We are excited to announce our latest FlytBase release, a significant step forward in enhancing drone operation control, expanding functionalities, and offering advanced solutions for aerial data capture and analysis. Key highlights include the integration of the Thrustmaster joystick, renowned for its precision and ergonomic design, which revolutionizes drone and payload control in remote setups.
Additionally, we introduce Payload 2.0, advancing your drone's thermal imaging and sensing capabilities, and our innovative Live Map Annotations, designed to improve mapping, navigation, and team collaboration.
Thrustmaster Joystick Support
Central to this update is our integration with the Thrustmaster joystick, specifically the Thrustmaster T.16000M Space Sim Duo Stick, known for its precision control and ergonomic design. This integration transforms the way operators control both the drone and its payload in a remote setup, providing:
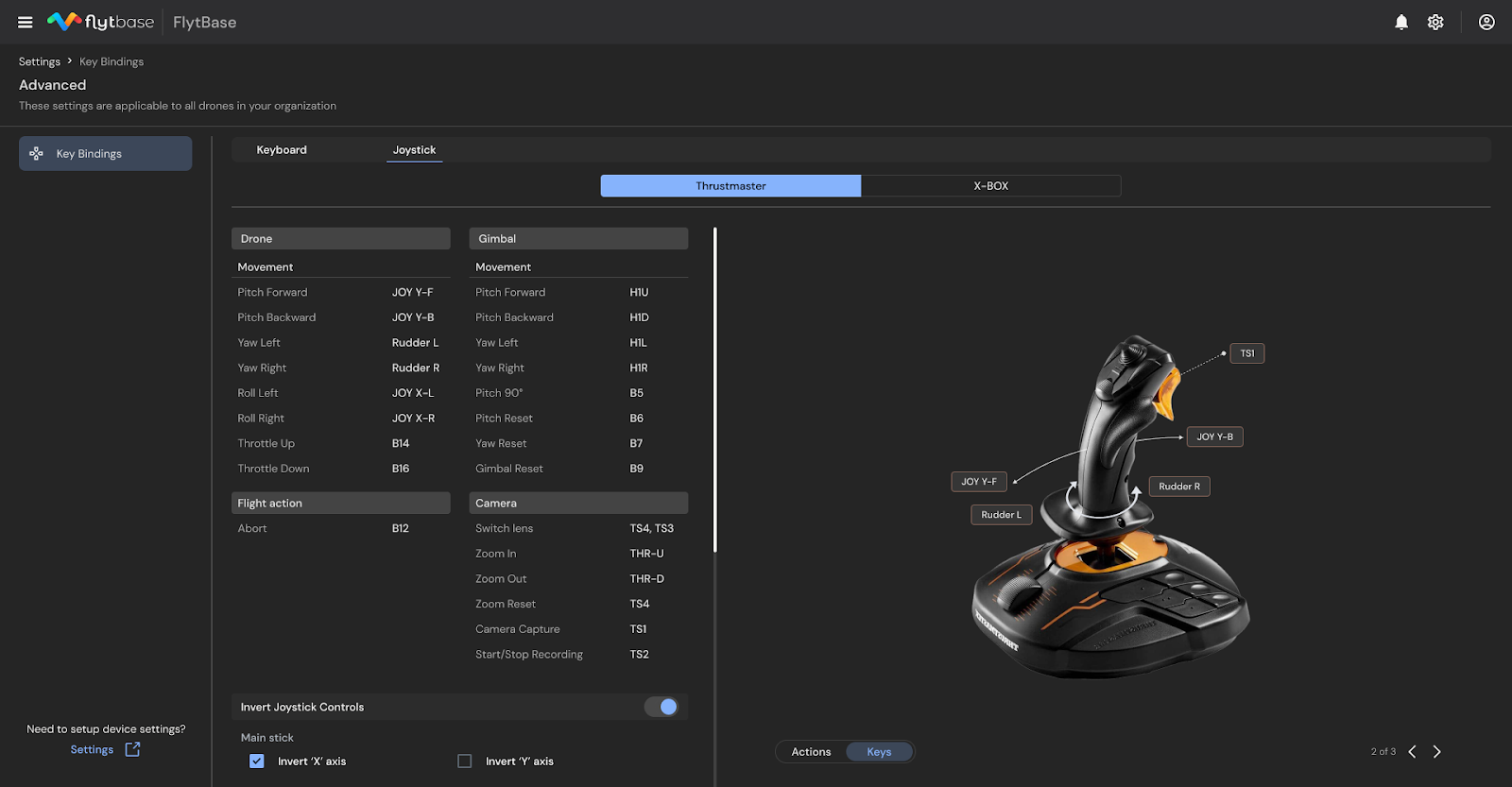
- Precision Control: The joystick's multiple axes, buttons, and programmable triggers enable operators to navigate drones with unprecedented accuracy, essential for executing complex tasks and navigating challenging terrains.
