Since the highly anticipated launch of DJI Dock 2 and the advancements it brings, it has captured the attention of enterprise users, DSPs, and system integrators.
Its compact size, easy portability, and improved efficiency, combined with the upgraded abilities of supported drones like the DJI Matrice 3D and Matrice 3TD, are expected to enhance applications like mapping and surveying, among other applications.
While multiple third-party applications and products support the DJI Dock 2, FlytBase stands out by providing a comprehensive platform that leverages its potential and makes it enterprise-ready. In this blog, we will learn how FlytBase now helps you deploy fully automated, secure docked drone operations for enterprise applications with DJI Dock 2.
Top 5 reasons to choose FlytBase for your DJI Dock 2 operations
FlytBase seamlessly integrates with DJI Dock 2, providing an enterprise-grade drone autonomy software solution that includes workflow integration, flight automation, fleet management, flight safety measures, and robust data security features for efficient drone operations. Following are some of the reasons why you should choose
1. Flinks: Flinks, short for FlytBase Links, are connectors that help integrate the FlytBase platform with a wide range of external software apps and hardware devices. Users can fully automate enterprise drone workflows with pre-built Flinks or create custom ones with FlytBase APIs and SDKs.
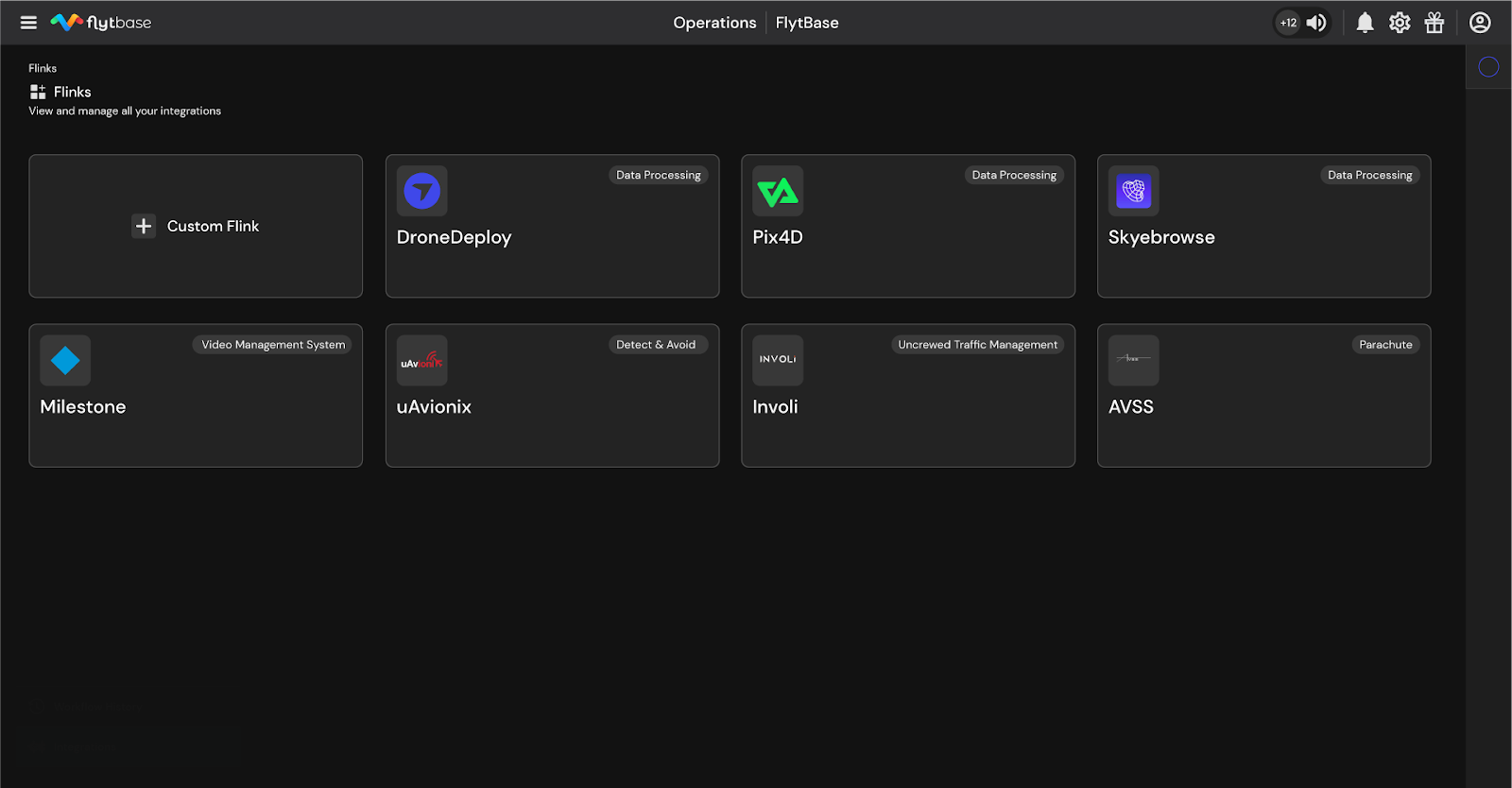
2. Flight safety and compliance: FlytBase ensures comprehensive drone safety with a range of features, including custom pre-flight checklists, collision avoidance, and configurable failsafes. Users can also create geofences and 2D No Fly Zones (NFZ) to maintain secure operations. Additionally, FlytBase alerts users to potential airspace threats and offers mitigation suggestions to help maintain a safe airspace.
