In recent years, the industry however, has faced criticism for its environmental impact and the safety of its workers. As a result, the use of more drones for mining, autonomy, and artificial intelligence (AI) in mining has emerged as a potential solution to these challenges.
During one of the NestGen'23 sessions, we spoke with Christopher Clark, CEO of Delta Drone International (ASX:DLT), a multi-national drones-as-a-service business dedicated to solving real-world challenges in the enterprise mining and agricultural industries by providing fully outsourced aerial drone data and solutions.
In the session we discussed how a combination of drones, autonomy, and AI can help mining companies address many of the challenges they face and pave the way for a more efficient mining industry.
Here’s what he had to say 👇
How a Combination of Drone Technology, Autonomy & AI are Redefining Mining Operations
Drone technology is increasingly being used in the mining sector to enhance safety and efficiency. They provide access to difficult or unsafe areas like mine pits, tailing dams, and stockpiles. Drone surveys and mapping of mining sites quickly and accurately, allow companies to generate digital surface models and digital elevation models to not only provide an accurate representation of the site but to also optimize processes such as ore extraction and waste removal.
Additionally, drones monitor mining equipment and infrastructure, like conveyor belts and processing plants, for wear and tear, enabling timely maintenance and reducing downtime.
By adding autonomy & AI to this mix, mining companies can gather data of large mine sites and monitor operations around the clock, without human operators, improving productivity and efficiency. AI can further analyze data to identify patterns and trends difficult for humans to detect. Companies can therefore have systematic data to make better decisions and reduce costs by identifying inefficiencies and areas for improvement.
As Christopher puts it, "By combining drone autonomy and AI, a unique recipe begins to take shape. We can detect people and vehicles by applying AI models to thermal imagery captured by drones. When combined with autonomous drone-in-a-box solutions in mines and dangerous areas, it enables frequent drone flights that only activate when a vehicle or person is detected, presenting an exciting opportunity for drone autonomy and AI to collaborate."
Some of the most promising applications of autonomous technologies and AI in the mining industry:
1. Safety and reducing accidents
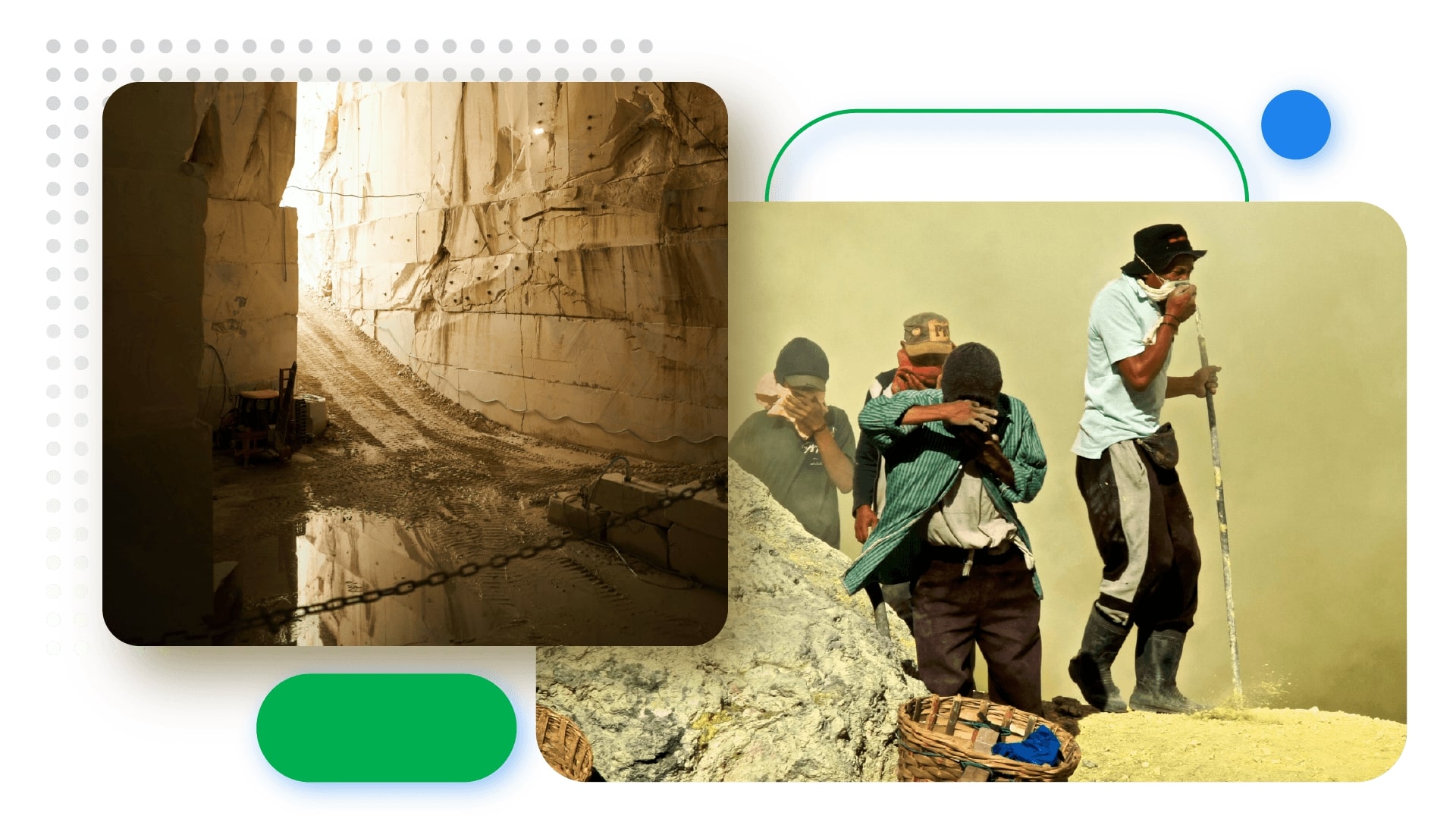
By using autonomous systems and drones equipped with AI, mining companies can improve safety by reducing the need for workers to enter hazardous areas, such as steep slopes or unstable ground. These technologies can detect and predict safety hazards, allowing for proactive measures to prevent accidents.