- Improved Maneuverability: The ergonomic design and intuitive interface of the joystick facilitate smooth and precise flight patterns, making it ideal for detailed inspections and operations in demanding environments.
- Revamped Key Bindings: To further personalize the flying experience, we have redesigned the Keyboard and Joystick Bindings Settings, allowing operators to tailor their control setup to their unique styles and preferences, ensuring smoother and more efficient manual flight operations.
Payload 2.0: Advanced Thermal Imaging and Sensing
Payload 2.0, brings a significant enhancement to your drone's thermal imaging and sensing capabilities. This update is particularly exciting due to the integration of the DJI M30 range finder, along with advanced thermal palettes and a split-screen display -offering a dual perspective, crucial for in-depth environmental assessment and decision-making.
- Versatile Thermal Imaging: With the integration of the DJI M30s thermal palettes, operators can now select from a range of imaging options to best suit the specific requirements of their mission. This versatility is invaluable in operations such as search and rescue, infrastructure inspections, and environmental monitoring, where clarity and precision in data interpretation are paramount.
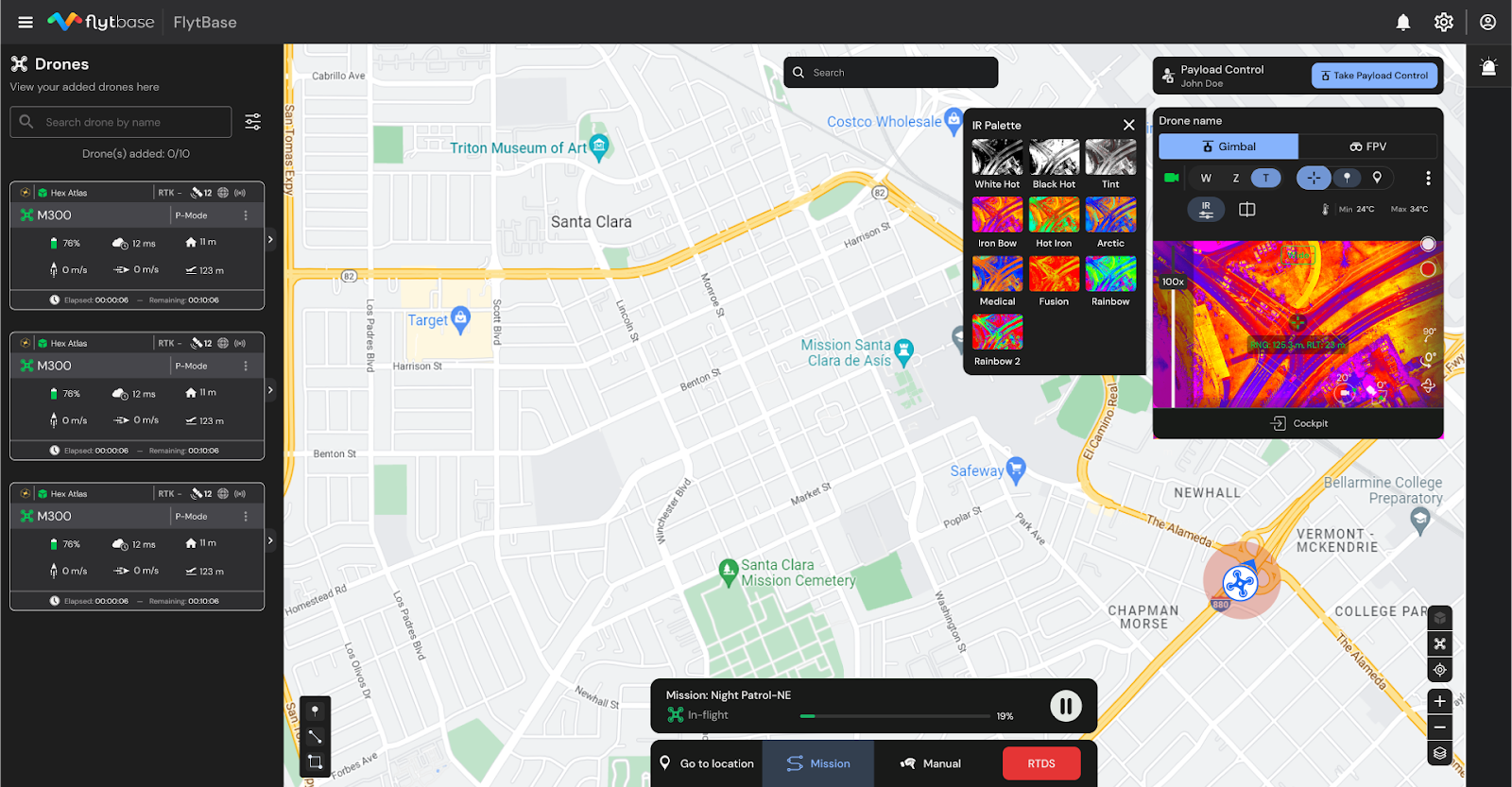
- Dual Camera Mode: Our Side-by-Side (SBS) display feature is a breakthrough in environmental assessment. Operators can now view infrared and visual feeds simultaneously, enabling comprehensive real-time analysis and fostering quicker, more informed decision-making.
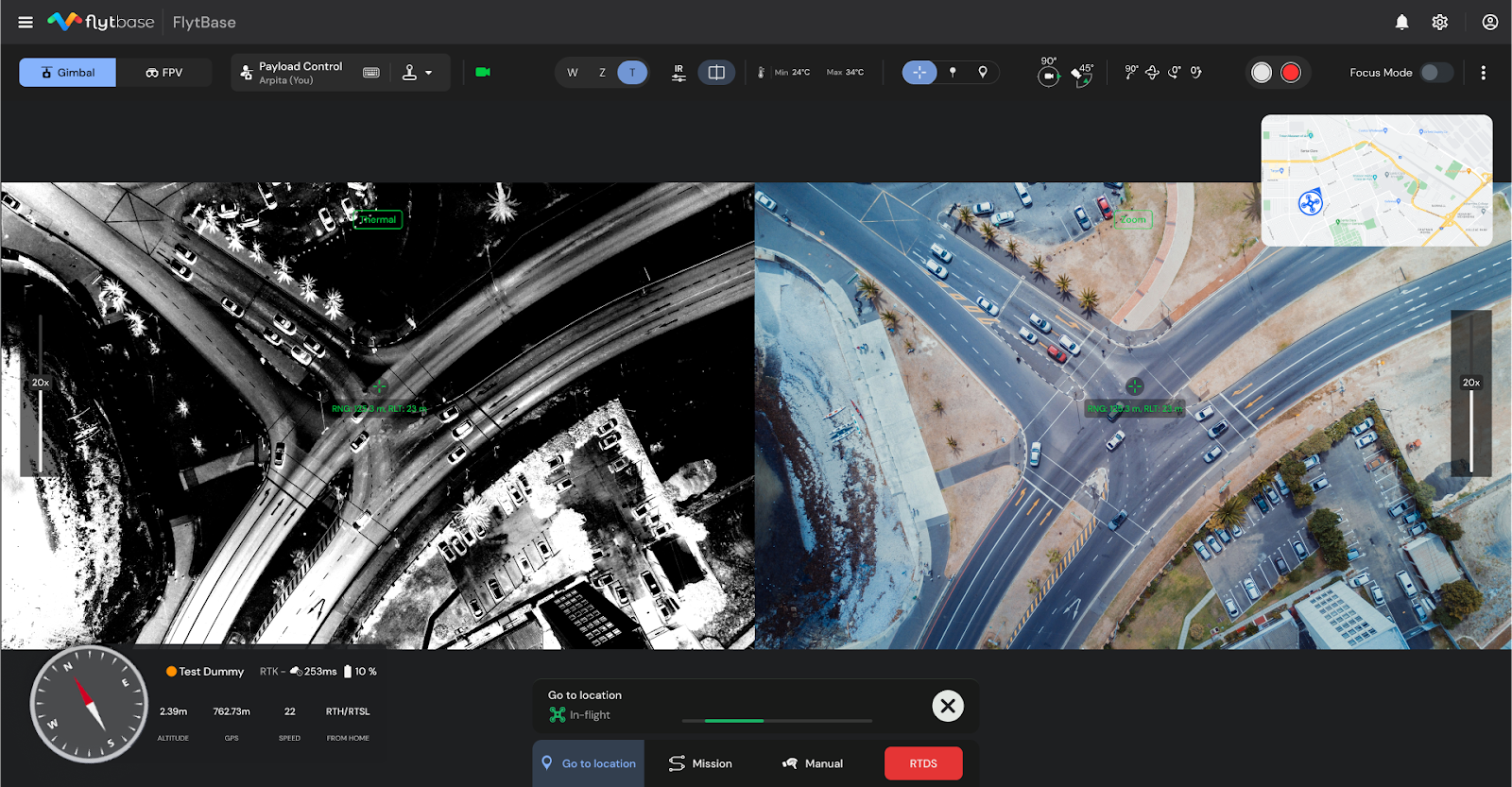
DJI M30 Laser Rangefinder support for Enhanced Spatial Awareness