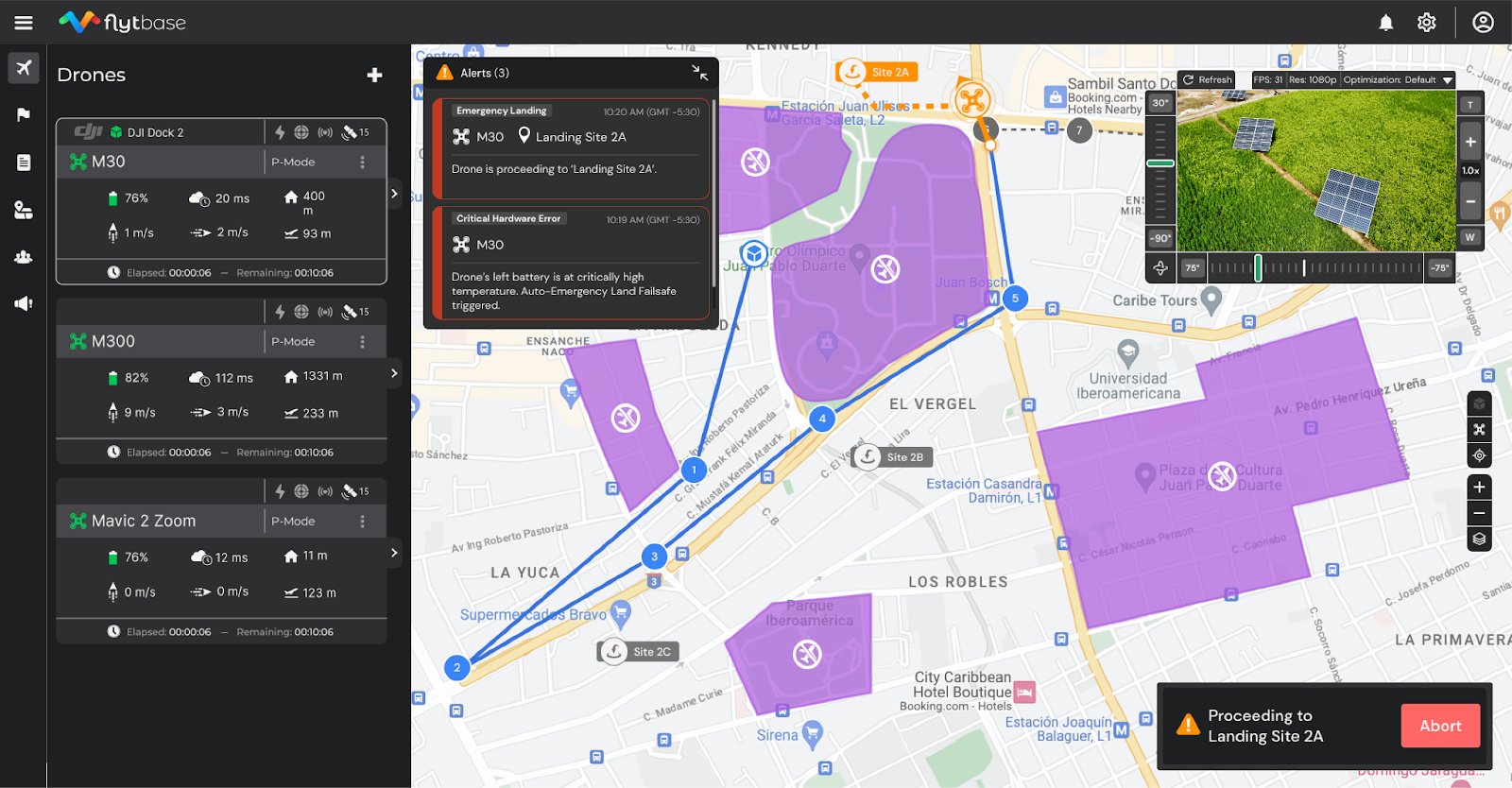
3. Robust data security: With multiple layers of protection that include secure data transfer, encryption, network configuration, application-level controls, and flexible deployment options, the FlytBase platform is designed with security in mind. We also use tools to help us enforce compliance with our internal security policies.
4. Hardware agnostic platform: You can seamlessly integrate and deploy FlytBase with multiple docking stations, drones, and third-party payloads while being able to manage the fleets with a centralized dashboard.
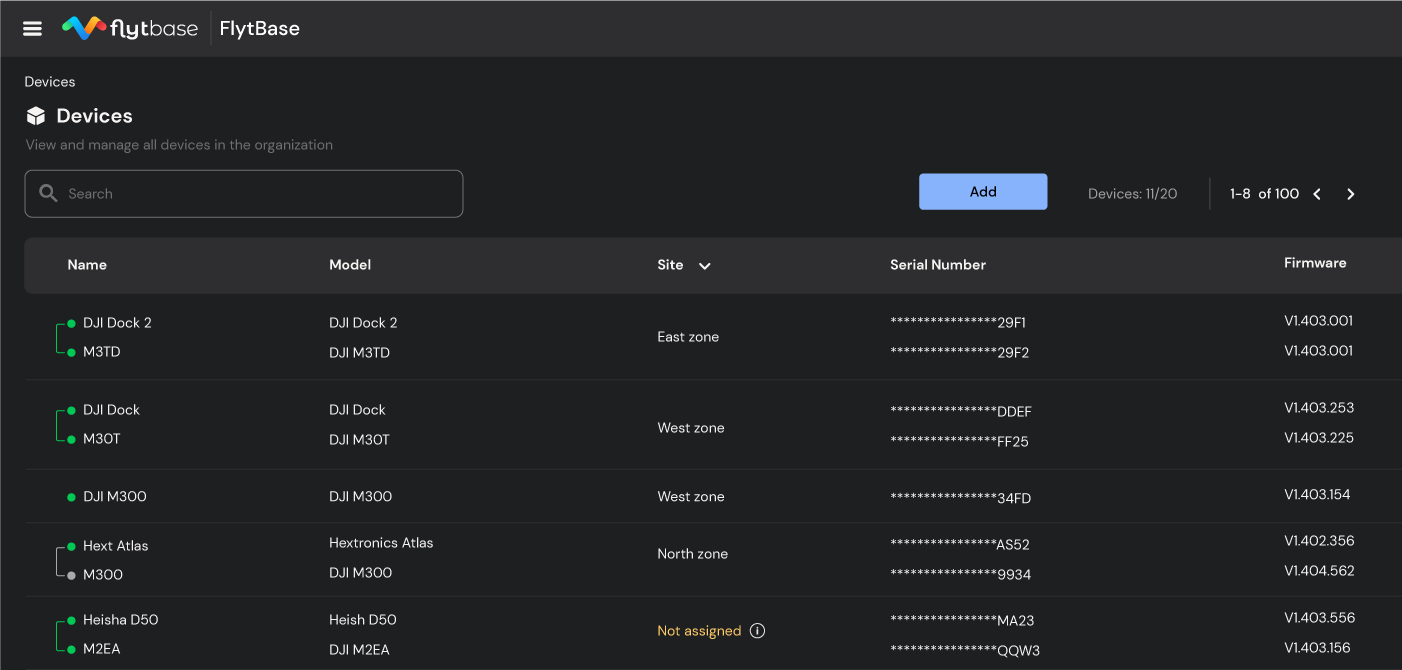
5. Enterprise-grade support: FlytBase provides enterprise-grade support via calls, emails, and chat, with the option to upgrade to custom SLAs. This helps dedicated business and technical account managers enhance customer and partner success, as well as provide on-ground support for extensive or critical deployments.