Just to set some context, Christopher shares a typical scenario in a mine-site - “If you wanted to calculate the volume of a stockpile and essentially how much a mine is digging out the ground, you would have to send men who would manually walk these 30, 40 meter high stockpiles. Sometimes these could be coal stockpiles really, which sort of have the propensity to spontaneously combust. So your shoes would be melting, even as you're walking over these stockpiles. And drones being able to immediately remove these types of surveyors from these stockpiles to provide them with immediate safety value. And we were very excited to see how drones have quickly become a part of the mining industry's daily routine and are only growing."
2. Productivity and efficiency
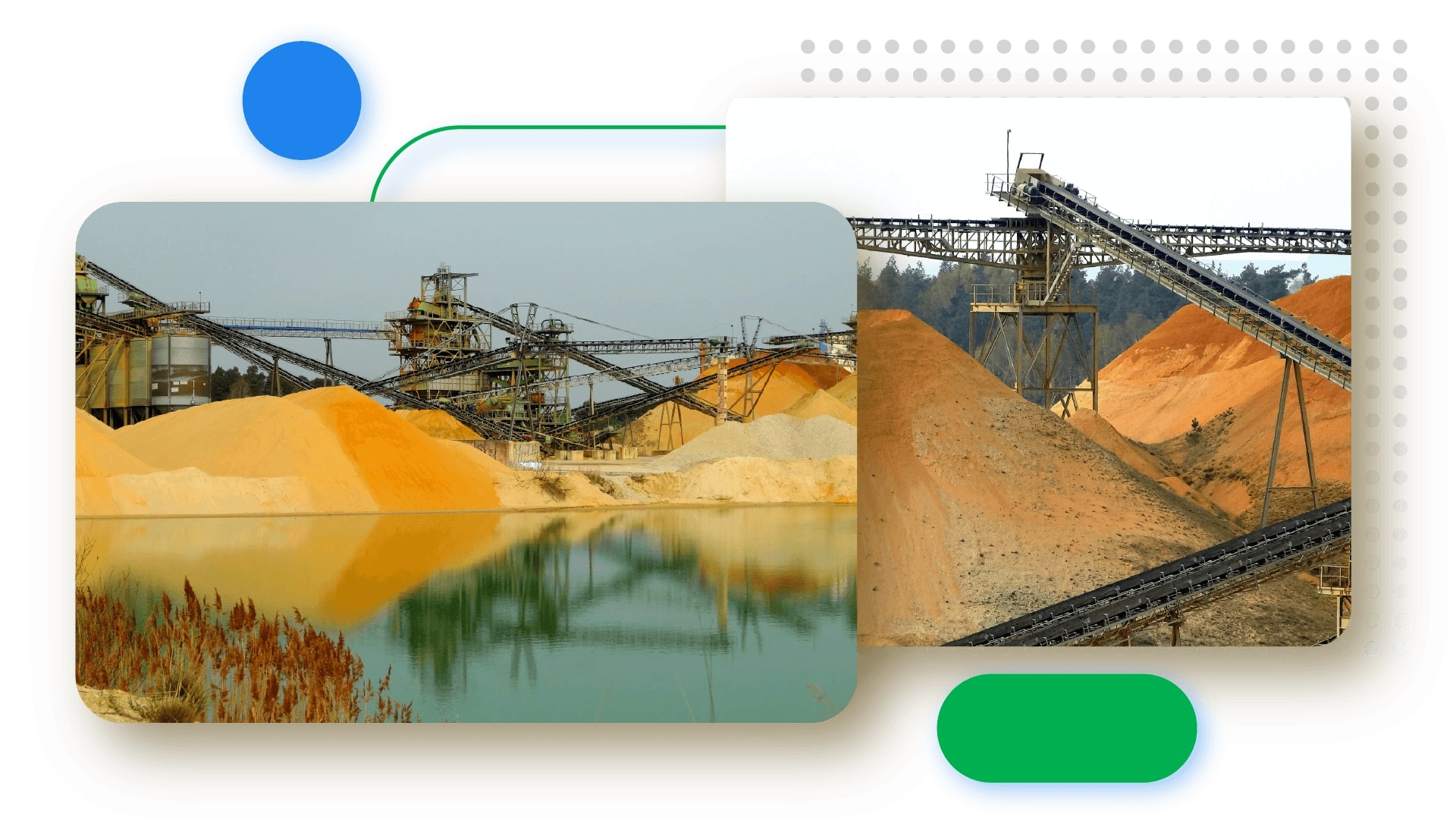
Autonomous drone systems enable mining companies to access hard-to-reach areas and monitor equipment and infrastructure on mine sites such as conveyor belts and processing plants for wear and tear, reducing downtime and preventing breakdowns. AI can further optimize mining processes like ore extraction and waste removal, leading to increased productivity and reduced costs.
