Just in time for ArduCopter shipping, magnetometer boards are back in stock. Works great with APM, ArduCopter and ArduIMU.
All Posts (14048)
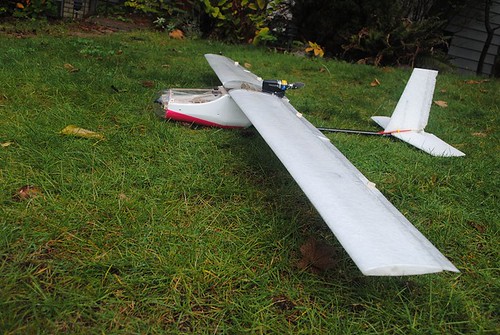
Expanded polypropylene is highly desired for fabricating small remote control airplanes and uavs . Its high impact stability low material cost and low weight makes it very good for this role . However the two main ways of manufacturing parts from the raw material have drawbacks . Molded EPP makes a great finished product and can be produced in many shapes including compound curves and can have a smooth finish. the major drawback is the high cost of producing the molds and the production machinery. The other method used is hot wire cutting . the start up cost is much less expensive, however it cannot produce compound curves and the finish is very rough, which can produce unwanted drag in an airplane design.
Wanting the best of both worlds , I came across this blog on what has been termed " the new stuff ". I ordered a couple roles and began playing with it when it arrived. I was very impressed and decided to use it on my next version of the techpod it went on like butter , very smooth , easy to manage wrinkles and adds much structural strength to the EPP. over all this technique is about the same weight per square inch of wing as molded EPP.
I am very please with the outcome and very happy to share this with the hobby uav community at large.
Read more here http://community.evuas.com/pg/blog/EVUAS/read/205/epp-covering-technique-the-new-stuff- and yes i will be offering small quantities at good prices on the EVUAS store soon
Full autonomous flight of the TrIMUpter UAV with automatic landing
Here the video of the 1st full AUTONOMOUS FLIGHT of the UAV TrIMUpter with AUTOMATIC LANDING controlled with a 9 DOF IMU and a GPS...
Electronic setup used:
- ArduIMU+ V2 flat (a 6DOF IMU)
- HMC 5843 triple axis magnetometer
- GPS EM406 SirfIII
- 3 brushless motors Hextronik 1300 Kv, HXM2730-1300
- 3 ESC Hobbyking SS Series 8-10A
- 1 servo Corona 919 MG 1.7kg/ 12.5g/ 0.06sec
- 1 Lipo battery 3S1P 11.1V 1500mAh
- 3 propellers CCW GWS EP0843
Firmware: TriStab v2.3 JLN
More info at: http://diydrones.com/profile/JeanLouisNaudin
I’ve made a small program that can be used to upload your own c code to arduino boards using the bootloader. That means you don’t need a flash programmer. I
made it for my own use and found it pretty useful. So now I’ve
made a more user friendly version..
To use it simply start XLoader.exe, pick a hex file and press upload. That’s it.
Hope you find it useful... Or am I the only one using AVRstudio to program my uav??
As you can see it's still early alpha, so there might be some bugs. Please contact me about bugs or suggestions.
http://xloader.russemotto.com
From a recent AMA Executive Council meeting:
"MOTION V: Moved by G. Fitch (II) and seconded by J. Rice (VIII) to change the name of the Experimental Aircraft program to Large Model Aircraft program. Additionally, pending approval of the regulations and insurance, increase Large Model Aircraft program (formerly Experimental Aircraft program) maximum weight from 55.1 lbs.-100 lbs. to 55.1 lbs. -125 lbs. for propeller-driven aircraft, and, 55.1 lbs. to 100 lbs. for turbine-powered aircraft." (bolding mine)
Is this their way of saying, "Lets really annoy the FAA!" ?????

Chase Cam

Overhead

I'm still fighting the "range" problem if the user wants to manually zoom in or out after selecting a view.
Jordi showed his electronic 3D Robotics facilities some weeks ago and Chris posted some more after he visited there, now It's time to give quick look on how Fah Pah Electornics facilities looks like and where the magic happens for ArduCopter frames and other parts.
Small history about early dates and today: Earlier Beta frames were made in smaller scale and without proper production facilities on my friends office but now that we are doing them in a bigger scale and we want to provide good and reliable service to all DIY Drones customers, we needed to have proper production and storage area. So me and my partner created another division under Fah Pah Elecronics Co., Ltd. (Btw. Fah Pah means Thunder/Lightning in Thai language).
We had a possibility to get another office area from same building where main office is, so we got it and did move all Drone/UAV production/packing/shipping there. Also to make life a lot easier on people on main office where all electronics design and assembly is done, I was driving them crazy running CNC's all day long.
And now finally we can start show how things looks like and where the magic happens. There are another factory that does all fiberglass/polycarbonate parts for us. On this area we make all smaller parts and packing/testing/shipping.
Picture: 3 weeks ago when first furnitures started to arrive:
Because we were in hurry to get production up and running so people can start flying their ArduCopters as soon as possible, we created temporary walls around CNC machines to keep voice down.