In addition to numerous other features, FlytBase enhances your DJI Dock 2 operations, making them enterprise-grade and exceptionally efficient. Now, let's take a look at FlytBase's approach to data security and its flexible deployment options for ensuring robust data protection.
Protect your drone data with FlytBase Shield
Large enterprises, government entities, and organizations managing critical operations face a major challenge in keeping their data safe and secure. Why is this so crucial?
Well, they handle vast amounts of sensitive information like proprietary business data, classified government information, and critical infrastructure. The drones capture this data, and any breach could lead to significant consequences, such as financial losses, damaged reputations, or even threats to public safety.
This is where FlytBase Shield comes into the picture to offer a comprehensive suite of security services designed to safeguard drone docks and data with multi-layer protection.
With our robust encryption methods, like AES-256, you can ensure that your sensitive data is protected at rest and in transit. Additionally, we take security measures for our user accounts with the help of:
- User account security with OAuth 2.0, Single Sign-on (SSO)
- Integration with Google and Microsoft accounts
- Adherence to industry cybersecurity standards such as SOC2 Type II, ISO 27001, GDPR, CIS, and NIST
This gives our customers peace of mind that their data and operations are safe.
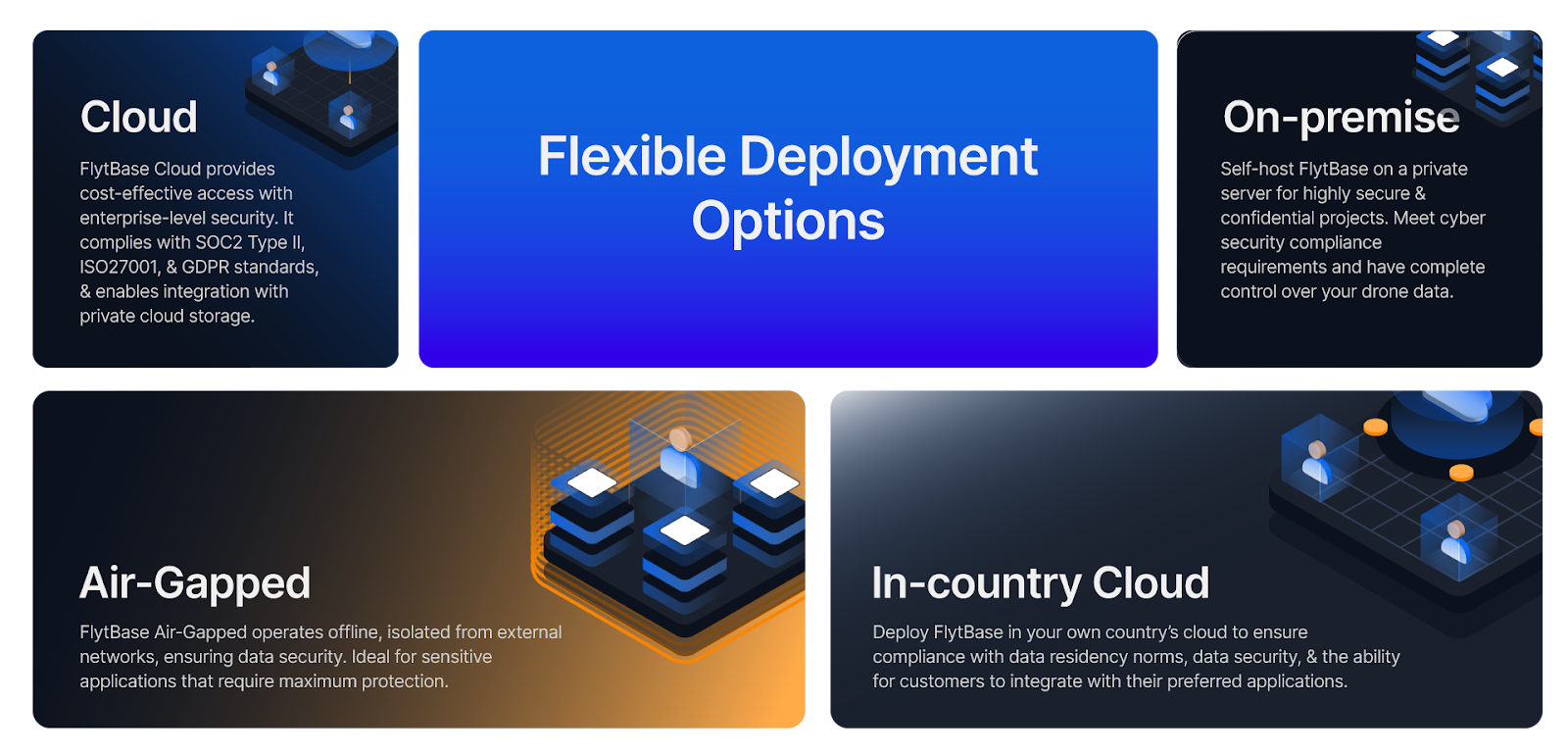
FlytBase provides a range of deployment options for the DJI Dock 2, including the choice to operate within a separately managed AWS environment, offering an additional layer of security and privacy by being physically isolated from our multi-tenant cloud infrastructure.
- Cloud: FlytBase Cloud provides cost-effective access with enterprise-level security. It complies with SOC 2 Type II, ISO 27001, and GDPR standards, and enables integration with private cloud storage.