3. Decreasing environmental impact and increasing sustainability
Drones and sensors monitor mining's effects on ecosystems, then AI analyzes the data to find improvements. These technologies enable targeted tracking of mining exploration' impact and efficient resource use, which minimizes damage and promotes responsible practices.
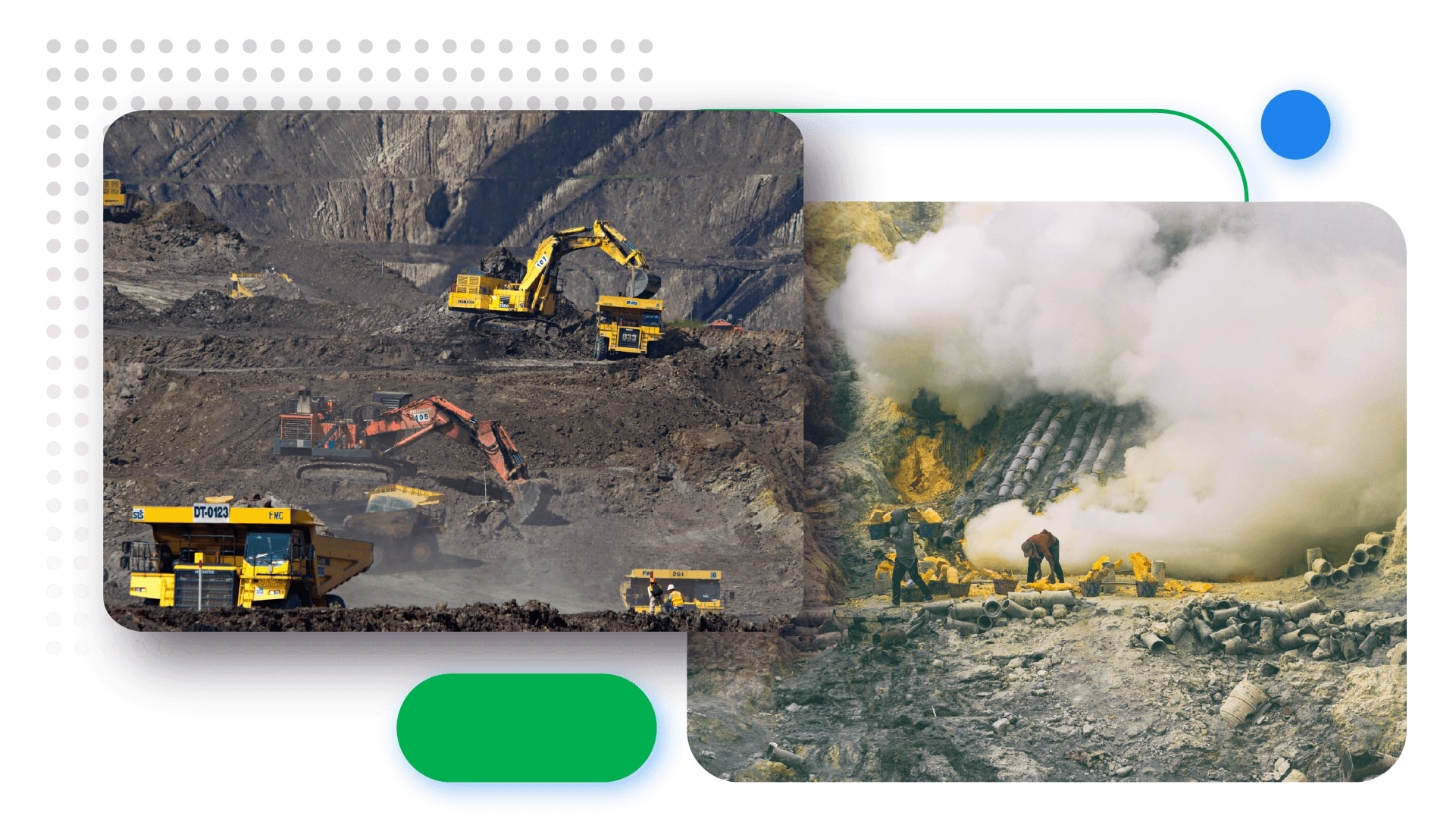
Successful Case Studies of Automation in the Mining Industry
A. Rio Tinto's Mine of the Future Program
Christopher highlights how Rio Tinto's Mine of the Future program is a successful example of utilizing technology to improve safety, productivity, and cost-effectiveness. Launched in 2008, the program uses autonomous technologies and AI to enhance mining processes. By incorporating autonomous trucks, drills, and trains, the company has decreased the number of workers on-site, while simultaneously improving safety and efficiency.