Picture: CNC cuting room where all small parts are made. Even tho there are automated machines, a lot of hand work is done to get them ready
There are now 3 table size heavy duty CNC machines running constantly and doing various parts. Covers are still missing around CNC routers so it's rather noisy room when all three are running at full speed.
Material size that we can use on those is 30 x 60 x 7 cm and they cut even 3 cm stainless steel.
(Mr. PIK examining cut quality on motormounts or something else parts)
Other tools that we do have is milling machine, grinding machines and polishing machines. Plans are to have few more tools to help on some production issues. Like belt saw, air compressor etc.
Picture: Preprocessor software for CNC routers, Mach3
Softwares that we are using on production floor are:
- Mach3 - CNC processing
- ArtCAM - CAD/CAM drawing and design
- Cut2D - CAD/CAM drawing and design, mainly for importing simple customer drawings
Picture: Storage shelfs are starting to get populated (filling up more every day)
Picture: Closeup for motors and other parts for ArduCopters
Picture: Packing are is used to unpack nuts/screws and propeller shipment that arrived today (16th of Nov)
Picture: People always says that it's hard to find CW & CCW propellers, not anymore.. We have them now and more will come :)
Video: Last but not least... Quick video tour to production floor. (Watchout, loud noises)
There are still many things to do before shipping will start, but it is close only few items are missing and they should arrive this week Thursday.
Many things are still looking their places on this production floor and many issues still needs to be resolved but over all it's looking rather ok.
If you have a good idea or needs, share it, maybe some one else has similar needs.. Also if you have special needs, just ask and we can look what we can do.
Few more picture will come after packing has started to show how new packets and contents will look. Not any major changes on beta frames but still :)
Happy flying guys & gals...
and remember.. fly safe.
gopro above sunset horse ranch from Quadroid on Vimeo.
here is a pleasant suprise while hovering above the tree tops in hollywood, CAHi,
this are the DXF Files for the Ardu and Mega BOX
it is made of 3mm Plywood
have fun
Peter
OK... It is only a doppler effect speed radar... but it is still a radar, with microcontroller. It is pretty light weight (3.7 onces) and not to expensive ($199). It as a range of half a mile when targeting a car size object (Maybe we can enhance that range...). If some potential is expected from you guys about that product, I may be willing to bail out some money for it.
Hope you enjoy the challenge.
- ArduPilot Mega – $60
- IMU Shield – $160
- 3×8 Angle Connector x 2 – $4
- Servo cables x 8 – $12
- GPS – $86
- XBee-PRO 868 x 2 – $140
- Xbee adapter x 2 – $50
- XBee ground antenna – $11
- FTDI cable for ground Xbee – $18 (really, too much for that simple piece of hardware)
Reasonable minimum. Without directional antenna, camera or FPV. $541 without shipping.
Would be good:
- Airspeed sensor – $20
- Tubes for airspeed – $6
Another $26.
Would be really cool:
- Magnetometer – $45
First up I have to give a big thanks to the DIY Drones community for developing such a great system, particularly the support documentation. After setting up, tuning and test flying APM the last few months, I have now had many long auto flights with this aircraft without a hitch, with the longest being around 15km.
The aircraft is a 1940's design Trenton Terror originally for free flight. This particular airframe is 20years old and still going strong. Wingspan is 2m, All up weight is 2.2kgs. Powerplant is an electric .32size rimfire outrunner turning a 14x8 prop. I normally run it on a 5Ah 3cell lipo, giving it an endurance of around 25-30mins in a 40kph cruise
Along with APM, I have also installed a 2.4ghz Video link, with a Remzibi OSD.
Belly mount camera
The Trenton Terror prior to being refurbished for APM testing,
I am almost sure about it, first venezuelan to use ardupilot (i hope so).
Ran my first tests in my workshop, turned everything on, including the xbee telemetry, and it worked like a charm!!!!! it is awsome....
The arduIMU works perfect, i am impresed of the sensitivity!!!!!! GPS locked in 1 minute!!!
Now i have to permanently install the electronics in the UAV and run a few more tests, one of them is to figure out how to make it work with my "V" tail, i have been reading the codes and it mixes only the channels 1 and 2, and my tail meeds to mix the channels 2 and 4!!!!!!
Still have more things to do, but i think that this weekend i will start to configure the ardupilot on the field...
I allready have the video tx working, still waiting for my Remzibi´s OSD!!!
Diego Colonnello
""" very happy"""
The AMA just announced that the Federal Register (item #19 here) is wrong and the AMA knows that the NPRM is going to be out in June. Meanwhile the Governement records indicate the process is running on schedule for NPRM release in March.
The AMA is telling everyone that the AMA knows more about the situation than the governement itself.
The AMA claims the FAA "reconfirmed" the July or later dates last week, but provided no document or FAA source to support that claim.
So who is spreading misinformation, the AMA or the Federal Register ? I let you decide.