- In-country Cloud: Deploy FlytBase in your own country’s cloud to ensure compliance with data residency norms, data security, & the ability for customers to integrate with their preferred applications.
- On-premise: Self-host FlytBase on a private server for highly secure & confidential projects. Meet cyber security compliance requirements and have complete control over your drone data.
- Air-Gapped: FlytBase Air-Gapped operates offline, isolated from external networks, ensuring data security. Ideal for sensitive applications that require maximum protection.
Having explored FlytBase's data security measures, let's now learn about BVLOS operations, where FlytBase equips your drone operations with advanced capabilities for safe and efficient Beyond Visual Line of Sight (BVLOS) flights.
Integrate your go-to apps and devices in a single click with Flinks
Using multiple platforms and systems in enterprise drone operations can create inefficiencies and pose safety risks. To solve these issues, FlytBase recently announced the launch of Flinks.
But what is Flinks?
Well, Flinks allow users to effortlessly connect the FlytBase platform with critical business systems such as alarm systems, video management, data processing, and more. By eliminating the need for complex, time-consuming manual interventions, Flinks enables enterprises to incorporate autonomous drones into their existing operations seamlessly.
Flinks includes six different integration types:
- Alarms: To integrate various alarm systems for drone response to incidents like motion sensors, fire alarms, and dispatch systems.
- Data Processing: To integrate data processing applications that help generate high-resolution maps, surface and 3D models, and reports tailored to specific applications.
- Live Streaming: To connect drone & dock video feeds with Video Management Systems (VMS) and other video storage or analytics applications for site security operations and incident response.