The integration of the DJI M30s laser rangefinder is another highlight of this release, offering operators exact spatial awareness, a critical factor in conducting precise operations:
- Instant Location Marking: Operators can now effortlessly mark, share, and revisit coordinates and distances of key locations or objects with a simple click, greatly enhancing operational response time and efficiency.
- Precise Drone Navigation: Direct your drone to specific coordinates with laser accuracy, a feature that significantly boosts operational effectiveness, especially in complex environments.
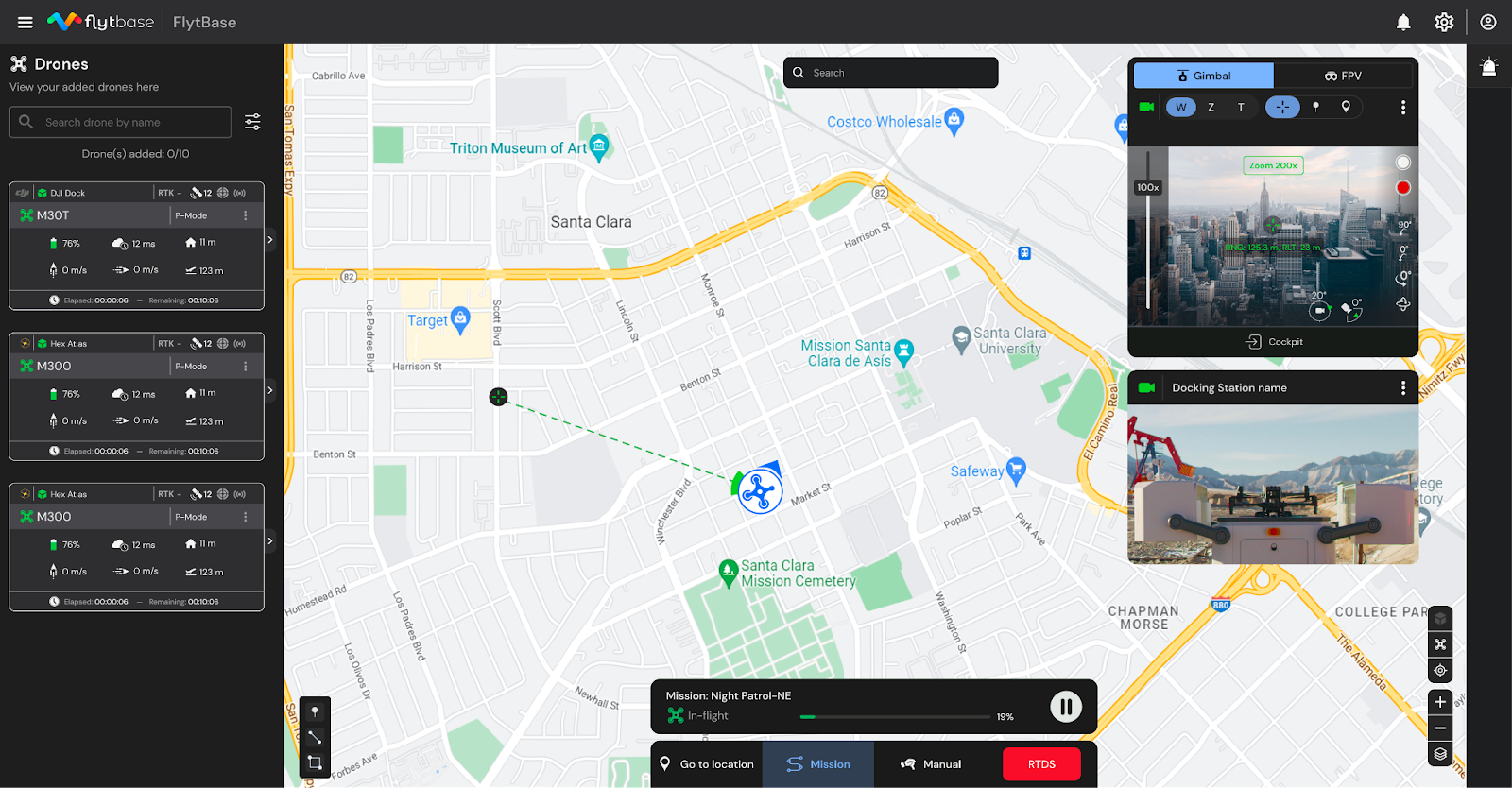
Live Map Annotations
Discover our new Live Map Annotations feature, designed to offer versatile, customizable annotation tools for enhanced mapping, precise navigation, and improved team collaboration, ensuring efficient and safe mission execution in various operational scenarios. What’s new:
