Better than an Xbee and cheaper Hobby King 433Mhz Radio Telemetry Kit 100mW
Ran this wee puppy at 57,600 full duplex no issues at 1/4 mile with the RX inside my neighbors brick post box. Seems to penetrate the masonry better than a 2.4Ghz Xbee and its half to a quarter of the price the price especially if you buy from Sparkfun.
Like the Xbee it resumes comms very quickly after a power cycle which is pretty essential for RC usage.
Arduino Xbee Receiver Arduino Nano V3.0 Microcontroller Board from hobby king
http://kiwitricopter.blogspot.co.nz/2013/10/rx-tx-csharp-to-arduino.html
Features:
• Very small size
• Light weight (under 4 grams without antenna)
• Receiver sensitivity to -121 dBm
• Transmit power up to 20dBm (100mW)
• Transparent serial link
• Air data rates up to 250kbps
• Range of approx 1 mile
• MAVLink protocol framing and status reporting
• Frequency hopping spread spectrum (FHSS)
• Adaptive time division multiplexing (TDM)
• Support for LBT and AFA
• Configurable duty cycle
• Built in error correcting code (can correct up to 25% data bit errors)
• Demonstrated range of several kilometers with a small omni antenna
• Can be used with a bi-directional amplifier for even more range
• Open source firmware
• AT commands for radio configuration
• RT commands for remote radio configuration
• Adaptive flow control when used with APM
• Based on the HopeRF HM-TRP radio module, featuring an SiLabs Si1000 RF microcontroller
A quick test at 57,600 Baud seems like a great product and well priced at US$29.99
XBee Pro 60mW Wire Antenna - Series 1 (802.15.4)
US$37.95 AND YOU NEED 2
An interesting price point comparison between Sparkfun and HobbyKing on another useful and in this case identical product. HK are almost 80% cheaper
Arduino 9DOF ArduIMU Controller ATmega328 (ACCEL/MAG/GYRO)
US$29.99
Same product from Sparkfun 9 Degrees of Freedom - Razor IMU
US$124.95
So HK sell this identical device for almost 80% less

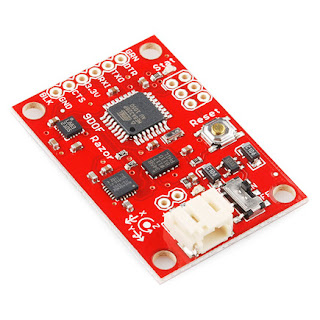