- Mission & Logs: To export detailed drone missions and data to apps that help manage resources, batteries, and flight logs.
- Detect & Avoid: To integrate third-party cooperative & uncooperative aircraft detection systems to ensure safety and compliance with airspace regulations.
- UTMs: To integrate uncrewed traffic management systems for real-time airspace awareness.
How FlytBase makes your drone operations BVLOS ready
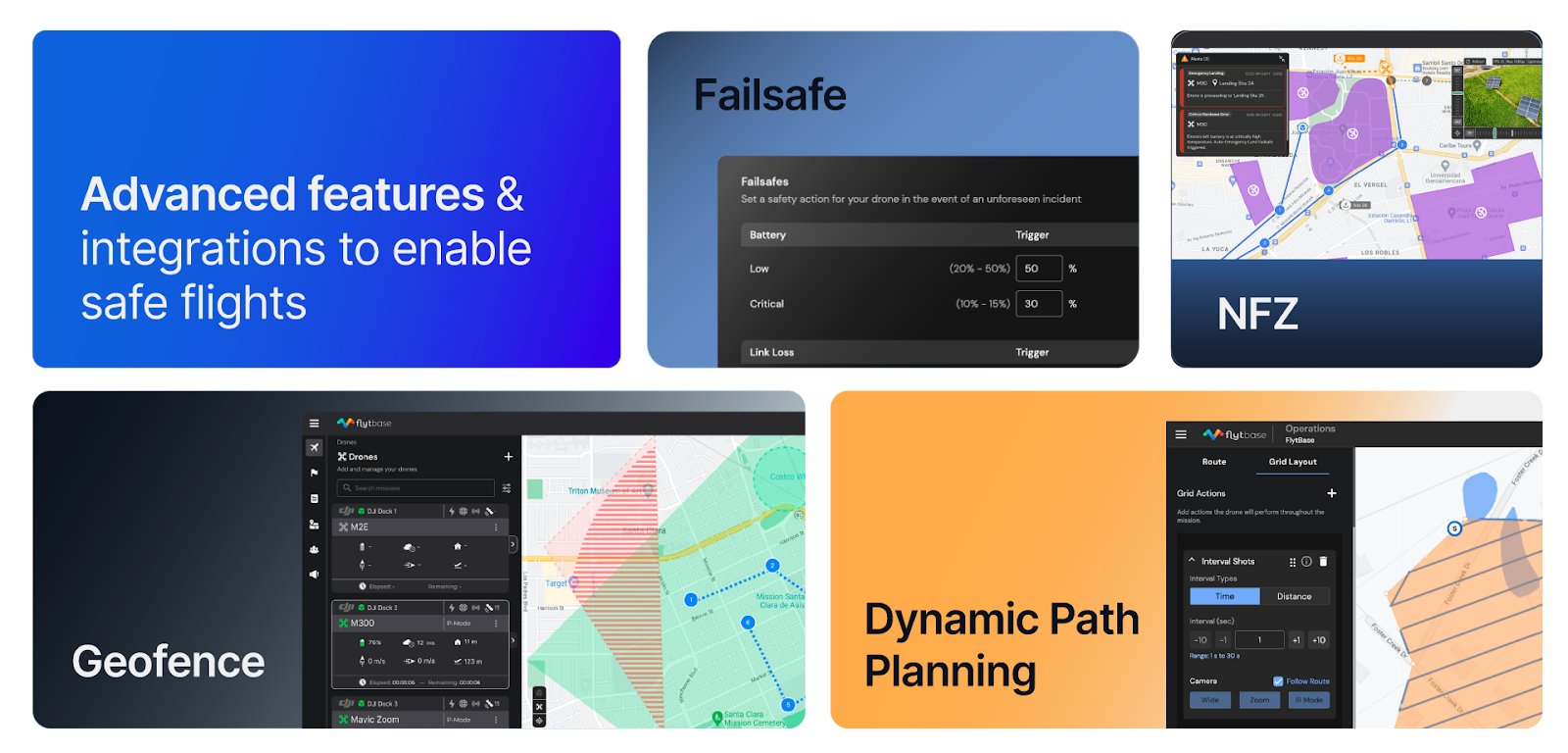
Flying Beyond Visual Line of Sight (BVLOS) is a significant milestone for various industries. With FlytBase and DJI Dock 2, your drone operations can seamlessly transition to BVLOS operations, with essential features and capabilities that ensure safe and efficient flight beyond visual range.