From the AMA (bolding mine):
"Over the past week there’s been a fair amount of speculation and misinformation on the internet regarding the proposed date for the sUAS Notice of Proposed Rulemaking (NPRM). There have even been assertions that the public comment period for the proposed rule has come and gone. Nothing could be further from the truth. In December of “09”, the FAA announced its target date of June 2011 for the publication of the Notice of Proposed Rulemaking. This is the date the proposed rule will be noticed (posted) in the Federal Register and the point at which the public comment period will commence. This date was reconfirmed last week by the FAA Unmanned Aircraft Program Office; if anything there’s the possibility this date could slip into July or even August.
So what caused all the fuss… ?
Well, the misunderstanding stemmed from a notice in the Federal Register posted in accordance with the Regulatory Flexibility Act (RFA). The RFA requires agencies to publish semiannual regulatory agendas in the Federal Register describing regulatory actions they are developing that may have a significant economic impact on a substantial number of small entities. The Act also requires the Office of Management and Budget (OMB) to review and comment on proposed rules with the potential for such an impact.
FAA posted its regulatory agenda relating to the sUAS rulemaking earlier this year. The rational for an RFA review was based on, “the novel legal or policy issues about the minimum safety parameters for operating recreational remote control model and toy aircraft in the NAS”.
The March 2011 date in the Federal Register relates to OMB’s review of the proposed rule under the Regulatory Flexibility Act. This review occurs before the proposed rule is published in the Federal Register and opened for public comment. Again, we expect the NPRM to occur in June 2011.
Please continue to check the AMA webpage for the most current sUAS rulemaking information. Timely alerts are also available on the web or on your cell phone at: Twitter.com/amagov "
Mikrokopter hexrotors by way of Aerobot; swimsuits from Hive Swimwear. (via BotJunkie)
enjoy...
Do you have an Ardupilot Mega and shield and want some fun for little money? check this tiny quad... my last drone in family...
Some specs:
- Size : 26.5cm (10.4 inches) from motor to motor
- Motors : 18-11 200kv 10 gram motors
- Props : 4x2.5 (standard CCW props)
- ESCs : Turnigy 6A
- Battery : 3S610 (or 3S800)
- Sonar : Maxbotics LV-EZ0 [optional]
The nice part about this frame is that it use standard kite parts, so it´s very easy to construct and it´s perfect for some radical tests.
Itried to find a bit different design that also make the quad less simmetrical (it´s very easy to loss the orientation with a quad) and I wanted to do as small as posible to flight indoors...
At this size and weight it´s very safe and robust also. The props use prop savers and this help a lot in crashes...
I am not very good writing... so I took a lot of photos during the build phase and I created a build log: https://docs.google.com/document/d/1fIZL-Ca2fx2RPhBQLzoOdqdCuikXRKePwKbxDlJWiss/edit?hl=es
This code supports a sonar for altitude hold and also has a battery alarm (2 alarms).
Thisquad works with ArduCopter code, but because how main board is mounted, actual code doesn´t work. This is the code that I used with this quad :
http://code.google.com/p/arducopter/source/browse/#svn/branches/Arducopter_indoor
(as zip format: Arducopter_indoor.zip )
note that this will be integrated on main Arducopter code. Now is temporarily in a branch.
ThePID gains are different than in standard ArduCopter, so you need to Initialize EEPROM on Configurator or put this ones manually:
-Stable mode: P : 4.8 ; I : 0.12 ; P_rate (D in configurator) : 0.4 ; Yaw : (4.5 ,0.15 ,2.8 )
-Acrobatic mode : P : 0.75 ; I : 0.1 ; D : 0 ; Yaw : (2.4 ,0.2 ,0 )
OK, but was all so perfect like in the video? I don´t believe that...
Yes, you are right, but fortunately this design is very crash resistance... and this part is also fun...
After all this battles I only needed a few drops of ciano in the crash with the lamppost :-)
What´s the real size?
On center, standard arducopter frame, on left, old ArduIMU quadcopter part III, on right-top this project.
And what about the automatic aerobatics on video?
I am starting to test a new function to do automatic aerobatics (Automatic Aerobatic Procedure). The idea is that you enable this function with a switch in the Tx to make an automatic predefined aerobatic and then automatically recover to a stable mode.
Thisis actually a proof of concept but works very nice. One limit here is the maximun rate of the gyros, in our case 500deg/s. If we exceed this, the IMU get confused...
An interesting point to note is that the IMU doesn´t loose the orientation in this hard movements...
Thestory is that I have never feel too much confidence doing flips manually with quads. Then I start thinking that with an automatic code we can get a precise timing and controled movement so maybe this could help to do better aerobatics. I started testing this function outdoor, on an open field but I was improving the code and got more tightly maneuvers, so tight, that I ended up doing flips with a quad inside my room!!!
Here is the code I was testing : (AAP function: AAP.txt )
I implemented this functionality as a state machine where there are three kind of states:
- fixed commands for a limited period of time. (example : Apply a throttle command)
- fixed commands until we reach some IMU state (example : roll until we reach a certain angle)
- And a mix between this categories and a control (example : Throttle command + stable mode on roll, pitch, yaw)
There are many things to test and improve here but the basic concept works very nice...
If I can get a bit of help from a friend, I will probably made a carbon fuselage for this prototype...
Enjoy this “Science & Fun” mix...
Jose Julio.
Arducopter Team