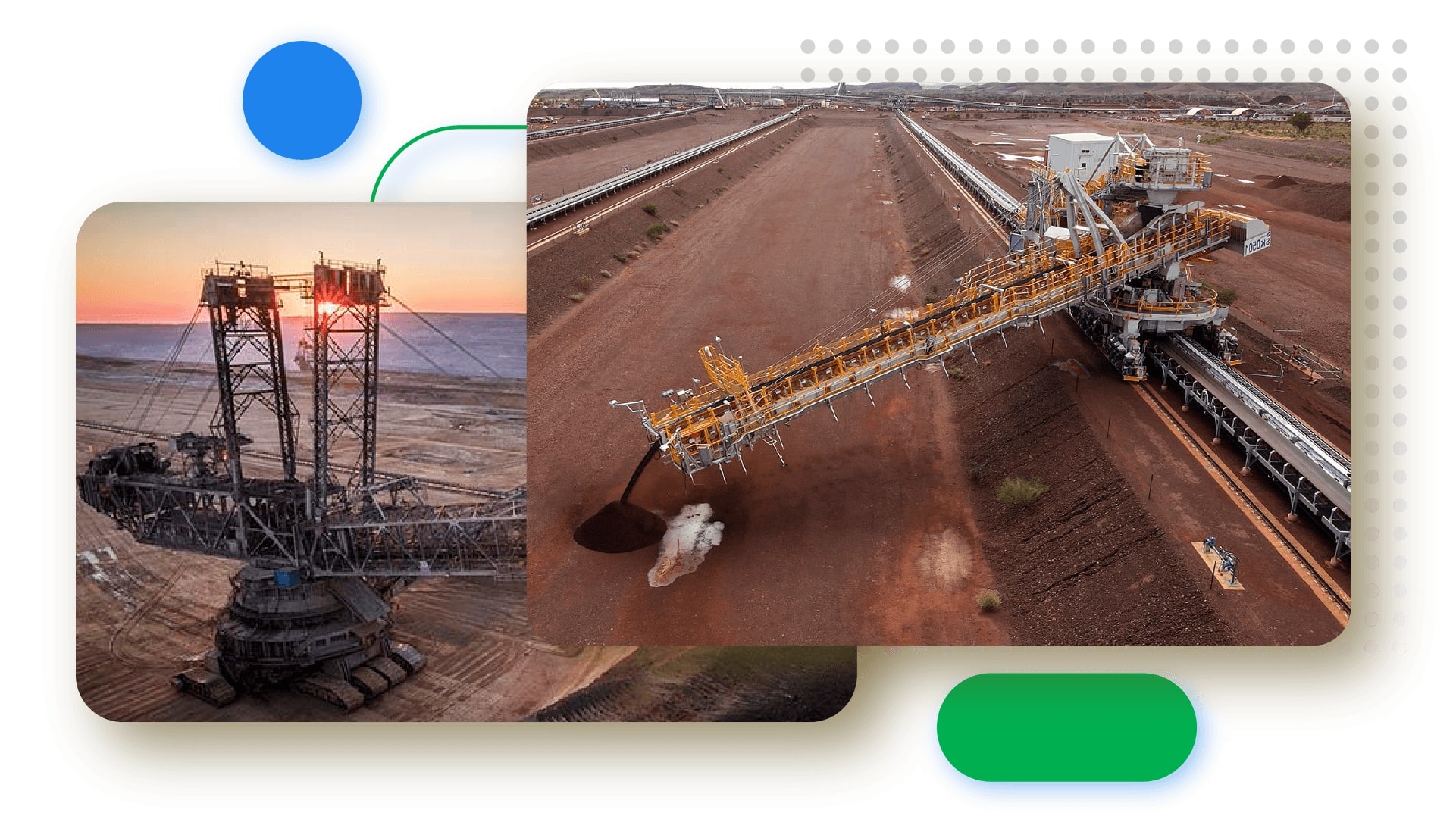
The Gudai-Darri Mine in Western Australia is an impressive instance of this program, as it is fully autonomous and remotely controlled from a central operations center, where workers monitor the mine's operations and make real-time decisions based on data gathered from sensors and cameras.
This mine has been very successful, with Rio Tinto reporting significant value and improvements in safety, productivity, and cost reduction. With the use of autonomous technologies and AI, Rio Tinto has been able to minimize waste and increase accuracy in mineral extraction, resulting in better efficiency and productivity.