- Advanced Flight Planning Routines: FlytBase offers advanced flight planning routines tailored for BVLOS operations. Dynamic path planning, corridor fly zones, No Fly Zones (NFZ), Smart Return-to-Home (RTH), and customized flight workflows ensure compliance with regulatory requirements and efficient navigation in complex airspace.
- Geofencing and No Fly Zones: FlytBase enables users to create Geofences and No Fly Zones, ensuring compliance with local regulations and safety protocols. These virtual boundaries restrict drone flight in designated areas, minimizing the risk of unauthorized operations and ensuring airspace integrity.
- Flight Logs: FlytBase provides detailed flight logs that offer a comprehensive overview of each mission. Operators can review vital information such as flight path, altitude, speed, device status, and media captured during the mission. These flight logs enhance operational transparency, facilitate post-flight analysis, and support regulatory compliance efforts.
- BVLOS Documentation Templates: FlytBase simplifies obtaining waivers and approvals for BVLOS operations with pre-built documentation templates. These templates streamline the application process, facilitating regulatory compliance and expediting approval for extended drone flights.
- Third-party integrations for BVLOS flight safety: FlytBase integrates with third-party detect and avoid systems, Uncrewed Traffic Management (UTM) services, external ADS-B, and parachute recovery systems using Flinks. These integrations enhance safety by providing real-time alerts on intrusions, conflicts with nearby aircraft, and automatic parachute deployment in case of system failure.
Find out which BVLOS enablers have partnered with FlytBase to make flights safer. visit: https://www.flytbase.com/flinks
After learning about multiple aspects essential for conducting safe, secure, and reliable autonomous drone flights, let's dive deeper into the applications of the DJI Dock 2 with FlytBase across diverse industries.
Automating drone operations across industries
Applications like mapping and surveying are becoming more efficient and advanced, thanks to the DJI Dock 2, powered by FlytBase. The highly efficient cameras of the Matrice 3D/3TD drones make mapping and surveying more accessible and cost-effective than ever before. FlytBase simplifies creating grids over an area, especially for mapping and surveying. Users can precisely control parameters like Ground Sampling Distance (GSD) and overlap, ensuring accurate data collection.
Additionally, FlytBase's Flinks enable seamless integration of third-party apps and systems, further enhancing the versatility and capabilities of the DJI Dock 2 for various applications beyond mapping and surveying.
- Public Safety: Equipped with autonomous drones, first responders gain rapid situational awareness during emergencies, aiding in law enforcement and Search and Rescue (SAR) missions. With remote control and management features, operators can efficiently oversee operations from remote or mobile command centers, ensuring swift and coordinated responses to public emergencies.
- Construction: FlytBase and DJI Dock 2 can be used as a monitoring system that helps automate data collection, enabling real-time tracking of construction progress. Conducting mapping and site analysis becomes effortless, facilitating effective planning, design, and asset inventory management.
- Mining: Deploying drone fleets for routine missions, such as equipment inspections and progress reporting, becomes easier. Real-time video data capture helps monitor and survey, ensuring efficient stockpile management to prevent mine hazards.
- Security and Surveillance: Deploying drones for aerial monitoring and security patrols becomes seamless and efficient with the DJI Dock 2. In addition, by automating routine missions and scheduling patrols, with FlytBase, operators can ensure 24x7 monitoring of properties, enhance security systems, and easily safeguard assets
What lies ahead?
FlytBase with DJI Dock 2 enables a wide range of applications in sectors like public safety, mining, construction, and more while prioritizing data security with a robust system. In addition to this, the seamless integration with third-party systems via Flinks enhances the capability to automate, streamline, and ensure secure drone operations, offering an enterprise-grade experience.