3D's high-precision cameras and the DJI Dock 2's autonomous deployment capabilities make it ideal for surveying and mapping large areas, construction sites, or infrastructure projects.
- Security and Inspections: The Matrice 3DT's thermal camera and long flight time are well-suited for security patrols, perimeter monitoring, and inspecting critical infrastructure like pipelines or wind turbines.
- Emergency Response: The DJI Dock 2's quick deployment and the drones' ability to operate in various weather conditions make them valuable tools for search and rescue operations, fire response, and disaster assessment.
- Public Safety: The Matrice 3DT's thermal and zoom capabilities can assist law enforcement in search operations, crowd monitoring, and crime scene investigation.
DJI Dock 2 integration with FlytBase Software Platform
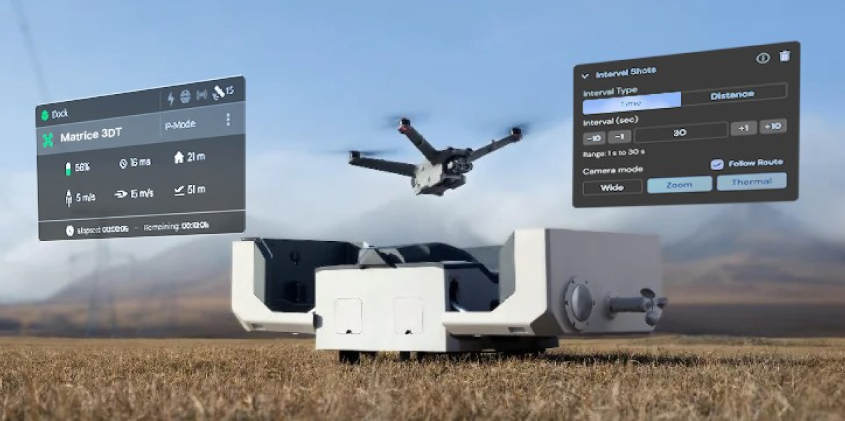
The DJI Dock 2, powered by FlytBase, will offer a comprehensive solution for remote drone operations. FlytBase is an enterprise-grade drone autonomy software platform that enables efficient autonomous drone operations, allowing missions to be planned and scheduled in advance and executed with minimal human intervention. FlytBase integration with DJI Dock 2 will offer customizable and scalable features suitable for various use cases, including inspections, surveillance, surveying, and security.
By incorporating a variety of Beyond Visual Line of Sight (BVLOS) components – such as parachutes, detect-and-avoid systems, uncrewed traffic management, and weather systems – FlytBase ensures that drone operations are reliable and secure.
Leveraging FlytBase, customers and partners have successfully obtained BVLOS certifications from top aviation authorities in 10 countries, including the FAA in the United States, EASA in Europe, CASA in Australia, SACAA in South Africa, JCAB in Japan, and CAAM in Malaysia. The platform also goes beyond basic mission planning by offering advanced features like dynamic route planning and customized flight workflows, all designed to align with regulatory standards.
In addition, FlytBase prioritizes data security by adhering to leading data protection standards. The platform is ISO 27001, SOC2 Type II certified, and GDPR compliant. To know more about the integration of FlytBase with the DJI Dock 2, feel free to contact us.
Conclusion
In conclusion, the DJI Dock 2 marks a significant advancement over its predecessor, DJI Dock 1 in the drone autonomy industry. Offering improved features and performance at an affordable price, DJI Dock 2 leads the way in remote flight operations, setting new standards for efficiency and reliability in autonomous aerial operations and making it a must-have for industries embracing drone technology advancements.