B. Barrick Gold’s Digital Transformation
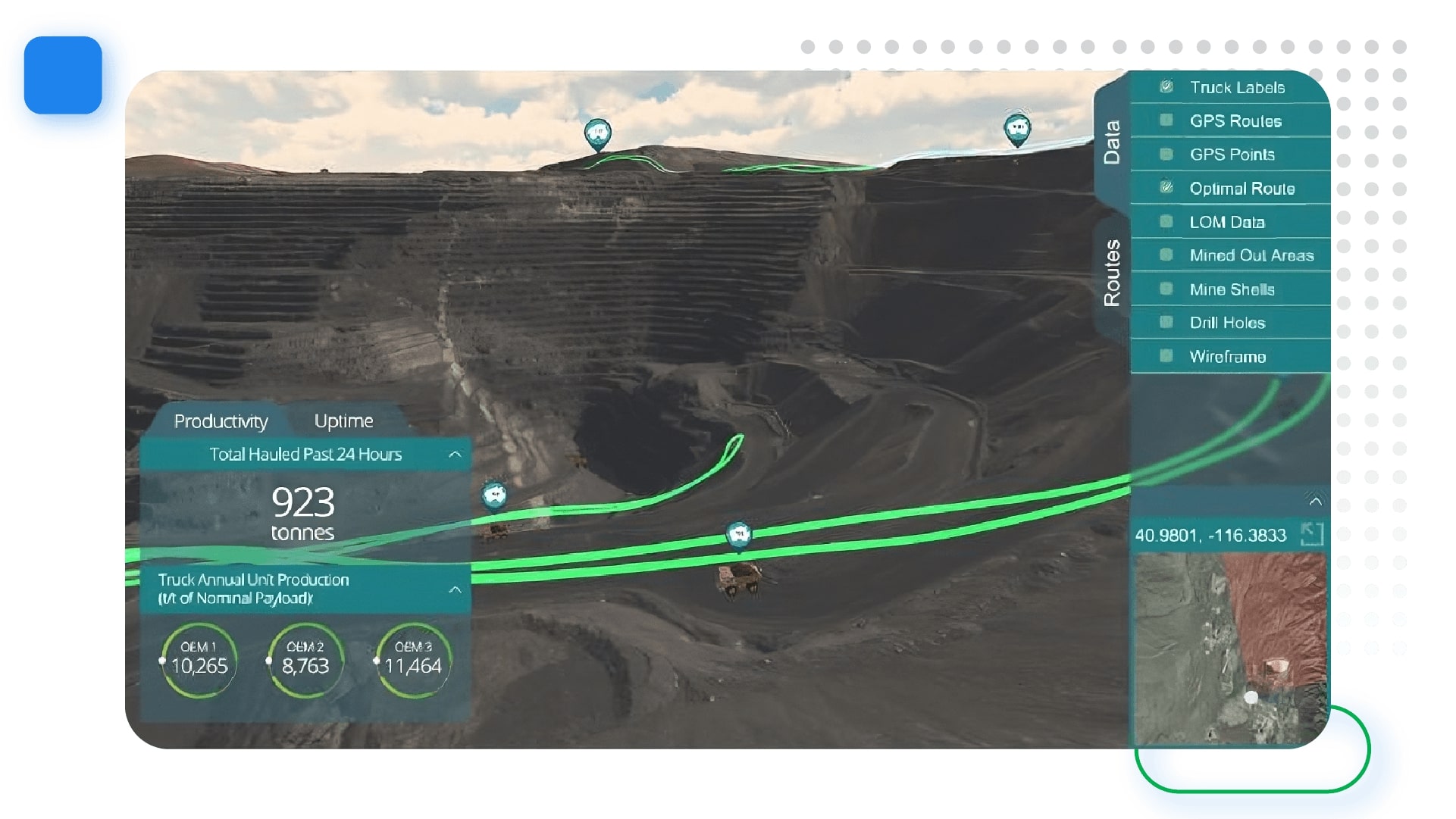
Barrick, one of the world's leading gold mining companies, has implemented a range of innovative technologies to improve safety, efficiency, and sustainability in their operations. These include:
- Autonomous Haulage System (AHS): Powered by advanced sensors and GPS technology AHS allows the trucks to navigate the mine site and transport materials safely and efficiently without any human interference.
- Predictive Maintenance: Using data analytics, Barrick anticipates equipment failures before they occur. This allows for proactive maintenance, reducing downtime and improving productivity.
- Real-time Data Analytics: The company has invested in a real-time data analytics platform that enables them to collect, store, and analyze data from every stage of their mining operations. This allows for more informed decision-making, optimization of processes, and better resource allocation.
- Digital Mine Planning: By using advanced digital mine planning tools, Barrick created accurate and detailed models of the mine site, optimizing the layout of equipment and infrastructure, and minimizing waste and environmental impact.
- Safety Improvements: Barrick has implemented a number of safety initiatives, including the use of wearable technology to monitor workers' vital signs, real-time monitoring of hazardous areas, and the incorporation of safety protocols into their autonomous technologies.
FlytNow for Autonomous Drone Data Collection
Automation software such as FlytNow, enables businesses to deploy drone fleets on routine missions to capture visual data in real-time. Mine operators can schedule missions at a regular interval to track the progress of work in mining sites from the comfort of their offices.