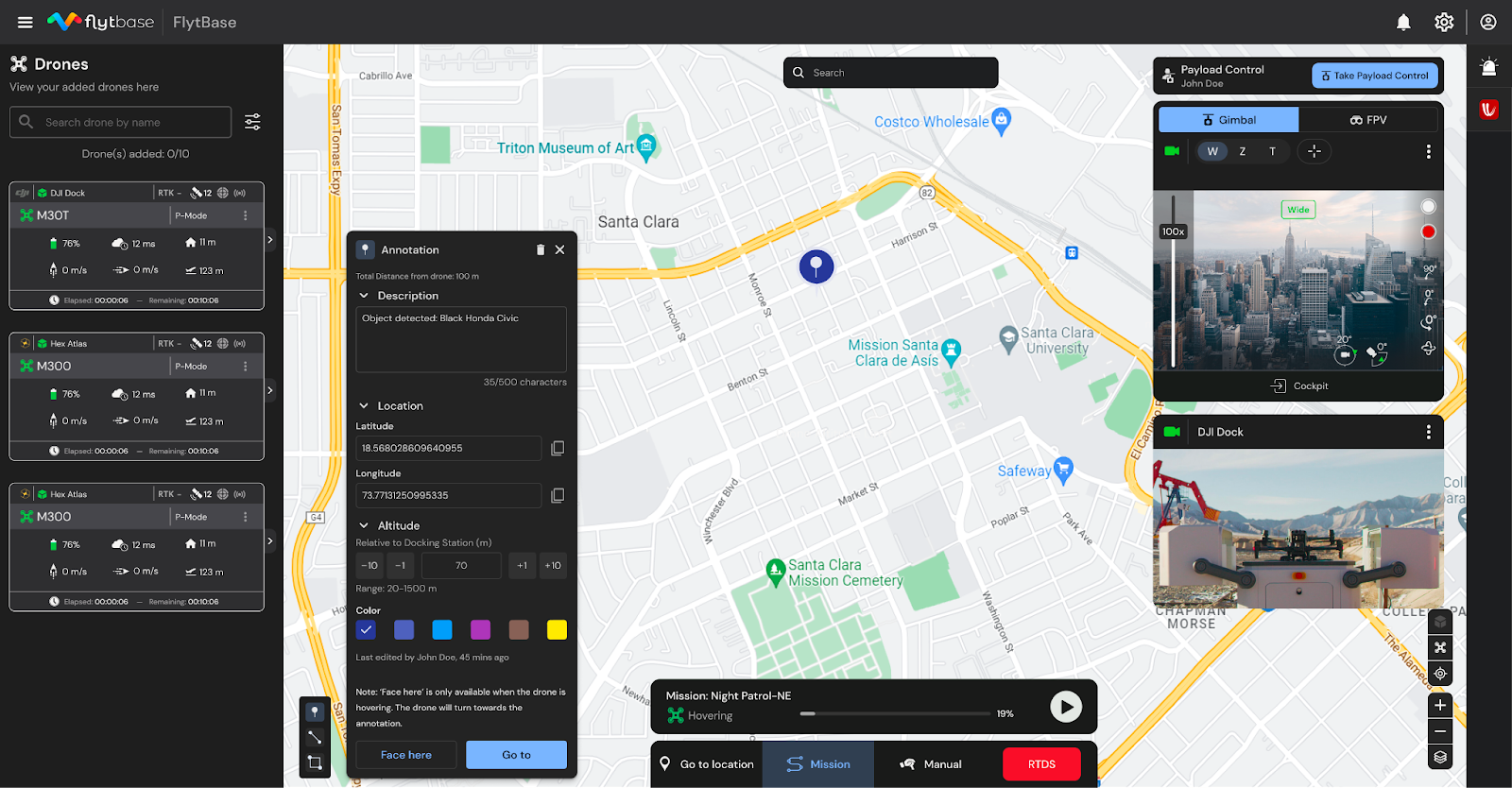
- Versatile Annotation Tools: Users can create diverse annotations - lines, points, polygons - adaptable for various missions, from search and rescue to infrastructure inspections.
- Customizable Mapping: Annotations can be customized in color, shape, and position, improving the clarity and relevance of operational maps for better planning and execution.
- Launch Drone to Annotated Locations: Annotate specific areas on the map, set altitudes, and direct drones to these coordinates, enhancing efficiency and safety in complex environments.
- Enhanced Precision with Range Finder: The integration of the M30s range finder with Live Map Annotations adds precision, crucial for operations requiring spatial awareness and accurate distance measurements.
- “Face here” functionality: Mark points on the map for the drone to orient towards automatically, useful for focusing on critical areas. This feature, coupled with the M30s range finder, which displays the distance to these marked points, providing you with a comprehensive view of the drone's position and target location.
- Streamlined Team Collaboration: Live annotations are visible in a dedicated window and on the map, ensuring swift information sharing and synchronization among team members including owners, admins, pilots, and ground teams.
Learn and Explore More
Learn how to effectively utilize these new features by referring to our in-depth guides on Enhanced Map Annotations and Thrustmaster Joystick Integration.
Dive deeper into FlytBase's extensive capabilities by checking out the FlytBase User Manual.
Have questions or feedback on optimizing your autonomous drone operations? Reach out to our team at support@flytbase.com. We're here to guide you every step of the way!