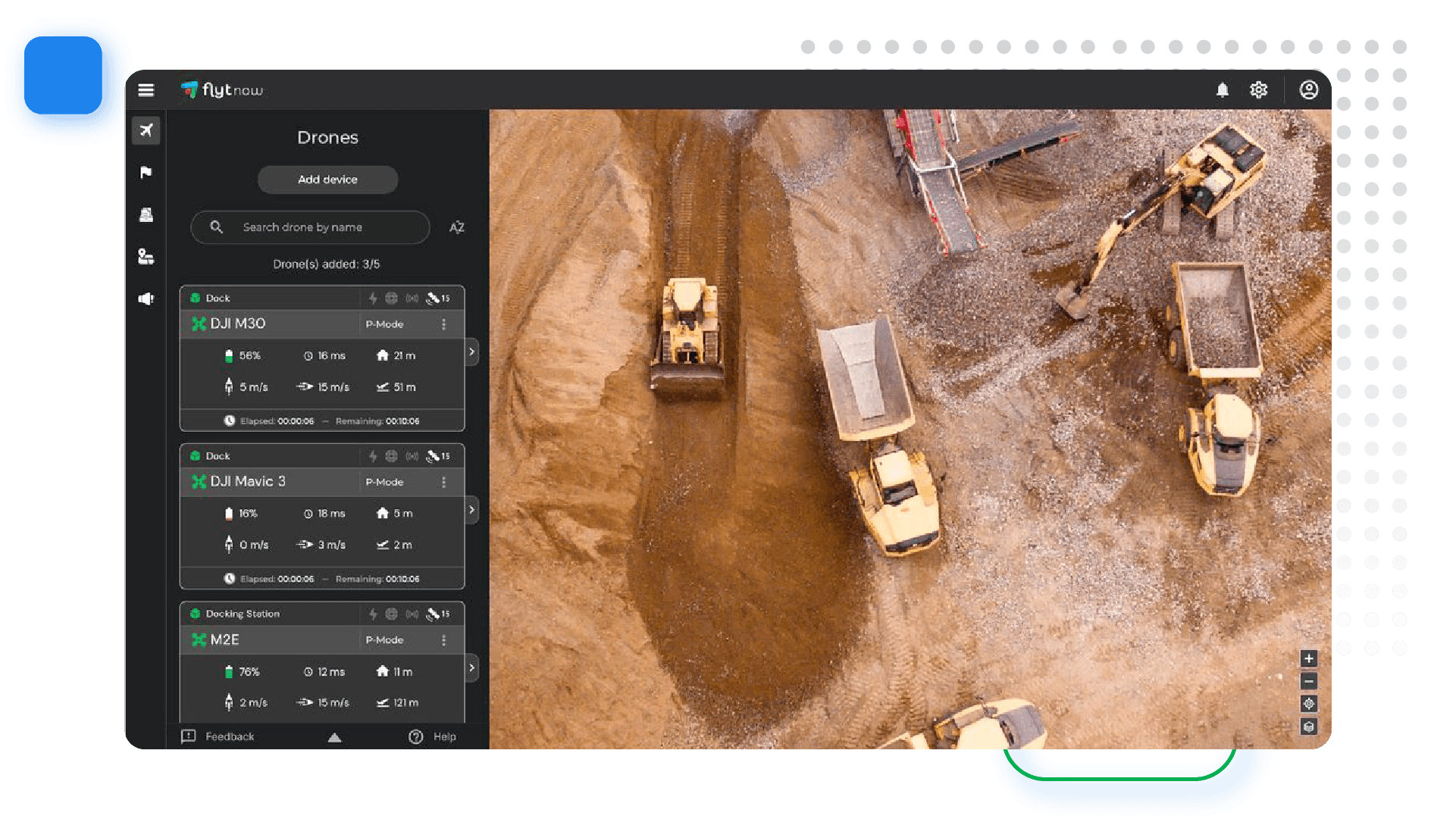
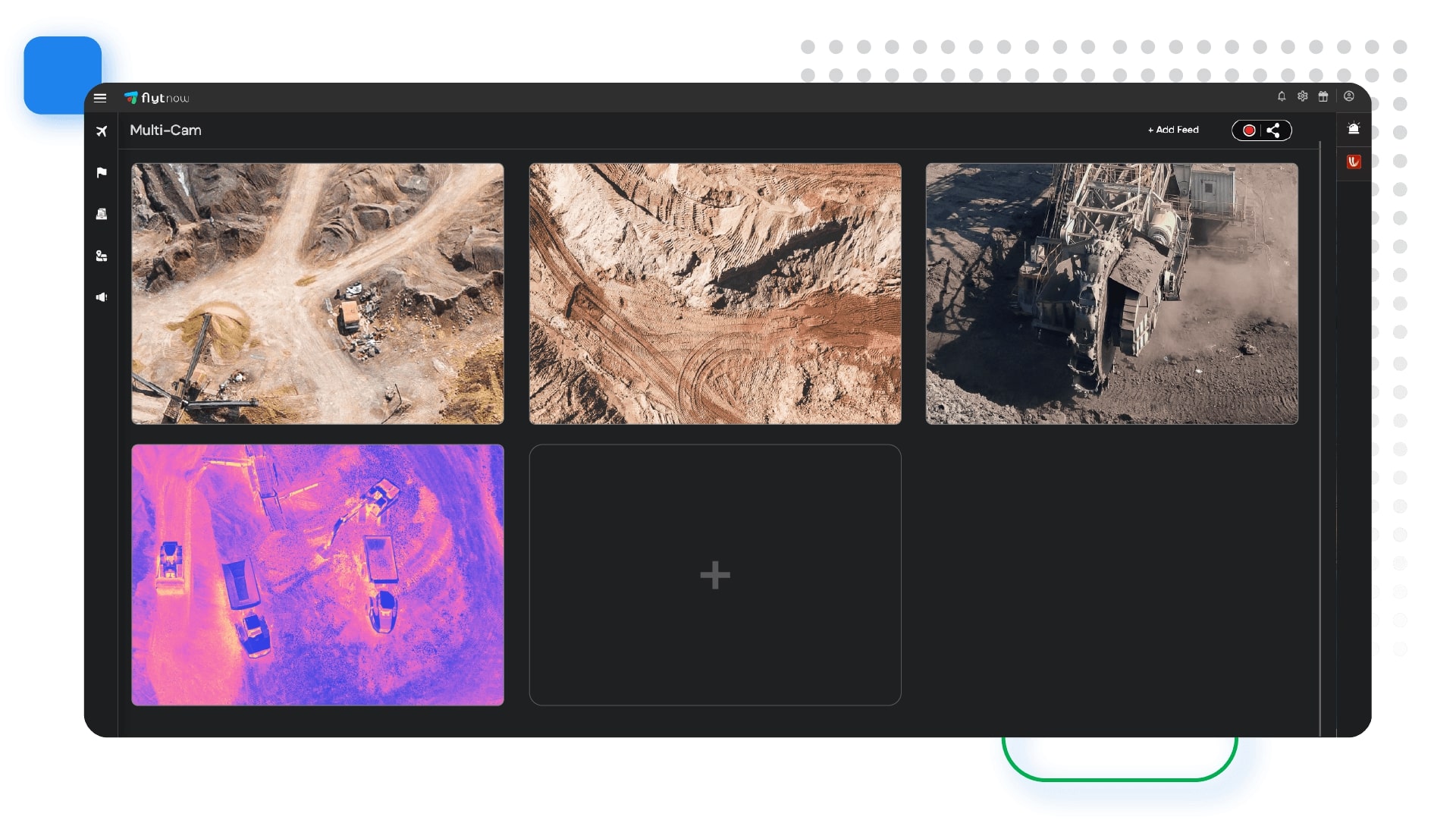
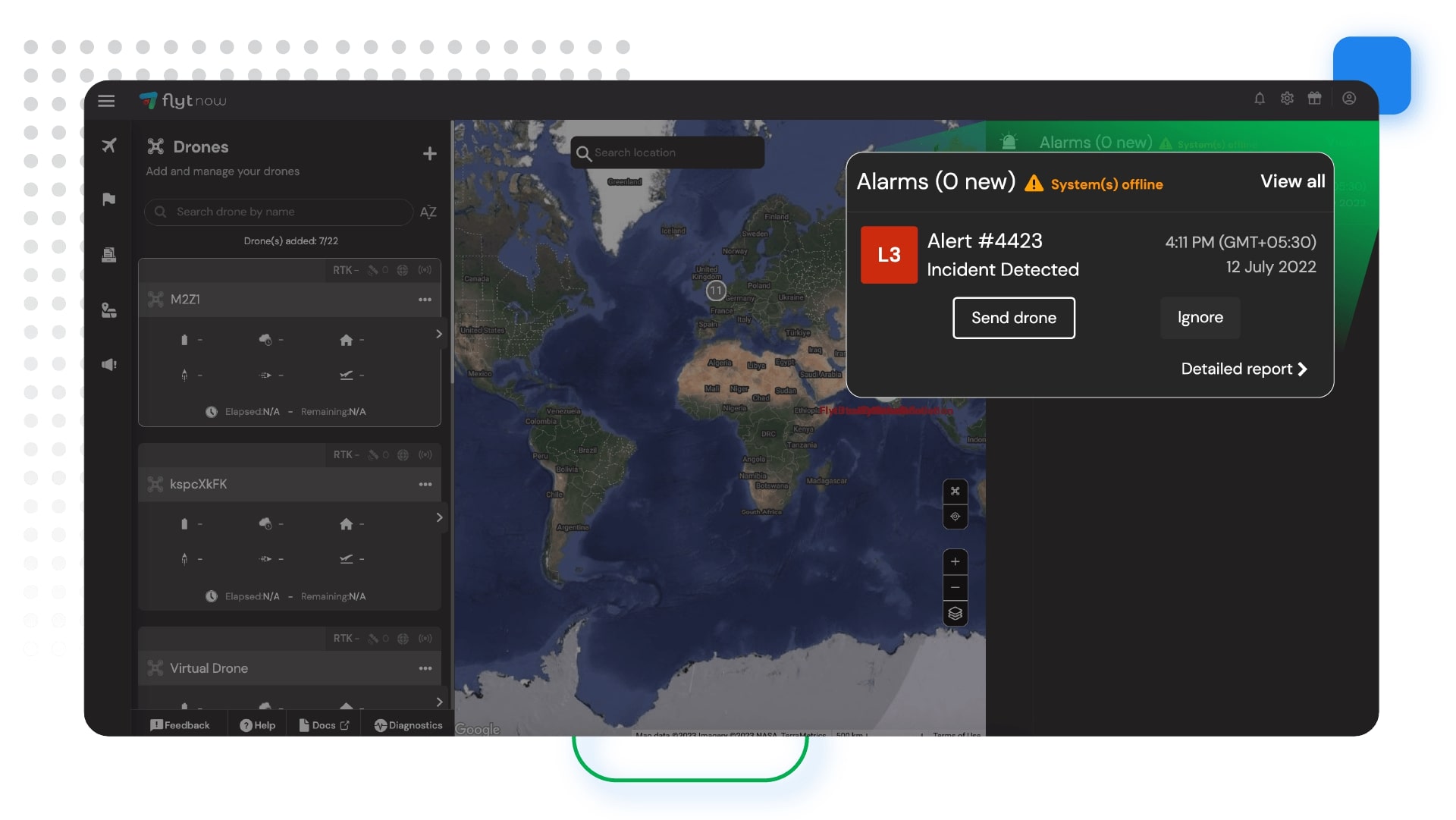
Apart from rapid data collection, FlytNow enables companies to integrate alarm monitoring systems, which enable drones to autonomously take off from docking stations, fly to precise locations, capture video feeds, relay them back to the command center, and return to the docking station without human interference.
This feature provides mine operators with quick access to accurate incident reports, allowing them to respond promptly and effectively to any issues that arise.
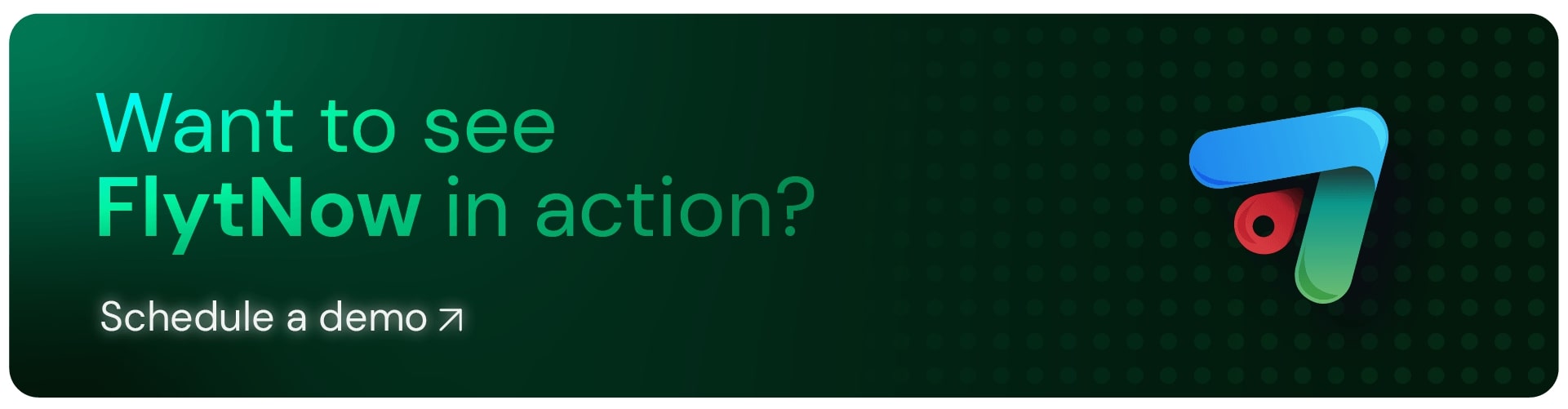
What's Next?
As with all disruptive technologies, the mining industry needs to overcome several challenges in implementing autonomous technologies and AI. While the benefits of these technologies, such as faster data insights, improved decision-making, and increased safety for workers, are vast, mining companies must also overcome regulatory hurdles, invest in necessary infrastructure and expertise, and ensure compatibility with existing systems. The adoption of these technologies promises to revolutionize mining processes, making them more efficient, productive, and safer.
It is worth noting that autonomy in mining applications will require a higher degree of analytical and electrical skill sets, but it does not necessarily mean a reduction in the workforce. Furthermore, the interoperability with downstream technologies such as wearables will empower situational awareness and safety. With proven platforms, drone swarms or fleets will unlock logistics and on-site deliveries for mine employees, leading to more streamlined operations. Overall, the mining industry's adoption of these technologies will enable them to remain competitive and better equipped to face the challenges of the future.